
With a wide variety of rolling motors on the market, choosing the right one can seem overwhelming. There are several factors to consider when selecting a rolling motor. Power source, torque control, RPM, torque range, and the style of the motor will vary depending on the application.
Electric v Pneumatic Motors
When expanding tubes mechanically, both electric and pneumatic rolling motors can be used. The power source can be determined by operator preference, availability of electricity or air, and the application.
Electricity offers better consistency when expanding tubes and is more readily available than air. Since there is less variation, electric is the best option when a very specific ID or wall reduction needs to be reached.
Pneumatic motors offer faster speeds and more power; however, they can be more susceptible to fluctuations in air supply. These motors are generally preferred in tough boiler applications because of the higher torque required to move a large amount of material.

Electric Rolling Motor

Pneumatic Rolling Motor
Types Of Torque Control
Torque controlled tube expanding is the most popular method for tube expansion because it compensates for variables that the operator cannot control, such as variances in the tube sheet hole ID and tube wall thickness tolerances.
Electronic Torque Control
When using an electric rolling motor, it is recommended to use an Electronic Digital Torque Control to achieve accurate and consistent expansions. An electronic torque control works by monitoring the amperage (amp) draw of the motor and determining the power needed to reach the desired wall reduction. Once the motor reaches the power requirement, the torque control will cut off power to the motor. This allows repeatability and consistency from tube to tube.
Pneumatic Torque Control
Pneumatic motors with torque control act very similarly to electric motors. As resistance is encountered during wall reduction, the pneumatic torque control shifts a valve that stops the flow of compressed air to the motor. Power is reapplied as the motor is activated in reverse to release the tool from the tube.
Stall Torque / Dimensional Rolling
Stall torque motors are pneumatic motors with no internal torque control. These are generally used for dimensional rolling in boiler applications. This is when an operator rolls to a predetermined size by stopping the forward travel of the mandrel. This can be done with visual cues or by setting a mandrel stop. For dimensional rolling to be accurate and repeatable, the tubes must have controlled wall thicknesses and diameters. This process is usually used in roll beading or flaring applications.
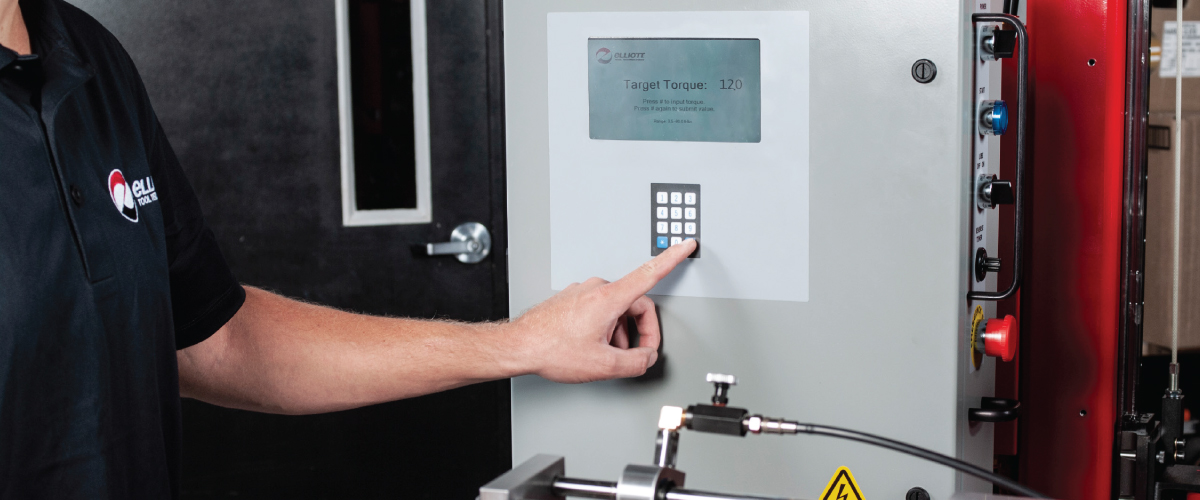
Determining RPM & Torque
Torque (Power) and RPM (Speed) have an inverse relationship, whereas one increases the other decreases. Speed is important because it helps maintain productivity and ensures that jobs get completed on time. However, having the highest RPM motor may not make sense for all applications. If you don’t have enough power to expand the tube, then the high speed will not make a difference.
In general, more speed is better when working with softer materials and more power is better when working with tougher materials. Below are some general industry recommendations for torque and RPM settings.
Considering Space Constraints
The style of rolling motor can also be important depending on the application. For example, wet back boilers have limited access to tubes, making standard rolling motors more difficult to use. One method to overcome this is to roll from within the combustion return area. This process requires a right angle rolling motor with a series of short mandrels, since the right angle head is able to work in tight spaces.
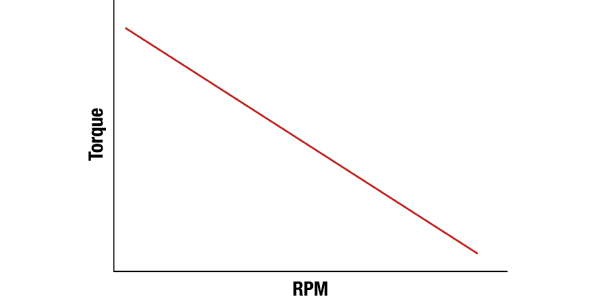
Overall, there are a lot of factors to consider when selecting the right rolling motor. Power source, torque control, RPM, torque, and style of motor will vary depending on the application. In general, electric motors are often used in smaller, more precise rolling applications or where air is not easily accessible. Whereas pneumatic motors are preferred in larger applications or environments where electricity cannot be used.
Industry RPM & Torque Guidelines
Tube OD Range | Free Speed RPM | Torque Range |
---|---|---|
1/4″ – 3/8″ (6.4 – 15.9mm) |
1,800 – 3,000 | 15 in lbs – 27 in lbs (1.7 – 3.1 Nm) |
5/8″ – 1″ (6.4 – 25.4mm) |
760 – 1,100 | 22 – 396 in lbs (2.5 – 44.7 Nm) |
1″ – 2″ (25.4 – 50.8mm) |
75 – 350 | 30 – 150 ft lbs (40.7 – 203.4 Nm) |
2″ – 4″ (50.8 – 101.6mm) |
75 – 190 | 30 – 305 ft lbs (40.7 – 413.5 Nm) |
4″ – 6″ (101.6 – 152.4mm) |
70 | 950 ft lbs (1,288 Nm) |
*Ranges may vary due to tube wall thickness, material, tube sheet thickness, lubrication, operation conditions, and/or operator technique.