Beyond Vessel & Deposits
Common Limitations for Tube Cleaning Selection
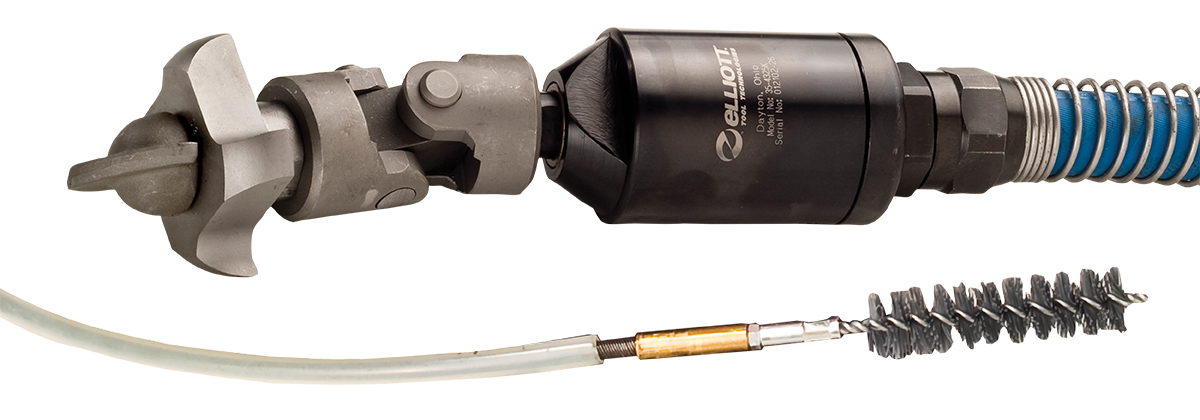
The abundance of tube cleaning methods on the market can make it challenging to select the best option for a specific application. While factors like vessel type and deposit composition are crucial, it’s equally important to consider the limitations of each cleaning method.
Type of Flush
One common limitation for cleaning methods is the type of flush required. Certain vessel types prohibit the use of water due to the potential for residue left in the tubes. In these cases, a dry flush application would be needed, limiting the number of options available.
Space Limitations
Another consideration when choosing a cleaning system is where the vessel will be cleaned. Cleaning a unit in a tight control room, versus an open shop environment will require very different set-ups. For example, using a rigid shaft style cleaner in a confined area would be very challenging, since a certain clearance is required for the shaft, in addition to the cleaning gun itself.
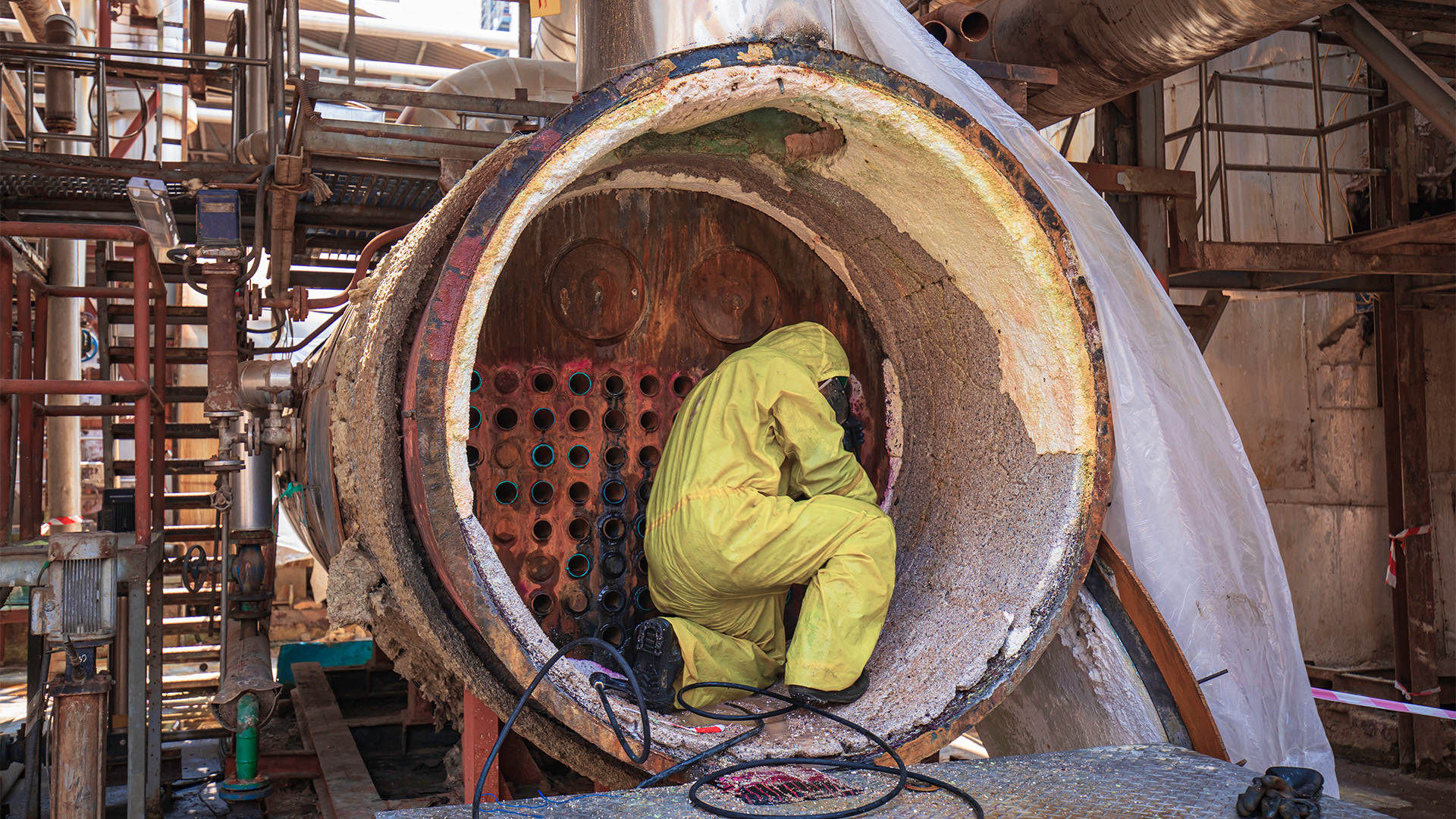
Tube Material & Enhancements
Coated or enhanced tubes are more susceptible to damage from heavier cleaning methods like turbine style cleaners. Due to the rotation of the motor and the aggressive nature of the cleaning head, this style of cleaner could scratch, dent, or break special tube coatings or enhancements.
This is also true in applications where the tube material is anything other than carbon steel. In non-carbon applications, the material is more likely to become damaged, potentially accelerating any existing tube wall loss. In this type of application, a brush style cleaner or water blasting would be preferred to avoid any damage to the tubes.
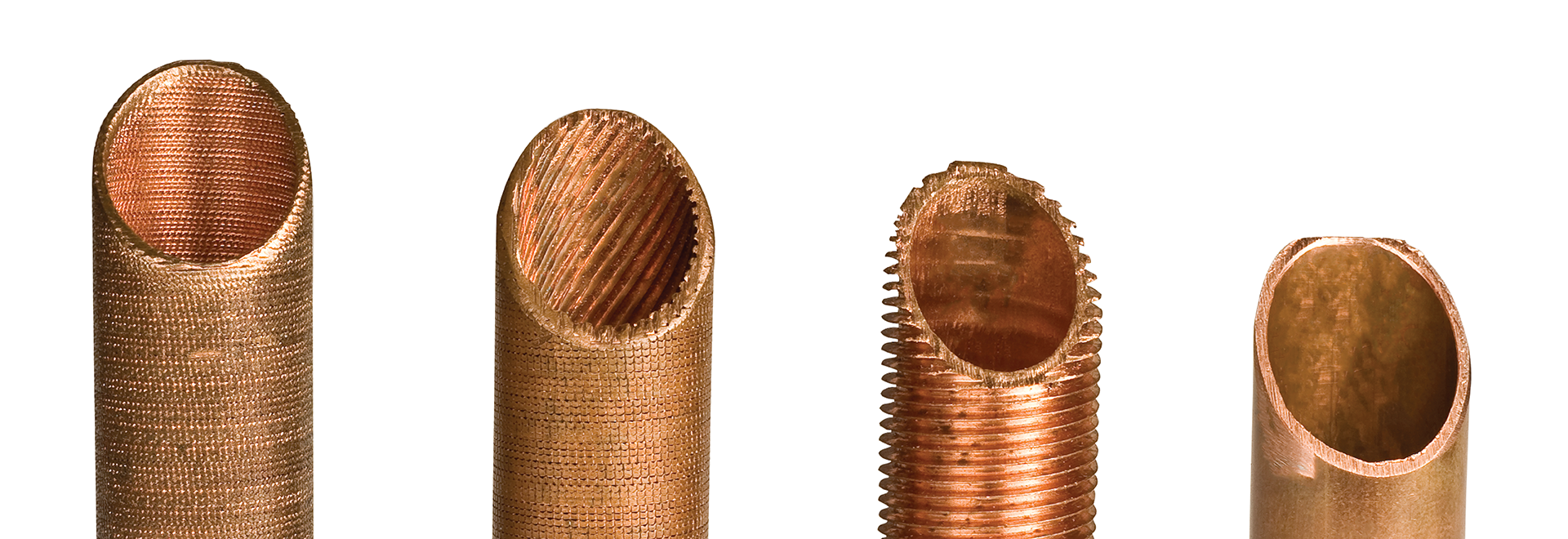
Bundle Configuration
U-tube style exchangers can present a challenge when cleaning due to the bend in the middle of the tube. Depending on the customer’s cleaning requirement, multiple cleaning methods may need to be used to effectively clean the bend. In longer bundles, a rigid shaft style cleaner could be used to clean the straight lengths, but an alternate turbine style cleaner may be required to clean the bends. This typically involves under sizing a motor and cleaning head to allow for it to pass through the curved portion of the tube.
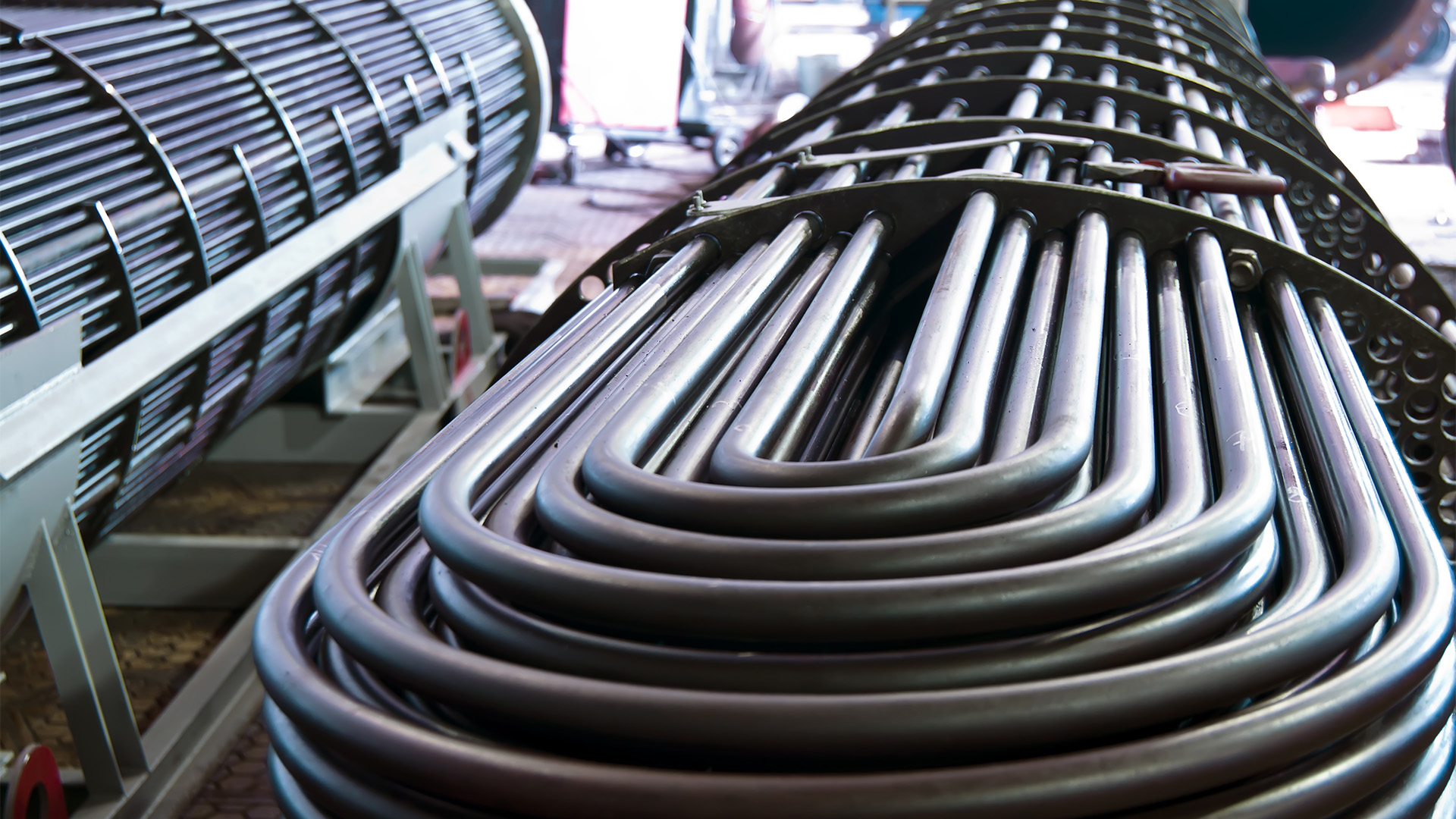
By carefully considering these factors, you can select the most appropriate tube cleaning method to effectively remove deposits and maintain vessel performance. For more information on selecting the right cleaning tool, contact our Application Specialist Team.