Many operators are challenged with completing a job correctly and on time. There are many factors that can influence a job outcome, such as tool life, operator error, and system productivity. One of the most effective ways to overcome these issues is through the use of an assisted tube rolling system.
Each system comes equipped with different features to suit your needs such as torque control, an expander holder, and auto-lubrication. Torque control systems accurately measure torque in order to roll to the target wall reduction each time, thus eliminating the amount of rework needed on a vessel. Additionally, an articulated arm and expander holder securely support the motor and expander to ensure proper tool alignment and eliminate premature breakage due to axial loads. Lastly, auto-lubrication provides automatic expander lubrication in order to increase tool life and reduce downtime spent re-lubricating tooling.
When purchasing a system, there are several factors you should look at to determine the correct solution, such as tube size, consistency, productivity, and ergonomics.
Tube Size
When choosing a system, it is important to first look at tube size. While most systems cover a wide range of sizes, some are specifically designed for rolling smaller tubes, like those found in oil coolers and small heat exchangers. These smaller systems also work well in smaller workspaces.
Consistency
After considering the size of the vessel, you can start to look at the consistency of the system. The goal when rolling a tube is to obtain a good mechanical tube-to-tube sheet joint. To ensure high quality-tube expansions, the tube wall must be reduced by a predetermined percentage and be consistent with each expansion. Maintaining rolling consistency will reduce the chances for tube leaks and rework later on.
Assisted tube rolling systems will be significantly more consistent than rolling by hand due to a built-in torque control system. While pneumatic motors are faster than electric, they tend to have challenges with consistency due to fluctuations in air volume or pressure. To overcome this, some systems will utilize an electronic torque control that can work with a motor regardless of its power source.
Productivity
Another aspect to consider when choosing a system is productivity. In general, the use of an assisted tube rolling system can significantly prolong tool life and boost productivity. First, an expander holder securely supports the expander to ensure proper tool alignment and eliminate premature breakage due to axial loads. Additionally, automatic tool lubrication provides lubrication to the working area of the tool, helping to expander tool life. This is especially helpful in vessels with thick tube sheets or water boxes.
Aside from tool life, the speed of the system is also important when determining productivity. Considering cycle time, tooling change-out, and lost time due to rework, an electric system would be a good option, a pneumatic or hybrid system would be a better option, and a hydraulic system would be the best option. Hydraulic rolling systems often utilize parallel pin expansion. In traditional expansion, the rotation of the mandrel combined with the feed angle determines how quickly a tube can be expanded. Once the expansion is complete, the mandrel rotation must be reversed to remove the expander from the tube. Parallel pin expanders are constantly rotated in one direction while the mandrel is pushed and pulled from the tube, independent to its rotational speed. As a result, cycle times can be reduced by 50% or more compared to traditional expansion.
Ergonomics
Each system is equipped with features to reduce fatigue and stress when rolling. A counterbalance type system will reduce the weight of the motor for the operator when rolling. However, most counterbalance systems do not absorb the torque of the motor, causing the operator to take on that force. On the other hand, an articulated arm will support the weight and absorb the torque of the rolling motor, allowing the operator to effortlessly roll and move the motor into position.
Ease of use is also important when choosing a system. One way this is achieved is through an auto-reverse system. These motors will roll until they hit torque and automatically reverse out of the tube, making the expansion process easier for the operator. Further, some systems are equipped with auto-cycling. This allows the operator to simply turn the system on and it will start, stop, and reverse without any operator intervention.
Overall, assisted tube rolling systems are a great way to increase productivity and decrease cost. When choosing a system it is important to consider tube size, consistency, productivity, and ergonomics. These will help you choose the system that is right for your facility.
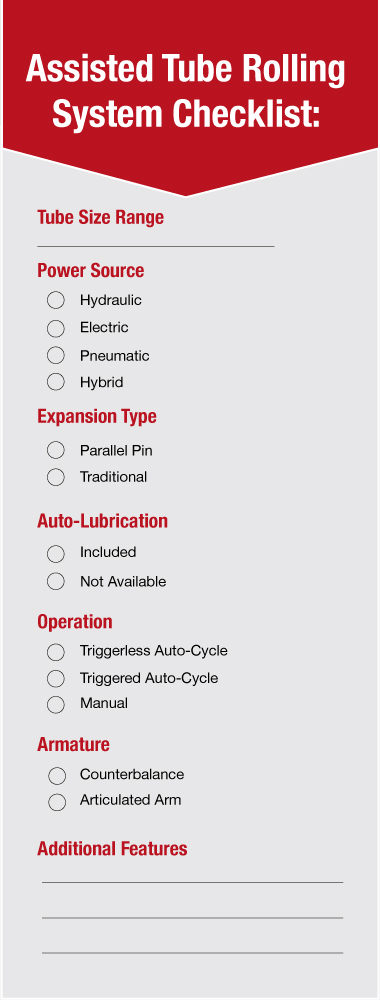