A Perfect Finish
How Time, Pressure, & Pre-Finish Impact Surface Finish
Burnishing is a quick and effective method for achieving a smooth surface finish when set-up properly. While there are many variables that can impact the surface finish of a part, there are 3 key variables that can be leveraged to change the outcome. Time, pressure, and pre-finish play a critical role in the ultimate outcome of the part. Changing any one of these variables could result in dramatically different results, which is why it’s important to understand what they are and how they work together to achieve the desired surface finish
Time & Feed Rate
Feedrate is the speed at which a tool moves across a workpiece, in this case the time it takes to burnish a part. In general, a slower feed will yield a better finish, but it may not be optimal given the workpiece material. If a feedrate is too low it can cause excessive plastic deformation and an over-compression of the surface. This leads to work hardening and can potentially damage the surface of the part. Additionally, a very slow feedrate coupled with a low pressure won’t be able to compress the part material, essentially providing very little finishing to the part.
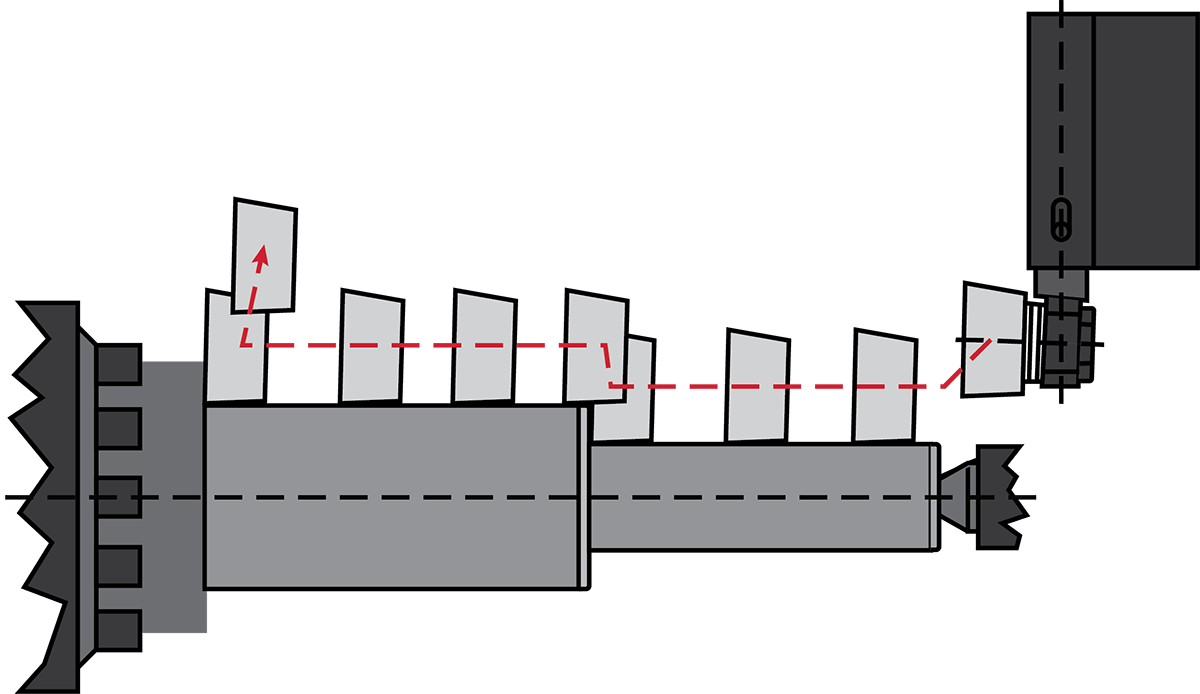
On the opposite end of the spectrum, if the feedrate is too high, the tool may not spend enough time on the surface to achieve plastic deformation. This can result in a rougher surface finish and leave visible tool marks on the surface. To get the best performance out of the tool, it’s important to find the optimal feedrate that allows the tool to deform the surface enough that it creates a smoother and more polished finish. The best feedrate ensures the tool maintains consistent contact with the surface, providing uniform compression and material flow. Depending on the tool itself, a minimum feedrate may be required to produce consistent results.
Pressure
Like feedrate, the amount of pressure that is applied to the part will determine the amount of plastic deformation and the smoothness of the surface. The pressure of the workpiece can be adjusted a few different ways such as, preloading the pressure on the tool itself or adjusting the gap between the tool and the stock allowance of the part. The method for adjustment will largely depend on the type of tool being used and the part being burnished.
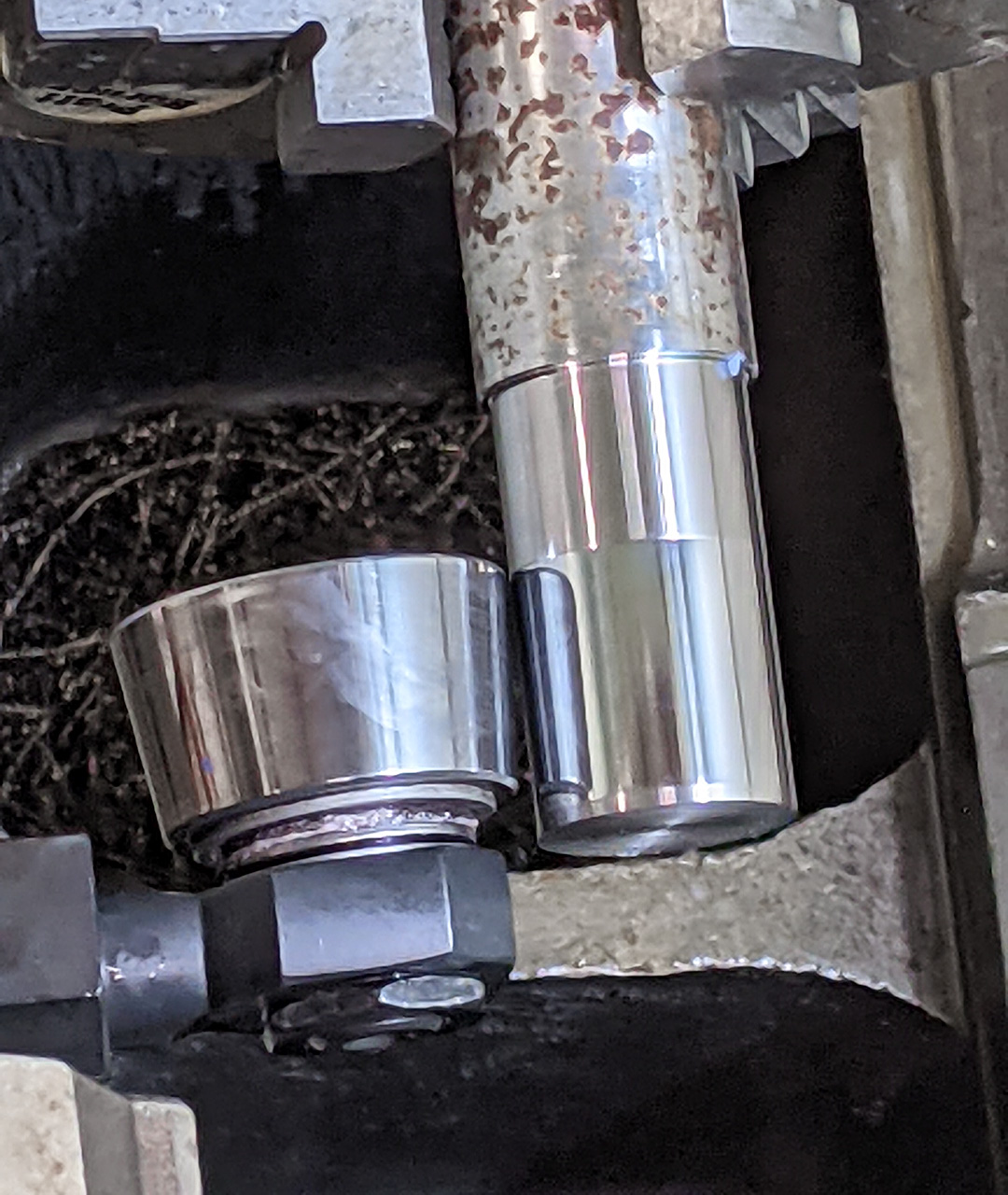
Generally, lower pressure will result in less compression, while higher pressure will result in more. However, like feedrate, the extremes of both can cause problems. Lower pressures may be insufficient in deforming the material, leaving surface irregularities, or producing a rougher finish. Excessive pressure can cause too much compression, leading to surface damage, work hardening and increased tool wear. As a result, an optimal pressure ensures that there is effective plastic deformation, meaning the tool compresses the surface material properly, reducing peaks and valleys to create a uniform appearance.
Pre-Finish or Starting Finish
The initial condition of the part surface, or pre-finish, is significant in determining the final burnished finish. A coarse finish with a peak and valley pattern is preferred for materials with a high ductility, while a smoother pre-finish is better for harder materials (45+ HRC). This is because highly ductile materials are better able to compress and change shape, while harder materials are more difficult to move and are more prone to work hardening. While the part material will determine where the pre-finish needs to lean, there are some general principles for varying levels of pre-finish.
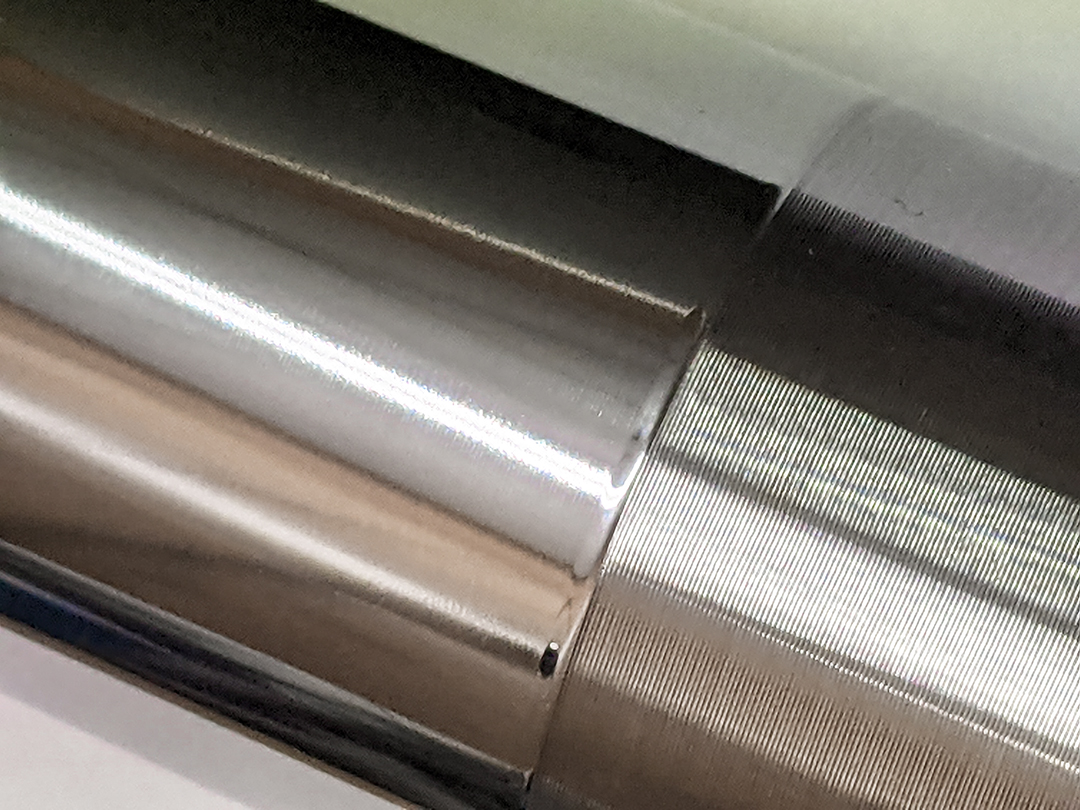
Rough pre-finish with significant irregularities is generally not ideal for burnishing. This is because it can increase the pressure required to compress the material which can damage or distort the part surface. Additionally, there is a higher probability that the irregularities in the starting finish will be visible in the burnished finish. One step down is a coarse pre-finish, 60-120 Ra, which has a consistent peak and valley pattern with minimal defects. This is an optimal starting finish for ductile materials, as it allows for better compression and produces a smoother final finish. Last is a smooth pre-finish, < 40 Ra, which greatly reduces the required burnishing time and pressure. As mentioned, a smoother pre-finish is ideal for harder materials as it allows for efficient material flow and results in a better polished surface after burnishing.
For more information on finishes, contact our application support team.