Best Practices For Extending Expander Tool Life
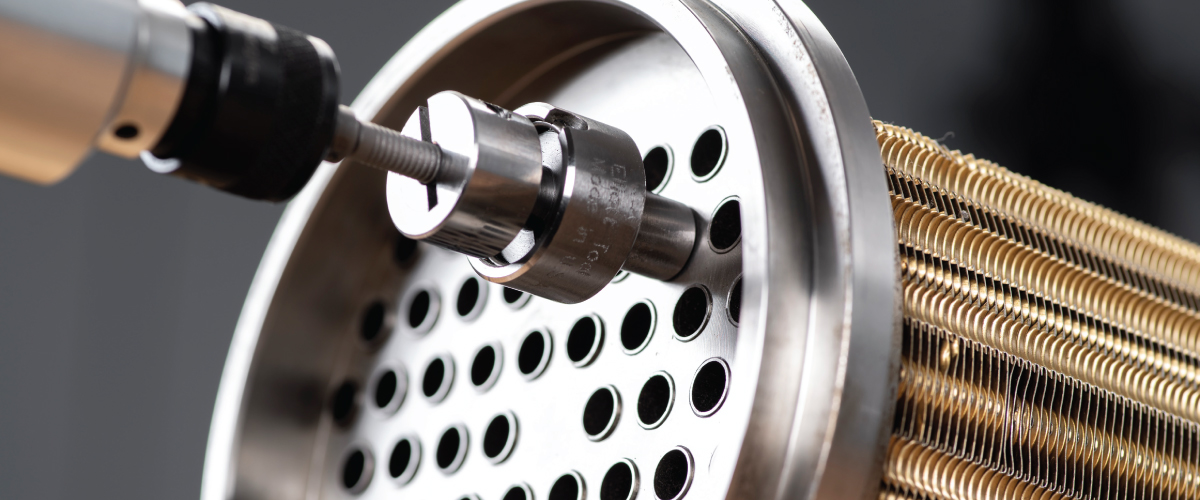
The goal when rolling a tube is to obtain a good mechanical tube-to-tube sheet joint. To ensure high-quality tube expansions, the tube wall must be reduced by a predetermined percentage and be consistent with each expansion. In order to complete the job efficiently, it is important to achieve the maximum expander tool life in order to reduce cost and downtime.
One of the most effective ways to prolong tool life is through the use of an assisted tube rolling system. Equipped with features such as torque control, an expander holder, and auto-lubrication, these systems can significantly increase expander tool life. Torque control systems accurately measure torque in order to roll to the target wall reduction each time, thus eliminating the amount of rework needed on a vessel. Additionally, the articulated arm and expander holder securely supports the motor and expander to ensure proper tool alignment and eliminate premature breakage due to axial loads. Lastly, auto-lubrication systems may be available on certain assisted tube rolling systems, such as the Hybrid Series Rapid Hawk. This feature provides automatic expander lubrication in order to increase tool life and reduce downtime spent re-lubricating tooling.
However, in situations where you are not able to use an assisted tube rolling system, here are some tips to make sure you are achieving the maximum tool life for your expanders.
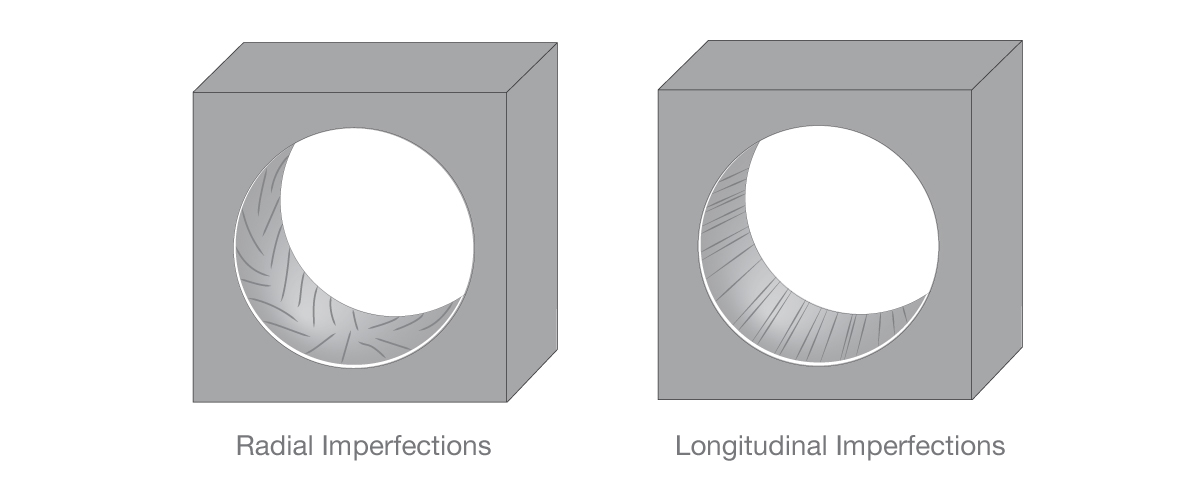
Visually Inspect The Tubes And Tube Sheet
The tube surfaces must be clean of debris, scratches, dents, and cracks in order to have a properly rolled tube. Utilizing a tube sheet hole brush aids in cleaning these surfaces. Inspect the tube sheet where the tube is being expanded into for any radial or longitudinal imperfections.
Use An Accurate Torque Control
In order to ensure an effective tube to tube-sheet joint, it is important to roll to the suggested tube wall reduction using an accurate torque control. This ensures repeatability of joint tightness and reduces overheating of the tube expander and components. Using this technique, in addition to an assisted tube rolling system, allows for consistent tube rolling, faster job completion times, and reduced re-rolling or re-working of tubes.
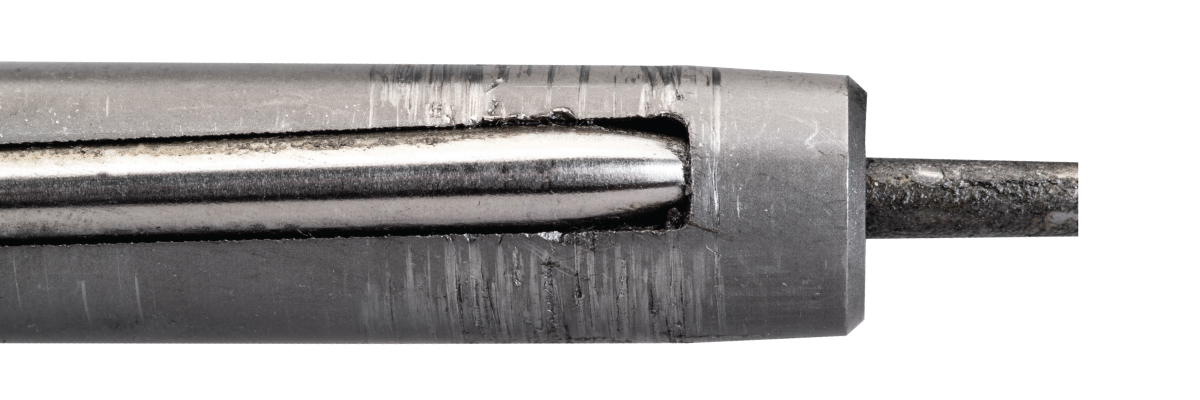
Expander Cage Wear
Ensure Expanders Stay Clean And Lubricated
Keep the expander clean and free from debris. If there are any visible signs of wear on the expander’s rolls and mandrel, replace these items immediately. The rolls and mandrel must be well lubricated to prolong tool life. There are two main types of lubricants: liquid lubricant and paste lubricant. The liquid lubricant is often used for stainless or titanium tubes because of its low sulfur content. Paste lubricant is commonly used for air coolers or in other applications where the operator is reaching through a header box, as it stays put and doesn’t drip into the vessel.
Use Two Expanders
One way to extend tool life is for each operator to use two expanders alternatively. When alternating tools, place one expander in lubricant while the other is used in the rolling operation. Change out the expanders after about 50 expansions to allow the tool to cool-off. A quick-change chuck can be used in order to minimize downtime. After about 5-7 exchanges, check to see if there is any debris trapped between the mandrel and rolls. If debris is present, disassemble and clean.
Use The Right Roll Sets For Your Application
Depending upon tube sheet thickness, the use of step rolling may be required. Best practices dictate that the first expansion should be set to achieve the deepest expansion into the tube sheet. This firmly sets the tube into the sheet and limits the tube movement from subsequent step rolls due to tube extrusion. The second expansion should slightly “overlap” the expanded area of the first rolling operation. As a result, double radius rolls should be used in order to allow a smooth transition between rolling steps. This step process should be continued until the full tube sheet thickness is rolled to the desired wall reduction.
Relief rolls are used when the tube ends are welded to the tube sheet. Due to the heat generated to form the welding bead, this material becomes hardened. If the expanding rolls contact this hardened steel area they will break, as this hardened material will not expand. The relief rolls are small in diameter in this critical area and will avoid contact with this hardened area, preventing premature failure.

Keep Thrust Bearings Well Lubricated
Thrust Bearings are used in expanders that have a guard or a collar that is positioned against the tube sheet, to keep the expander in a specific location. As the cage rotates, the thrust bearing absorbs the forward motion of the expander, allowing the collar to remain static in position against the tube sheet. Because of the force placed on the thrust bearing during expansion, it is important to keep it well lubricated to prolong tool life.
Select The Correct Collar For Your Application
When expanding, it is important that you are using the correct expander collar for your application. Most expanders come with a standard flush or recessed collar. However, in situations where you are rolling welded tubes or at an angle not perpendicular to the tube sheet, a swivel collar would be the best option. The swivel collar is able to bend against uneven surfaces while maintaining axial alignment of the expander within the tube.
Eliminate Premature Breakage Caused By Axial Loads
Hold the rolling motor in a vertical/straight position (perpendicular to the tube sheet) to avoid the motor weighing down sideways on the mandrel. If the motor is not held perpendicular to the tube sheet, it can cause fatigue and premature tool breakage due to axial load on the mandrel.
Overall, there are many factors that can influence the life of an expander. From improper tool lubrication to incorrect motor alignment, a lot can go wrong during expansion. One of the best methods to overcome these challenges is to use an assisted tube rolling system. With features such as torque control, an expander holder, and auto-lubrication, assisted tube rolling systems can solve many challenges that may arise during expansion. However, in cases where you will be rolling by hand, it is important to consider the above tips in order to get the best results.
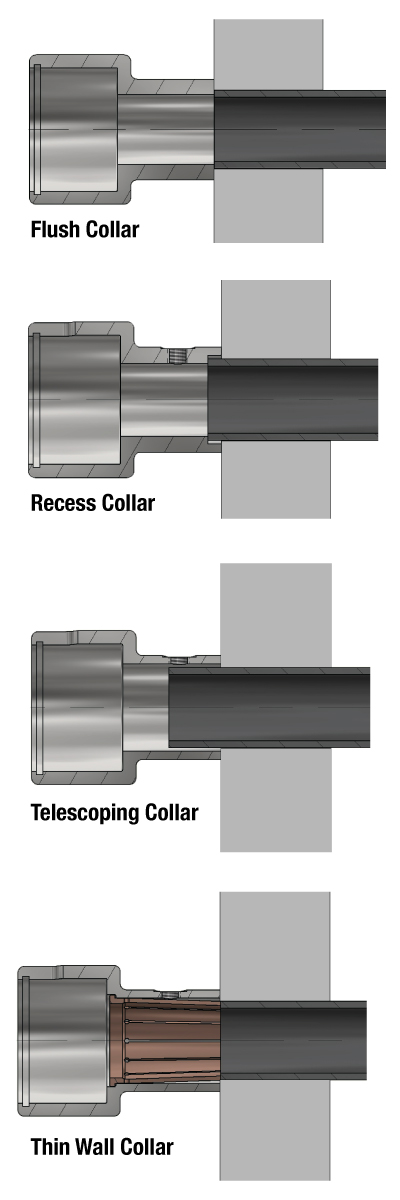