The Power of Burnishing in Aerospace
Burnishing, a cold working process, offers a multitude of benefits for the aerospace industry. By improving surface finish, increasing hardness, and introducing compressive residual stresses, burnishing enhances the performance and durability of critical components. This article delves into the specific applications of burnishing in engine components, landing gear, bearing surfaces, and fuel systems.
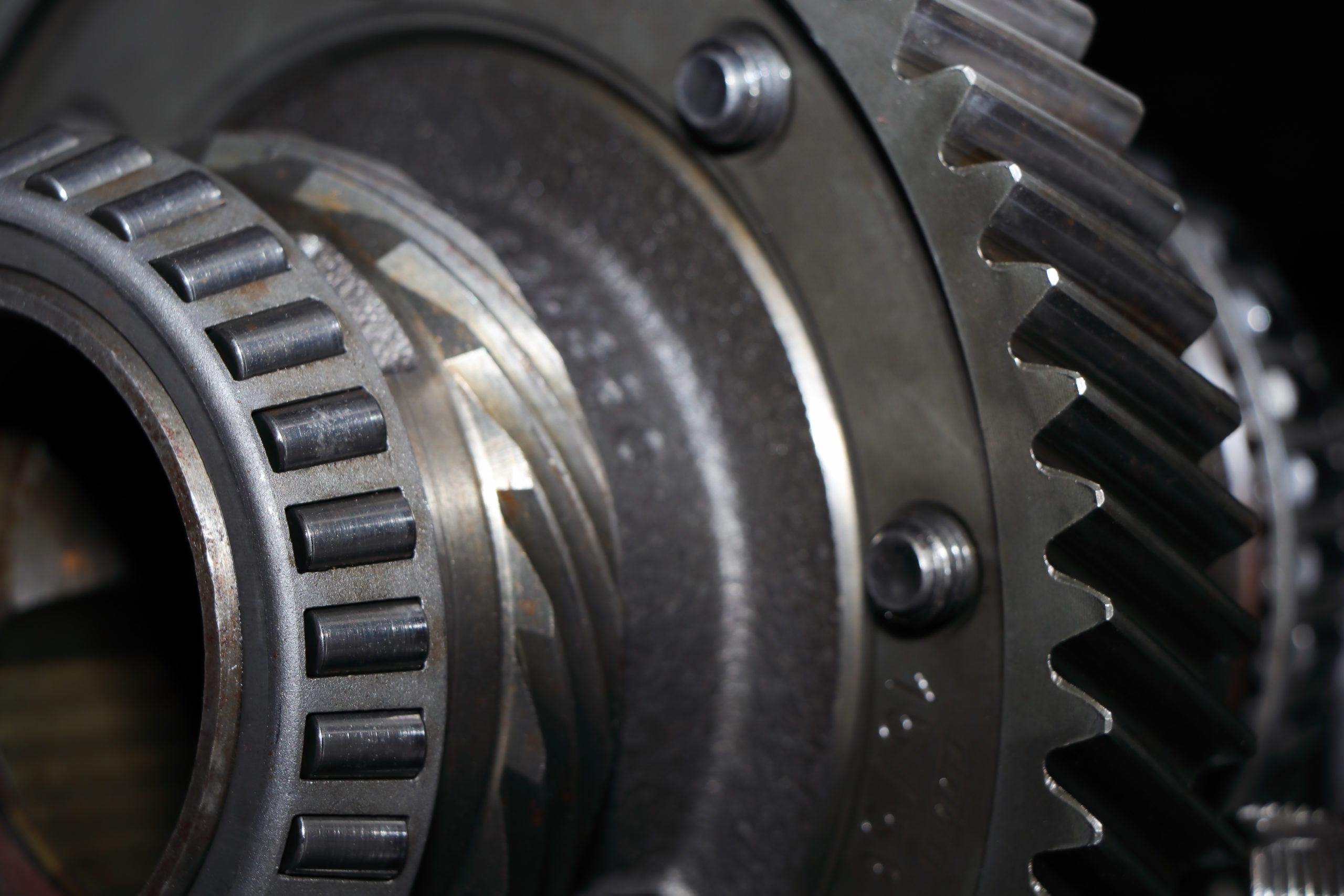
Engine Components & Landing Gear
One benefit of burnishing is that it can improve the fatigue life of critical components like turbine blades, compressor disks, and shafts, which are subjected to cyclic stresses.
Burnishing is a machining process that cold works the metal, rearranging a metal’s crystal structure to increase surface hardness. This higher hardness provides an increases resistance to abrasion and wear. This can be especially important in critical components, as it helps prolong the life of the part.
Additionally, burnishing introduces compressive residual stress to the material that can counteract forces placed on high-stress areas like blade roots and disk rims. This is done to help pre-stress the material to avoid fractures or failure in flight.
Landing gear struts also benefit from the increased surface hardness and introducing compressive residual stress, as this can delay crack initiation and propagation in use.
Bearing Surfaces
Bearings are an essential component that support rotating shafts and reduce friction. Burnishing can improve the performance and durability of bearings by reducing friction and improving fatigue resistance. The smoother the surface the bearing rides on, the less friction that will be produced between components. Additionally, a harder surface can enhance the bearing’s ability to withstand cyclic loads, prolonging the bearings lifespan.
Specific Applications:
- Engine Bearings – Improved wear resistance and reduced friction of main and accessory engine bearings can extend their lifespan
- Landing Gear Bearings – Enhanced wear resistance of wheel bearings and strut bearings will improve performance and durability
- Hydraulic System Components – Improved wear resistance of hydraulic pump and valve components reduces leakage and extends service lifespan
Hydraulics & Fuel Systems
Burnishing can significantly reduce surface roughness in hydraulic components such as valves, pumps, and fittings. This smoother surface reduces friction, leading to improved fluid flow and reduced pressure drops.
Like hydraulic systems, burnishing can improve fuel flow in fuel tanks, lines, and pumps. Additionally, the smoother the surface, the less susceptible it is to corrosion, which can be a significant issue in fuel systems due to the presence of corrosive additives.
Specific Applications:
- Hydraulic Cylinders – improved surface finish enhances sealing performance and reduces friction
- Fuel Injectors – improved surface finish of fuel injector nozzles improves fuel atomization and combustion efficiency
- Fuel Tanks – Reduced surface roughness prevents accumulation of contaminants and improves fuel quality
- Fuel Pumps – Reduced friction and wear improves the efficiency and durability of fuel pumps
Burnishing emerges as a powerful tool for enhancing the performance and reliability of aerospace components. By improving surface finish, increasing hardness, and introducing compressive residual stresses, burnishing significantly extends the lifespan and reduces maintenance costs. As the aerospace industry continues to push the boundaries of technology, burnishing will remain a valuable technique for optimizing component performance and ensuring the safety and efficiency of aircraft.