Why Won’t This Tube Expand?
Troubleshooting Incomplete Tube Expansion in Heat Exchangers
When expanding heat exchanger tubes, achieving the proper wall reduction is crucial for a secure and leak-free seal. Sometimes, however, tubes fail to expand sufficiently, hindering the integrity of the vessel. This article outlines common causes and troubleshooting steps for incomplete tube expansion.
Initial Questions to Ask
Before diving into complex diagnostics, start with these fundamental questions:
1. Motor Sizing
Is the motor powerful enough for the job? Insufficient torque can prevent proper expansion. This depends on several factors including: tube outer diameter (OD), wall thickness, tube material, tubesheet thickness, and tubesheet material. A motor that lacks the necessary torque will struggle to expand the tube effectively.
2. Expander Selection
Are you using the correct expander? Choosing the right tool is critical for expansion. Reviewing the tube OD, wall thickness, and whether the tubing is minimum or average wall will reveal if the right sized tool is being used. For example, in minimum wall application, a smaller expander size is needed to fit the tube ID. Additionally, if the tubes have inconsistent inner diameters (ID) due to supplier variations, it can mean that 2 expanders are required for the job. This is generally indicated when a very small wall reduction (2-3%) is achieved despite attempts to expand further.
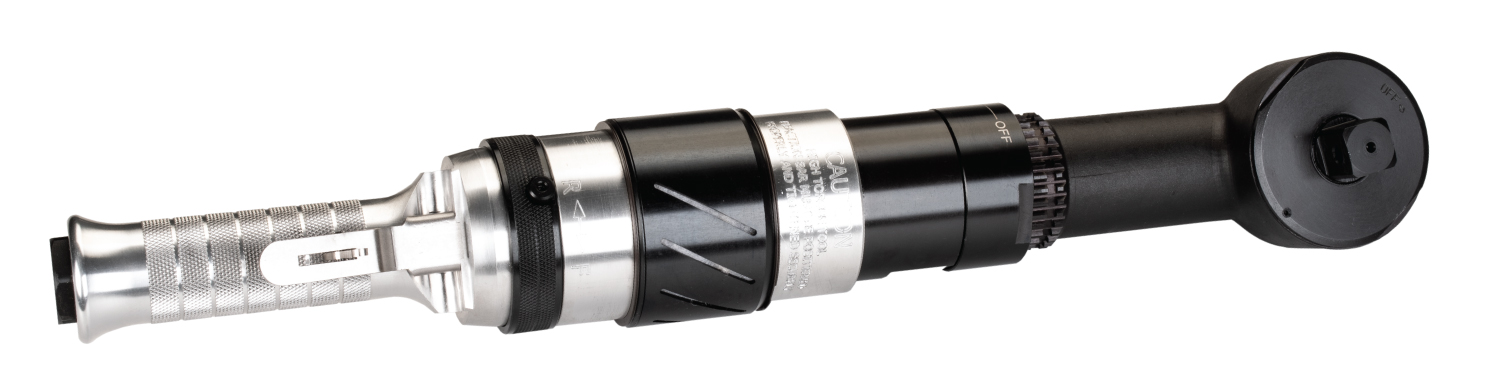
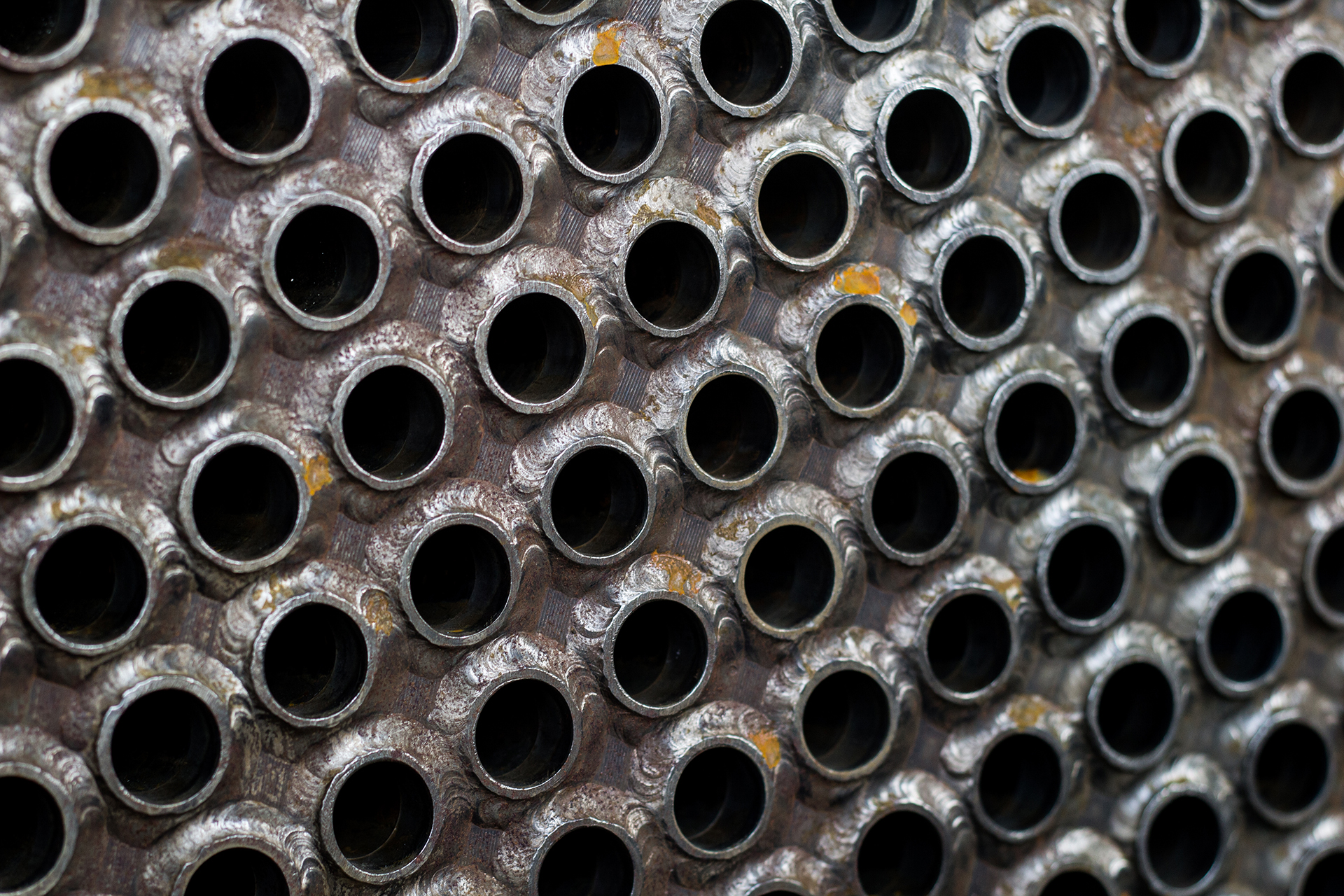
3. Welded Tubes
Are the tubes seal welded? If the right motor and expander are selected, welds are generally the most common cause. If using standard rolls on seal-welded tubes, the tool might be working against the weld itself, not the tube ID. Relief rolls are essential in these scenarios to avoid contact with the welded area.
4. Thick Tubesheets
Are you expanding welded tubes in a thicker tubesheet (>2.125”)? Welding can induce a heat treat effect in the tube ends, especially in thicker tubesheets. Excessive heat during welding can work harden the first 3/16” to ¼” of the tube, making it resistant to expansion. Test for this by adjusting the roll into the tube by the effective roll length. If expansion is successful in this adjusted position, heat treat is the likely cause.
Advanced Troubleshooting
If the initial questions don’t reveal the problem, a more in-depth investigation is necessary. Consider the following:
- Material Compatibility: Analyze the tubesheet material, tube pitch, and tube material for compatibility.
- Expander Design: Evaluate the expander design for suitability to the specific application.
- Motor Performance: Verify the motor’s performance. For air-powered motors, ensure consistent air supply. For electric motors, confirm stable voltage.
- Work Hardening: Have you expanded the tube area multiple times? Repeated expansion, especially with materials like Inconel into Hastelloy at high torque (e.g., 60 ft-lbs), can lead to work hardening, preventing further expansion.
Rare but Possible Issues:
- Extreme Wall Thickness: If the tube wall thickness is excessively high (e.g., ≥ 20% of the tube OD, like ½” x .100 wall), expansion might be impossible. The required expander would be too small to achieve sufficient expansion range. In such cases, welding is the only viable option.
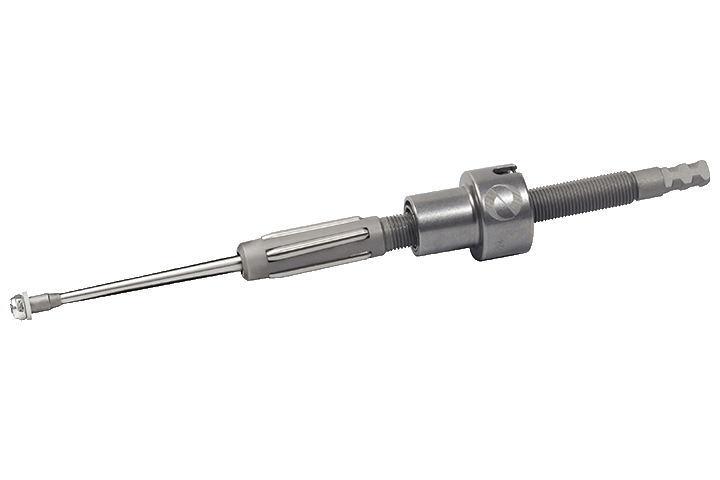
Conclusion
Most often, the inability to expand a tube to the proper wall reduction stems from issues with welded tubes or work hardening. By systematically addressing the questions and troubleshooting steps outlined above, you can pinpoint the cause and implement the appropriate solution. Thorough understanding of the application, materials, and tooling is crucial for successful tube expansion and a reliable heat exchanger.