Enhanced Part Durability: The Power of Roller Burnishing
In manufacturing, enhanced part durability is a constant pursuit. Roller burnishing, a cold working process, is a powerful technique to achieve this goal. By densifying and hardening the outer surface of a component, roller burnishing significantly improves its resistance to wear and premature failure, extending its operational lifespan and boosting overall performance. This process fundamentally alters the material’s properties, leading to tangible improvements in durability and reliability.
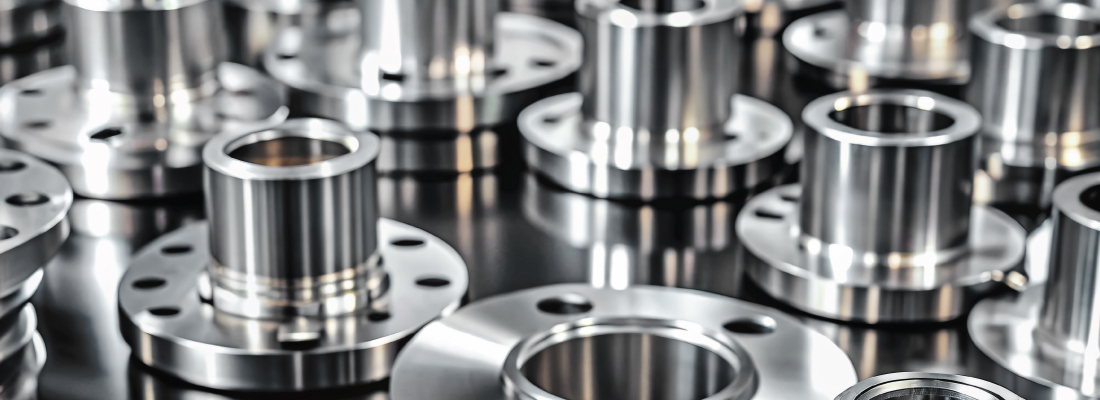
One of the primary mechanisms through which roller burnishing enhances durability is by increasing surface hardness. The cold working process imparts a high degree of plastic deformation to the material’s surface, resulting in a denser, more robust layer. This hardened surface acts as a formidable barrier against abrasive wear, a common cause of part degradation. Furthermore, the resulting smoother surface finish plays a crucial role in minimizing friction. When two surfaces interact, friction generates heat and mechanical stress, leading to wear over time. By reducing surface roughness, roller burnishing minimizes the frictional forces involved, thus decreasing the rate of material removal and preventing premature failure. In essence, the smoother the surface, the less force is required for movement, and the less material is lost to wear. This translates into a significant increase in the operational lifespan of the part, ensuring consistent performance over extended periods.
Beyond surface hardness and smoothness, roller burnishing offers the distinct advantage of introducing compressive residual stresses into the material. This prestressing effect is particularly beneficial in applications where parts are subjected to fluctuating loads or extreme environmental conditions. By inducing compressive stresses, the process effectively counteracts tensile stresses, which are the primary drivers of crack initiation and propagation. This is exemplified in the treatment of cylinder liner flanges in diesel motors. These flanges endure rapid and dramatic pressure and temperature changes during operation. By roller burnishing the corner of the flange, compressive stresses are introduced, significantly reducing the risk of fatigue failure and ensuring the engine’s reliability.
Furthermore, the smooth surface finish achieved through roller burnishing provides protection against corrosion. A rough surface, with its inherent imperfections and crevices, can act as a breeding ground for corrosive agents. Fluids and contaminants can easily accumulate in these areas, initiating and accelerating the corrosion process. By minimizing surface roughness, roller burnishing reduces the likelihood of fluid retention and exposure to corrosive environments. This enhanced corrosion resistance is particularly valuable in applications where parts are exposed to harsh conditions, such as marine environments or chemical processing plants. The smoother surface ensures that the part remains less susceptible to corrosion, maintaining its integrity and functionality over prolonged periods.
In conclusion, roller burnishing offers a multifaceted approach to enhancing part durability. The combination of increased surface hardness, reduced friction, compressive prestressing, and improved corrosion resistance translates into a significant increase in wear resistance and overall lifespan. This process empowers engineers and manufacturers to create components that can withstand demanding operating conditions, ensuring consistent performance and minimizing the risk of premature failure. As industries continue to strive for greater efficiency and reliability, roller burnishing stands out as a powerful tool in the pursuit of enhanced part durability, ultimately leading to improved performance and extended operational life.
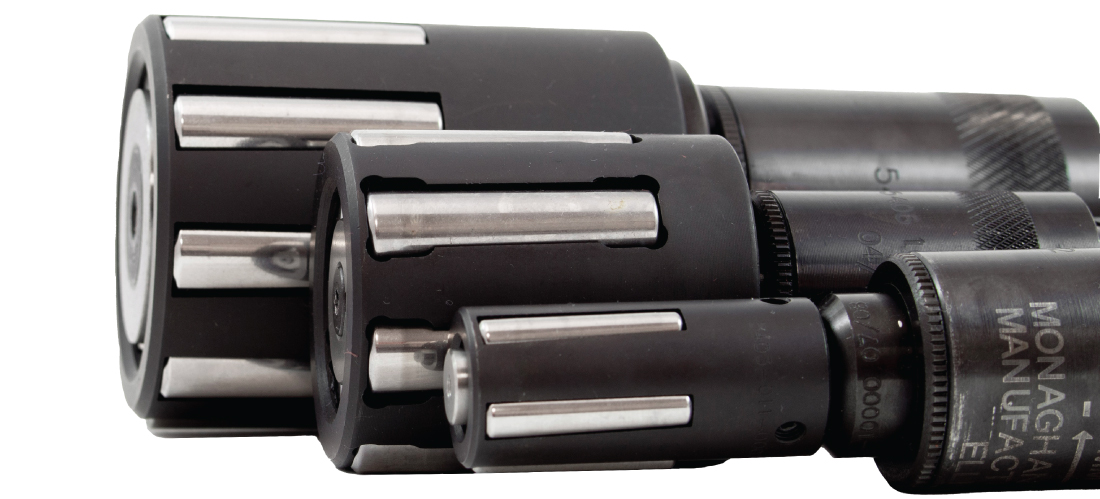