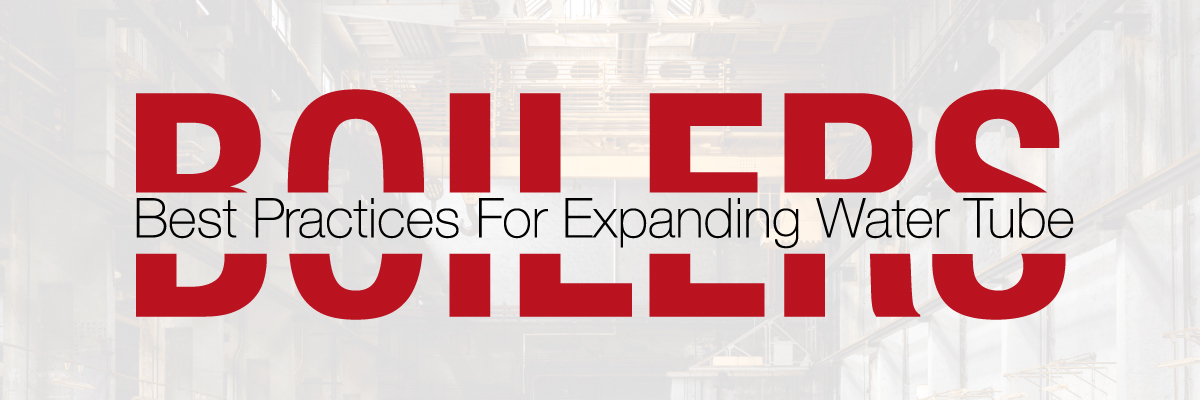
The American Society Of Mechanical Engineers (ASME) develops standards to provide consistency and ensure public safety and reliability. While these codes are not always required, they have been widely adopted and implemented across many industries. As a result, it is important to be knowledgeable and aware of these standards prior to beginning a job.
There are a number of important steps, which should be considered before the actual tube rolling is to take place. The sequence of rolling tubes into drums and water wall headers is as important as rolling the tube joints themselves. When rolling a tube joint, there is an elongation of the tube; the tube actually grows by a fraction of an inch. This growth causes pressure between tube sheets. When rolling water wall tubes, this will cause the tubes to push the upper or lower headers out of alignment. Therefore, it’s recommended that the sequence of rolling be obtained from the manufacturer of the boiler prior to rolling.
Determine Proper Tooling
Before Starting A Job
- What is the OD and BWG (or wall thickness) of the tube?
- What is the tube sheet thickness, drum thickness, or length of the tube?
- Do the tubes have a bend outside of the drum?
- What type of mandrel is needed?
Types Of Mandrels
- Drum Mandrel- For drums that are 18″ in diameter or larger.
- Short Mandrel- A set of short mandrels are used in curved boiler tubes to prevent the mandrel from damaging the tube.
- Header Mandrel- For extended reach if the tube is in direct line with the hand hole.
Generally, drums are thicker than the headers, so it’s important to select different expanders with the proper roll lengths for both headers and drums. Boiler expanders are designed with rolls sufficiently long to roll 1/4” to 3/8” beyond the sheet thickness. Boiler inspectors insist that tubes be rolled the full thickness plus a minimum of 3/16” beyond the sheet or drum thickness to a maximum 1/2”.
It’s very common to use four or five different tools when repairing watertube boilers. As a result, it is important to bring a variety of operating accessories, such as universal joints for rolling headers.
Short Mandrels
Step Rolling Process
The ASME boiler code states the projection of tube ends into boiler drums and headers shall not be less than 1/4” and not more than 1/2”. These are measured on the high side of the drum shell and before the tube end is flared. The code further specifies that the flare of the tube end must not be less than 1/8” greater than the diameter of the tube hole. It is important not to exceed these specifications, in order to prevent splitting.
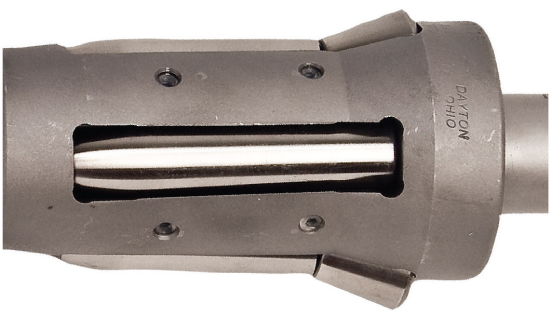
Flare Roll Boiler Expander
Flaring The Tube End
When flaring tube ends it is extremely important that the flare roll does not travel into the drum. Otherwise, it will create a sharp edge on the ID of the tube and a surface crack on the OD of the tube. Choose the appropriate expander; tube hole tolerances should be considered (figure plus 1/32”), the roll length should allow you to expand a minimum of 3/16” to a maximum of 1/2” beyond the tube sheet or seat, as in a drum or counter-bored tube hole. Using a flare roll tube expander, roll and flare the tube end in one pass, approximately three-fourths tight. Roll a suitable flare to meet the ASME specifications. When setting the tube expander in the tube, it’s important to determine how far into the tube the expanding portion of the rolls should be set. Set the rolls and tighten the mandrel so that the space between the end of the tube and the front of the flare roll will allow for rolling the tube three-fourths tight while producing a suitable flare. No rigid instruction can be prepared for this step since the rolling of boiler tubes is best performed through the experience and judgment of the operator. If a condition exists where the tube hole tolerance is extremely large, it may be necessary to set the tube with the straight roll expander, flare the end with a flare roll expander, and then re-roll with the straight roll expander.
Expanding The Tube
To complete the tube rolling cycle and form a leak-proof joint, use a straight roll expander to re-roll each tube end. This will also smooth out any out-of-round holes in your tube sheet or any tube with uneven wall thickness. There are manufacturers who feel that rolling the tube with a flare roll expander only is the best procedure. They will take a flare roll expander and roll and flare the tubes to a tight tube joint. If the flaring roll starts to walk under the drum, they back the tool out and place the mandrel in the expander tightly and finish the roll. While this may work, it is not recommended.
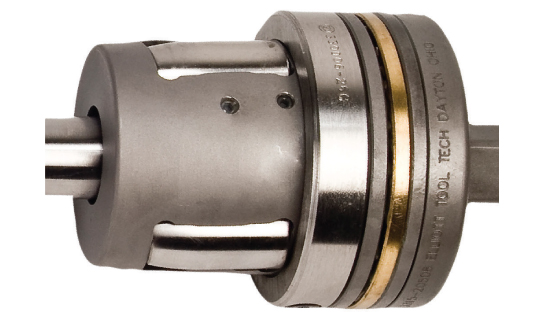
Straight Roll Boiler Expander