A Faster Way to Cut
Cutting lands in spool bore valves and valve bodies
Spool bore valves and valve bodies are common components in many heavy industries. From forklifts to land excavators, valves are used to regulate the flow of fluid through the machine, impacting the functionality of the machinery. For these large pieces of equipment to handle fine movements and adjustments, it’s important that the grooves and lands inside of the valve body are cut precisely. In the article, we will discuss spool bore valves and valve bodies: The design, how they work, as well as the processes for cutting grooves and lands.
What Are Spool Valves?
Spool valves are commonly used to control the flow of fluid or air in a piece of equipment. In heavy machinery, these are commonly used in excavators, forklifts, and other pieces construction equipment. Composed of a cylinder with an internal bore and a piston, actuating the valve causes the piston to move back and forth, opening and closing off different grooved pathways. The grooved areas of the bore consist of different configurations of hooks and bumps, also sometimes referred to as lands. These are small areas that have been notched out in the groove space, allowing for more precise fluid pathways.
As the valve is actuated, often with a lever or electronic controller, the piston moves to a specific position in the bore, allowing hydraulic fluid to fill the open space. This creates a change in pressure that is enough to allow for finite movements of the machine.
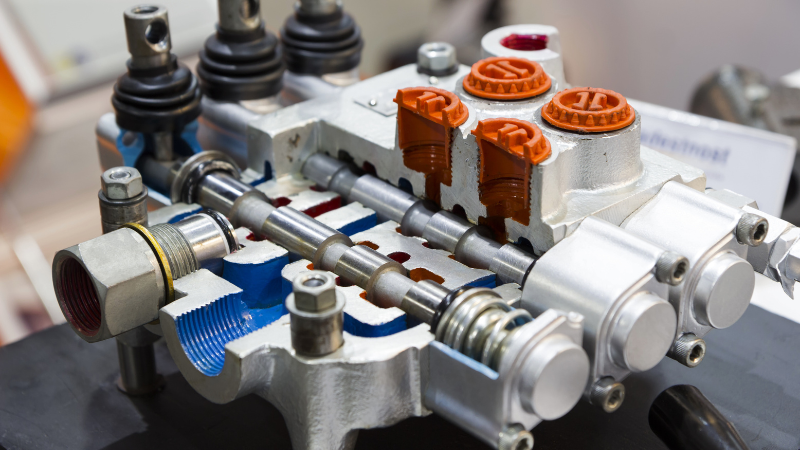
Figure 1. Hydraulic Spool Bore Valve
Source: Target Hydraulics, https://www.target-hydraulics.com/hydraulic-spool-valve
Cutting Grooves & Lands
Generally, the internal bore and grooves of a valve body are cast. This allows for easy and consistent production, and eliminates some challenges associated with grooving a finished part. Sometimes, the manufacturer will cast bore, but use a keyway cutter or boring bar to machine out the grooves and lands. While this method can work, it can take a lot longer to manufacture. This means that grooves need to be cut one at a time, followed by some type of system flush to remove any metal chips or debris.
Regardless of the manufacturing type, once the grooves and bore are complete, the lands will still need to be machined out during a separate process. This is because castings are unable to hold the tight tolerances needed to produce the lands and the locations can vary based on the valve body.
Boring Bar
One traditional method for machining lands is with the use of a boring bar. This consists of a holder, a long bar, and a cutting edge on the end. Generally, boring bars are run on a lathe, so the part is spinning while the tool remains stationary.
While boring bars can work well for cutting lands, it’s generally a lot more time consuming and it can produce some inconsistent results. Due to the design of the tool, only one groove can be cut at a time. Additionally, due to the thin nature of the tool, the difference in diameter of the boring bar and the bore diameter poses the risk of deflection. This is when the tool bends and becomes out of alignment when in use. If this occurs, it can result in improper sized lands, cutting in the wrong location, and chatter or vibration, causing poor surface finish.
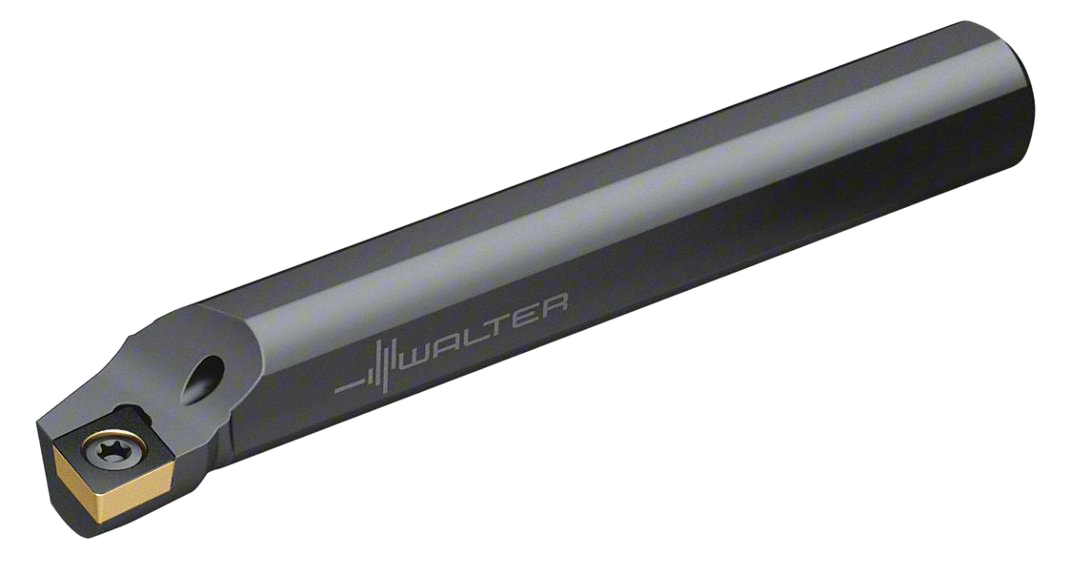
Figure 2. Boring Bar
Source: Target Hydraulics, https://www.grainger.com/product/WALTER-VALENITE-Indexable-Boring-Bar-80-Diamond-30EM81
Internal Recessing Cutters (IRUs)
One of the most popular and efficient methods for cutting lands is with the use of an Internal Recessing Cutter (IRU). Made up of a pilot, nose piece, and cutter, this tool is an all-in-one solution for cutting valve bodies. Each tool is designed to the specific bore diameter and application requirements of the valve, allowing the tool to sit correctly inside of the part. Proper sizing leaves little room for deflection, allowing for more precise cuts and a better surface finish. Deflection is controlled by allowing the cutting teeth to recess into the pilot as a function of this tool. The cutter is activated once pressure is applied to the operating head and the nose piece engages the part.
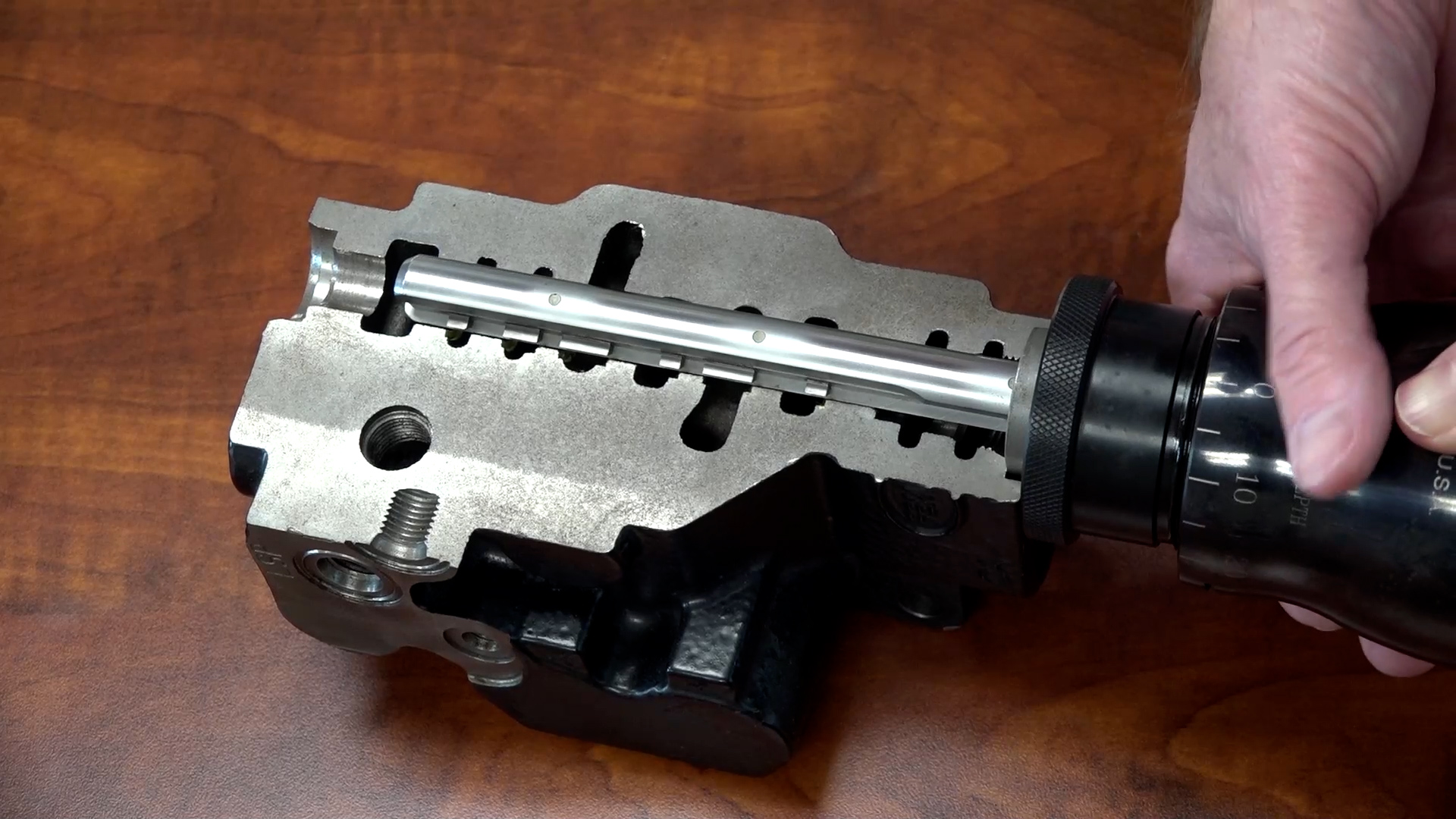
Figure 3. IRU in Valve Body Grooves
In addition to being sized to the application, IRUs also allow all grooves to be cut at the same time. This makes it a much faster process than cutting each groove one at a time. IRUs are also a great method for cutting when working with unusual geometries. Since each tool is custom, the cutting teeth can be manufactured to suit a variety of different part requirements. Some lands require different shapes or angles of cuts, which can be easily achieved with an IRU style cutter. The cutter can often be re-sharpened to allow for several more cycles to be gained out of the same tool vs. buying a brand-new cutter.
Overall, spool bore valves and valve bodies are a key component in heavy machining applications, as they help regulate movement in large pieces of equipment. Precise machining of the bore, grooves, and lands is critical in order to achieve control over fine movements or adjustments. While there are many different methods for cutting grooves and lands, one of the most efficient methods is an internal recessing cutter or IRU. With the ability to cut all grooves at once and being customized to a particular application, IRU cutters save a significant amount of job time, making it easier to take on high volume parts.
For more information about IRU cutters or other metal finishing applications, please contact our Customer Experience Team: sales@elliott-tool.com.