Evaluating Performance Of Single Roll vs Multi-Roll Burnishing In Different Applications
Burnishing is a manufacturing process that improves the surface finish and dimensional accuracy of components by applying compressive stress. This is achieved by passing a hardened roller or set of rollers over the workpiece, resulting in a smoother, harder, and more wear-resistant surface. Two primary types of burnishing tools are available: single roll and multi-roll. Understanding the differences between these tools will help you select the right tool for the job.
Single Roll Burnishing
As the name suggests, single roll burnishing utilizes a spring loaded, hardened roll to achieve the desired surface finish. The tool is typically mounted on a stationary tool post and fed along the length of the workpiece. This method is well-suited for:
- Longer parts: Single roll burnishing can effectively process longer workpieces where maintaining consistent pressure and surface finish across the entire length is critical.
- Tight manufacturing tolerances: This method excels in applications where dimensional accuracy is well controlled, as it won’t remove material or make up for large differences in tolerances.
- Large diameters & complex geometries: Single roll tools can effectively process parts with larger diameters, due to the versatility of the design. Additionally, single roll tools can accommodate contours, gaps, and other unique part geometries.
Limitations of Single Roll Burnishing:
- Slower processing speeds: Due to the slower feed rates required to maintain consistent pressure and avoid excessive deformation, single roll burnishing can be a more time-consuming process when compared to multi-roll burnishing.
- Small diameters and thin walls: Since smaller parts are more susceptible to deformation under pressure, a single roll tool would be less ideal, as all the force would be concentrated in one area of the tool.
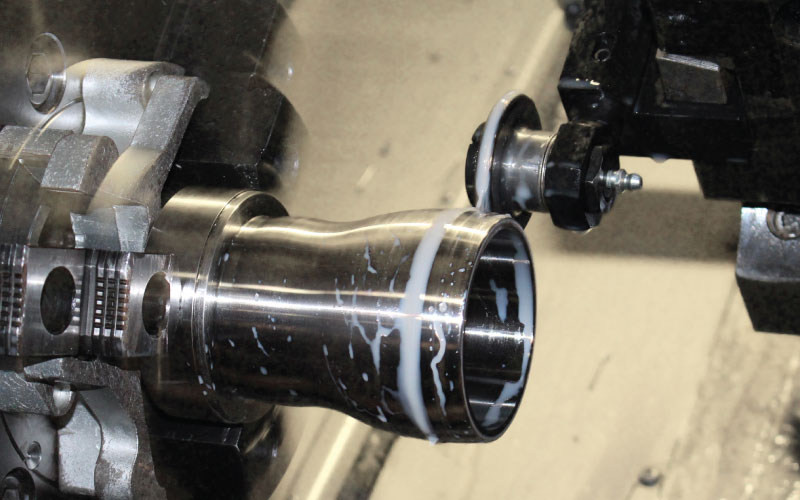
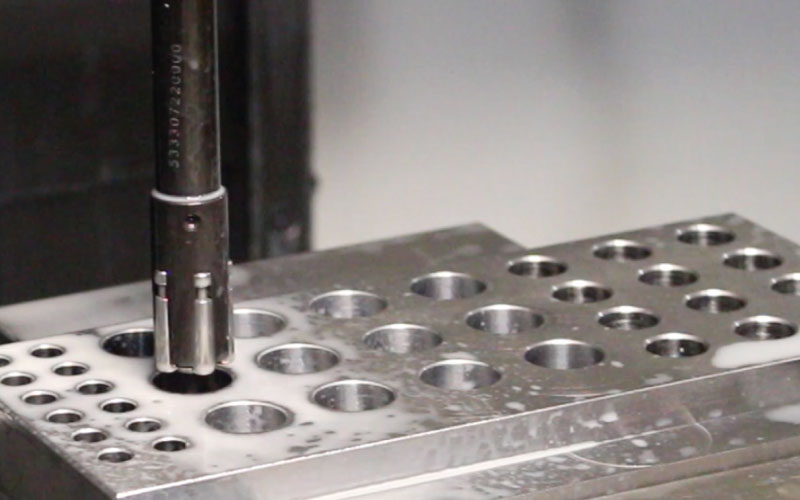
Multi-Roll Burnishing
Multi-roll burnishing employs multiple hardened rolls arranged in a specific configuration, often in a radial or axial arrangement. This configuration allows for:
- Processing smaller diameters: Multi-roll tools are particularly well-suited for processing smaller diameter parts. The multiple rollers distribute the pressure more evenly, minimizing the risk of deformation that can occur with single roll burnishing on smaller parts.
- Improved dimensional accuracy: Multi-roll tools enter the bore at a set diameter, allowing it to make up for larger variations or discrepancies in sizing. This helps to ensure dimensional accuracy when less precise manufacturing methods are utilized.
- High Volume Mating Surfaces: Some applications for angled or flat faces require a repeatable process that yields fine finishes for seals and mating parts.
Limitations of Multi-Roll Burnishing:
- Shorter parts: The length of the multi-roll tool restricts its use to shorter workpieces in small diameter bores.
- Challenges with complex geometries: Multi-roll tools may not be suitable for processing parts with complex contours or curved surfaces.
Choosing The Right Tool
The selection of single roll or multi-roll burnishing tool depends on several factors, including:
- Part geometry: Consider the length, diameter, and complexity of the workpiece.
- Material properties: The hardness, ductility, and other material properties will influence the choice of burnishing method.
- Tolerances and surface finish requirements: The desired level of dimensional accuracy and surface finish will dictate the appropriate tool and process parameters.
- Production volume: The required production volume will influence the choice of tooling and the overall cost-effectiveness of the process.
By carefully considering these factors, manufacturers can select the most appropriate burnishing method to achieve the desired results while optimizing production efficiency and minimizing costs.
Summary
Single roll burnishing is generally preferred for longer parts or those with complex geometries, while multi-roll burnishing is well-suited for smaller diameters and applications where dimensional accuracy is critical. By understanding the strengths and limitations of each method, manufacturers can make informed decisions to optimize their burnishing processes and improve the quality and performance of their products.