Tube Removal Triumph
Avoiding Common Pitfalls of Tube Extraction
Tube removal can be a daunting task, especially when encountering challenges like corrosion or tight spaces. One of the most frustrating situations operators face is the inability to pull a tube using a hydraulic puller. This article explores the four primary reasons behind this issue and offers simple solutions to overcome them.
Why Won’t This Tube Pull?
- Tube isn’t cut on the other side
- Seal or strength weld has not been removed
- Wrong size or worn-out tooling
- Extreme corrosion
Tube Isn’t Cut
A common oversight in tube removal is failing to cut the tube on the opposite side behind the tube sheet. This is particularly easy to miss when removing multiple tubes or sections. To prevent delays due to missed tubes, it’s recommended to check that all tubes in the removal area have been successfully cut through on the other side prior to pulling.
Weld Hasn’t Been Removed
With many manufacturers opting for seal or strength welds, welded tubes have become extremely common. While they are beneficial for the vessel when in operation, they can make tube removal much more time consuming. In order to remove a welded tube, the weld must first be removed.
One of the best methods for weld removal is to use an end prep tool, also known as a tube auger, boiler gun, or mill hog. This tool uses a collet jaw to grip the inside of the tube while the operator advances the blade until the weld is fully removed.
Wrong Size Or Worn-Out Tool
When using a pulling spear, the ID of the tube is critical. If the spear is undersized for the tube, you will see it bottom out when being driven into the tube. This means it will go in the tube a quarter or halfway (up to the shoulder) before being driven in with an impact. If a spear is too small, the teeth won’t be able to bite into the tube material enough to break the mechanical joint.
If the spear is oversized it will be difficult to drive it into the tube. This means that it will require more force to drive it into the tube with an impact and it won’t be able to grip the tube effectively. Instead, this will result in spear breakage where the very end will snap off in use.
In addition to improper spear sizing, the inability to remove the tube can also be related to worn-out tooling. This can mean that the teeth of the spear are worn down and have lost their ability to grip the material. It can also mean that the collets are worn out and are not grabbing the spear or tube in the hydraulic puller itself. Many customers will know the collet set is worn out when they feel they need additional leverage to pull the tube.
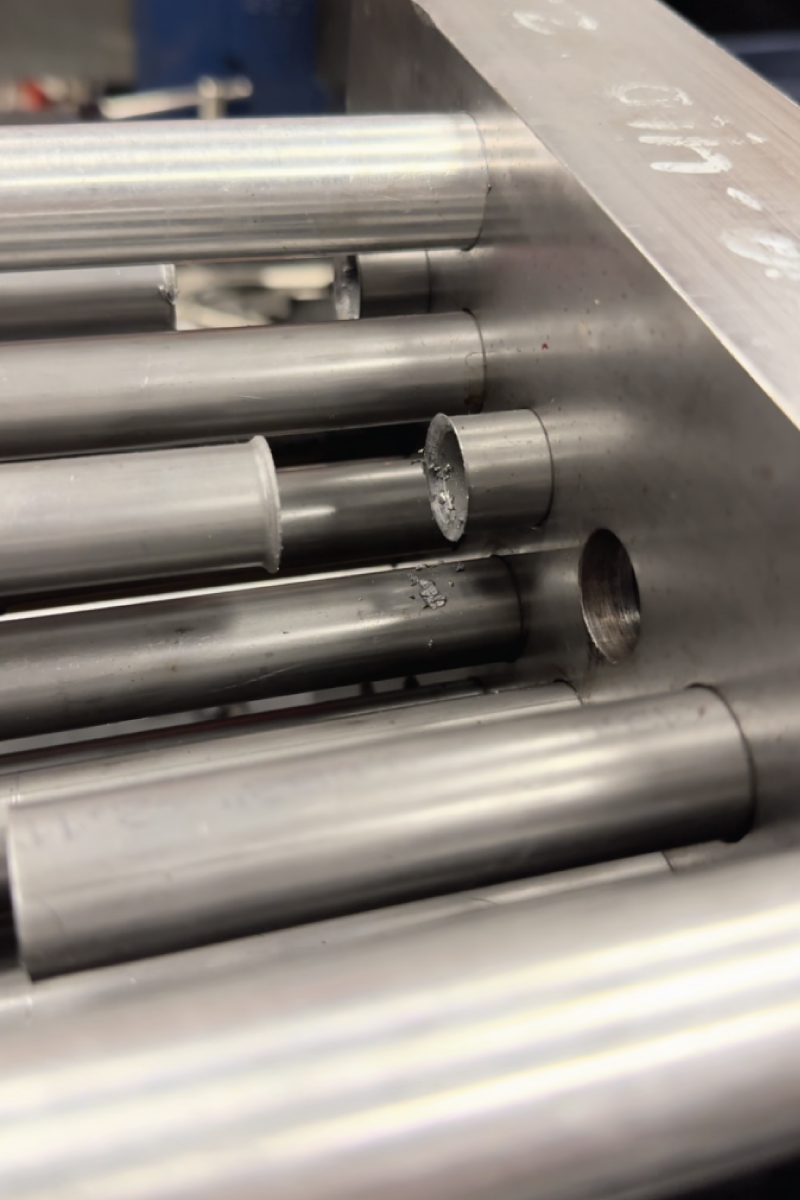
Too Much Corrosion
In certain petrochemical applications, the hot pass side of an exchanger can see extensive corrosion due to temperature and caustic materials. If the tube is too worn and brittle, it will be very challenging to remove the tube with a spear. This will be evident if the tube breaks or fractures into pieces when trying to pull. In these situations, it’s preferred to pull the tube from the back or punch them out with a knockout tool.
By understanding and addressing the common tube removal challenges outlined in this article, operators can significantly improve efficiency and reduce downtime. Proper tool selection and adherence to best practices are essential for successful tube extraction. By investing in training and staying updated on the latest techniques, operators can ensure that tube removal remains a smooth and efficient process.
By carefully considering these factors, you can select the most appropriate tube cleaning method to effectively remove deposits and maintain vessel performance. For more information on selecting the right cleaning tool, contact our Application Specialist Team.