Understanding Expander Design & Functionality
Tube expanding is a technique used to create a secure connection between a tube and tube sheet, by compressing the outer diameter against a fixed surface. This process ensures a leak-proof joint that is crucial for the proper functioning of heat exchangers and other pressure vessels.
Anatomy of a Tube Expander
While specific designs vary, core components typically include a cage, mandrel, rolls, and collar.
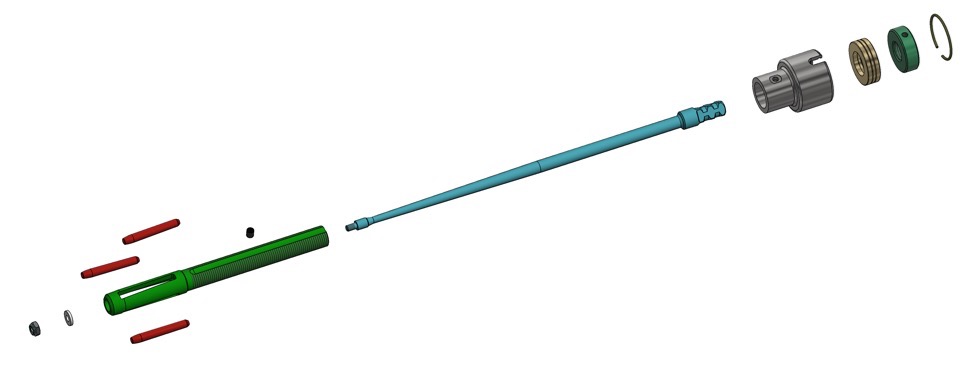
Cage
This acts as a housing for the mandrel, roll set, and collar, holding it in place. It features slots for the rolls and a threaded section for collar adjustment.
Mandrel
The mandrel goes through the case and is used to actuate expansion. When pushed forward, its taper pushes the rolls outward, engaging with the tube.
Rolls
Typically in sets of 3-5, the rolls make contact with the tube’s ID, forcing it to expand against the tube sheet hole.
Collar
Adjusted to accommodate different tube sheet thicknesses, the collar positions the rolls accurately within the expansion area of the tube sheet.
The Tube Expansion Process
The goal of expansion is a secure, leak-free tube-to-tube sheet joint. During expansion, the mandrel is fed into the tube and rotated. This action forces the rolls outward, expanding the tube until it contacts the tube sheet hole.
This expansion process can induce stress in both the tube and the tube sheet hole. As the rolls pass over the tube, the metal may resist the force and attempt to return to its original shape. This repeated stress leads to work hardening, making the metal less malleable.
Metals like titanium, stainless steel, or Inconel work harden very quickly due to their elasticity. Elasticity allows a material to stretch and return to its original shape. However, when the applied force exceeds the material’s elastic limit, permanent deformation occurs. During expansion, the tube and tube sheet expand until the tube reaches its plastic state and is contained by the tube sheet’s elastic properties.
Selecting the Right Expander
While similar, boiler and heat exchanger expanders do have some significant differences in size and function.
Boiler Expanders
These are 3 main types of boiler expanders: Flaring, straight roll, and roll beading.
Flaring and beading prevent tube ends from overheating and cracking. Watertube boilers require tubes to be flared and then straight rolled, while fire tube boilers will flare the exit side and bead the fire side.
Key Considerations:
- Tube OD
- Wall thickness
- Tube sheet thickness
- Space constraints
- Distance to the tube bend (generally for watertube boilers)
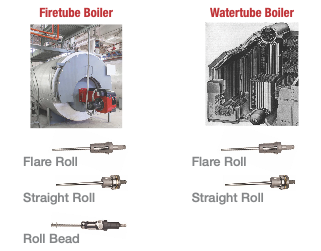
Heat Exchanger & Condenser Expanders
Due to industry practices and manufacturing requirements, heat exchanger expander design allows for easy customization.
Key considerations:
- Tube OD
- Wall thickness
- Minimum/average wall tube
- Tube sheet thickness
- Reach requirements
- Welded tubes
- Required projection
- Handheld or assisted rolling system
Summary
Proper tube expansion is critical for vessel performance, By understanding the anatomy of an expander and following best practices for selection and use, operators can ensure secure and reliable tube-to-tube sheet joints.
Read more about proper tool selection and installation procedures in our expansion series.