2 Common Types Of Tube Failure
How To Identify Fouling and Corrosion In Heat Exchangers
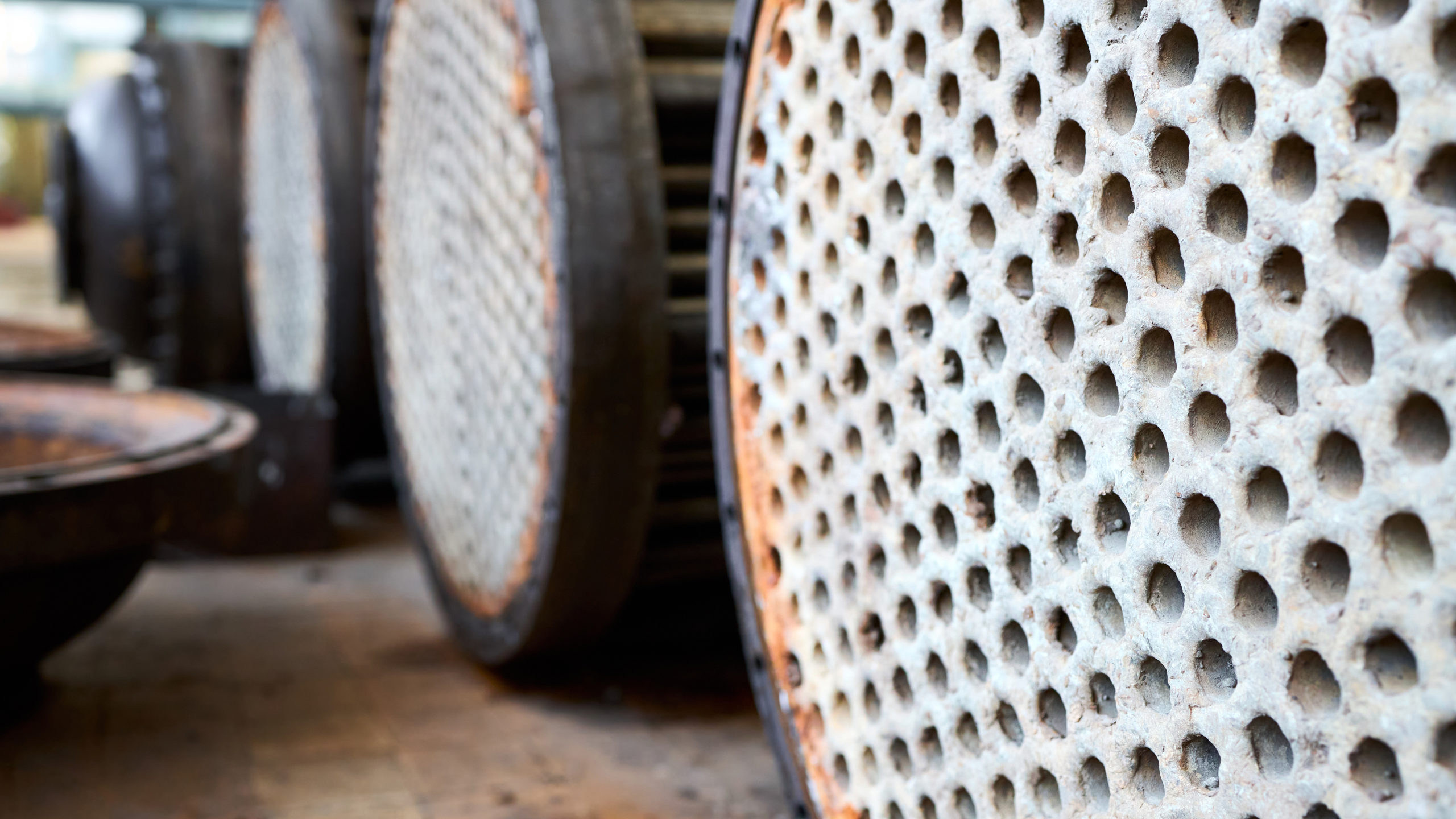
Heat exchangers are essential for many industries, but their performance can be significantly impacted by fouling and corrosion. These can lead to reduced efficiency, increased maintenance costs, and potential safety hazards. Understanding the mechanisms, impacts, and prevention strategies for fouling and corrosion is crucial for ensuring the optimal operation of heat exchangers.
Fouling and Scaling
One of the most common, and least severe, types of tube failure is fouling and scaling. Fouling describes the build-up of unwanted deposits in the tube. This can include mineral deposits, biological growth, and organic matter like oil or grease.
Types of Fouling
Scaling is a specific type of fouling caused by the precipitation of inorganic salts, primarily calcium, from hard water. As the water temperature increases, salts become less soluble and form hard, crust-like deposits on the heat transfer surfaces.
Another type of fouling is biofouling, which is common in marine applications. This is the accumulation of microorganisms like bacteria, algae, arthropods, or mollusks.
Impacts of Fouling and Scaling
Fouling and scaling can decrease heat transfer efficiency, increase maintenance costs and risk of corrosion, and reduce the lifespan of the exchanger.
- Reduced heat transfer efficiency: The deposits act as an insulating layer, reducing the transfer of heat.
- Increased pressure drop: Deposit build-up can narrow the internal diameter of the tube, restricting the amount of fluid that can pass through the tube. This will result in an increase in pumping power to maintain pressure.
- Increased risk of corrosion: Fouling creates localized areas of high concentration of corrosive substances, accelerating corrosion.
- Reduced lifespan: Combined effects of reduced efficiency, increased pressure drop, and corrosion can lead to premature failure of the exchanger.
Testing Methods
Various methods can be used to test for fouling, including visual inspection and pressure drop analysis. A pressure analysis evaluates the pressure difference between the inlet and outlet of the heat exchanger. A high pressure drop indicates fouling or scaling obstructions, while a low-pressure drop can indicate an internal leak where the system is running below capacity.
In marine applications, water sampling can also be used to identify biofouling. This will determine how much microbial contamination is present.
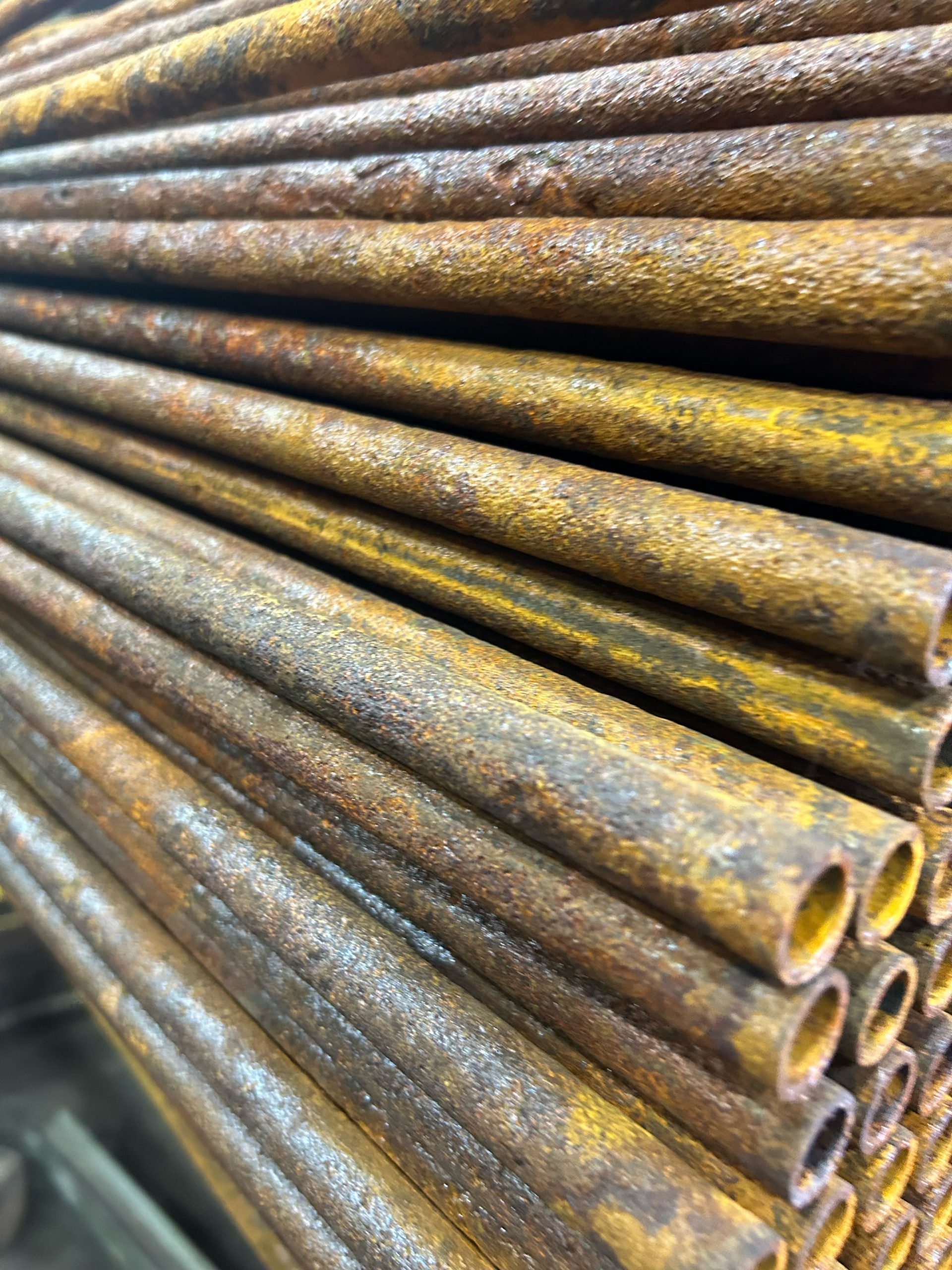
Corrosion and Erosion
Corrosion and erosion are two severe methods of failure that can degrade the performance and lifespan of a heat exchanger.
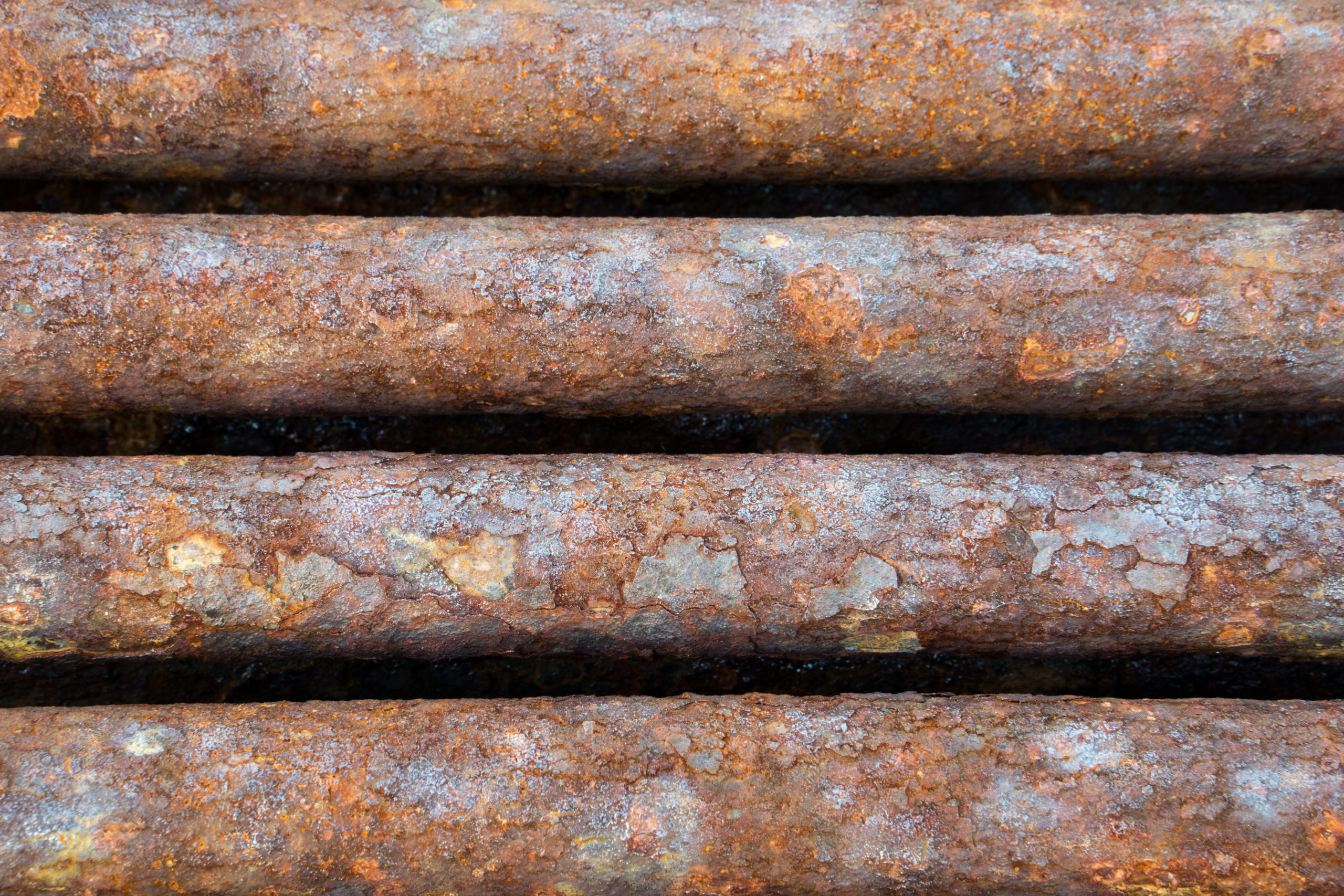
Types of Corrosion
Corrosion is the deterioration of a material due to a chemical reaction with its environment. In a heat exchanger, this is typically a result of a reaction between the tube material and the fluid running through the exchanger causing a reaction.
Galvanic corrosion occurs when two dissimilar metals are in contact with each other, generally due to tube plugging with a dissimilar material or an improper matching of component materials.
Pitting or crevice corrosion occur as a result of small pits or gaps in the metal surface, allowing fluids can accumulate and cause a localized reaction.
Types of Erosion
Erosion is the gradual wearing away of material due to the mechanical action of fluid. While different from corrosion, the impact of erosion on the heat exchanger is quite similar.
The most common cause of erosion is high-velocity fluid flow, which can erode the metal surface, especially in areas of high turbulence like bends, inlets, and outlets.
Impacts of Corrosion and Erosion
When corrosion and erosion occur together, the effects are often more severe. Erosion can remove protective oxide layers, exposing the underlying metal to further corrosion.
- Reduced heat transfer efficiency: corroded materials can form a layer on the heat transfer surface, increasing thermal resistance and reducing the heat transfer rate.
- Increased pressure drop: reduced flow area of the tubes or channels leads to an increased pressure drop, requiring higher pumping power.
- Structural damage: Corrosion can lead to significant metal loss, weaking the structural integrity of the heat exchanger. Additionally, corrosion can cause stress corrosion cracking, leading to sudden and catastrophic failures.
- Tube Leaks: Thinning tube walls can lead to leaks and potential for fluid mixing.
- Safety Risks: Fluid leaks can lead to the release of hazardous materials, and in some cases lead to fires or explosions.
Testing Methods
Ultrasonic testing and eddy current are the most common methods to reveal wall loss. Ultrasonic testing is a non-destructive testing method that uses high-frequency sound waves to detect defects. Similarly, eddy current testing uses an electromagnetic current passed through a coil to detect changes in the magnetic field.
Overall, fouling and corrosion are significant challenges that can affect the performance and longevity of heat exchangers. By understanding the underlying causes and implementing appropriate preventive measures, it is possible to mitigate these issues early on. Regular inspection and testing are essential for early detection and timely intervention to prevent catastrophic failures. By prioritizing these strategies, industries can optimize their heat exchanger systems and minimize downtime and operational costs.