Cómo reentubar una caldera de locomotora
El diseño único y los desafíos comunes de mantenimiento
Históricamente, muchas empresas ferroviarias utilizaban locomotoras de vapor para el transporte. Hoy en día, la mayoría de las locomotoras de vapor están reservadas para ferrocarriles privados, museos y otras organizaciones benéficas. A medida que estos sistemas envejecen, presentan varios desafíos de mantenimiento únicos que pueden surgir debido al diseño y ubicación de estas unidades. Comprender la composición de las calderas de las locomotoras, así como las necesidades de mantenimiento, puede facilitar un poco los trabajos de restauración.
Una de las diferencias más notables entre una caldera estándar y una locomotora es el patrón de la placa de tubos. Muchas de las primeras locomotoras dependían de vapor saturado o húmedo para su uso en operaciones madereras y mineras. Si bien fue efectivo, este método de producción de energía resultó en una menor producción de caballos de fuerza. Para hacer que el motor sea más potente, se agregaron supercalentadores para convertir el vapor saturado en vapor seco, para obtener una mayor producción de energía. Este diseño dio como resultado un patrón de placa de tubos que consta de tubos de caldera de 2″ y 4 conductos de sobrecalentador de 5,5″. Si bien este diseño hace que la unidad sea más eficiente energéticamente, puede dificultar la instalación de los tubos. Dado que la mayoría de las herramientas estándar para calderas tienen un diámetro exterior de hasta 3”, se requieren expansores de tubos personalizados para adaptarse a los conductos de humos.
Además, los espacios reducidos para el expansionado de los tubos pueden dificultar la instalación de un motor, por lo que a menudo se utilizan juntas universales para facilitar la instalación en esquinas estrechas.
Otro desafío espacial implica inspeccionar la cúpula de vapor en la parte superior de la unidad. El cuerpo del acelerador ocupa la mayor parte del espacio, lo que obliga al operador a moverse en un espacio de trabajo muy reducido. En caso de que sea necesario completar algún trabajo en esta área, puede resultar extremadamente difícil instalar herramientas, y mucho menos un motor, debido a limitaciones de espacio.

Placa tubular en una caldera de locomotora, imagen proporcionada por Engine 557 Restoration Company

Chimeneas en expansión en una caldera de locomotora, imagen proporcionada por Engine 557 Restoration Company
En lo que respecta al mantenimiento rutinario de las calderas de locomotoras, la Administración Federal de Ferrocarriles establece muchas de las directrices que siguen estas organizaciones. Generalmente, las unidades deben cambiarse de tubo aproximadamente cada 15 años. Esto garantiza que toda la caldera cumpla con los códigos de seguridad y funcione de manera eficiente. La extracción del tubo a menudo se realiza usando un soplete para cortar los extremos del tubo en un lado del espejo, seguido por la extracción de los extremos del tubo rebordeado. Una vez que se ha removido el rebordeo, se corta una costura en el medio de la parte expandida del tubo para aliviar la fuerza del aro, lo que permite colapsar los trozos de tubo y sacarlos con un martillo neumático. En el lado largo del tubo, se utiliza un sistema estilo varilla y pasador para retirar el tubo del espejo. Esto implica hacer un agujero en el tubo, asegurar un perno y sacarlo con una correa o cadena.
Una vez que se retiran todos los tubos, la placa de tubos y otros componentes de la caldera se someten a una inspección completa antes de volver a instalar los tubos. Los orificios de la placa tubular pueden agrandarse con el tiempo y a menudo se utilizan férulas para prolongar la vida útil del espejo.
Entre los trabajos de cambio de tubería, las calderas tendrán limpiezas de rutina conocidas como limpieza de arena, donde se rocía arena en la cámara de combustión para eliminar cualquier depósito o acumulación de operación. Los cepillos de humos también se utilizan habitualmente para la limpieza de tubos. Además, se realizan inspecciones periódicas para verificar si hay fugas o daños en los tubos. Si un tubo no pasa la inspección, se puede tapar hasta que la unidad esté lista para mantenimiento.
En general, el diseño de la caldera de la locomotora tiene varias diferencias con respecto a una caldera estándar, lo que puede presentar algunos desafíos únicos en lo que respecta al mantenimiento. Desde los diferentes tamaños de tubos y conductos de humos hasta el trabajo en espacios reducidos, hay muchos factores diferentes que entran en juego al considerar las herramientas y completar los trabajos de mantenimiento. Comprender mejor los requisitos de mantenimiento y las opciones disponibles puede ayudar a facilitar este proceso.
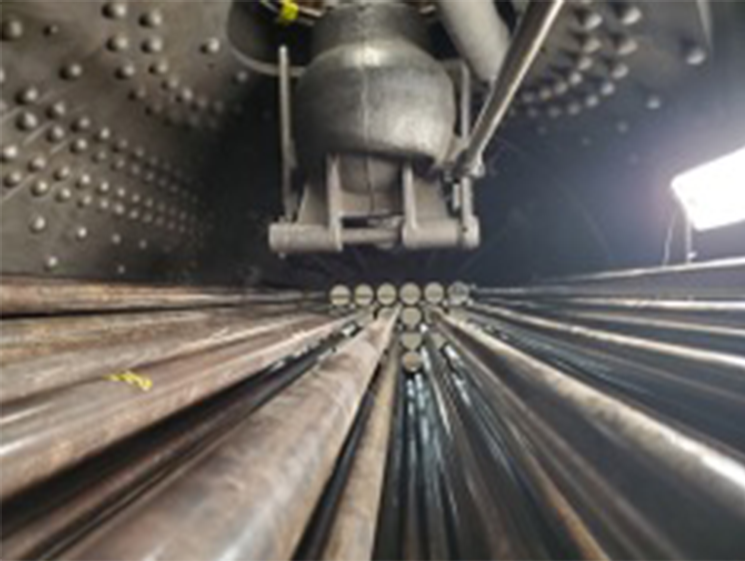
Vista del cuerpo del acelerador dentro de la cúpula de vapor, imagen proporcionada por Engine 557 Restoration Company