How Ductility Impacts Surface Finish
Surface finish plays a crucial role in the performance, durability, and quality of a manufactured part. A smoother finish reduces the amount of friction and premature wear on a part, ultimately increasing its longevity and performance. Burnishing, a process that involves compressing the surface of a part, is a popular method for improving surface finish. However, the success of burnishing depends heavily on the ductility of the material being processed.
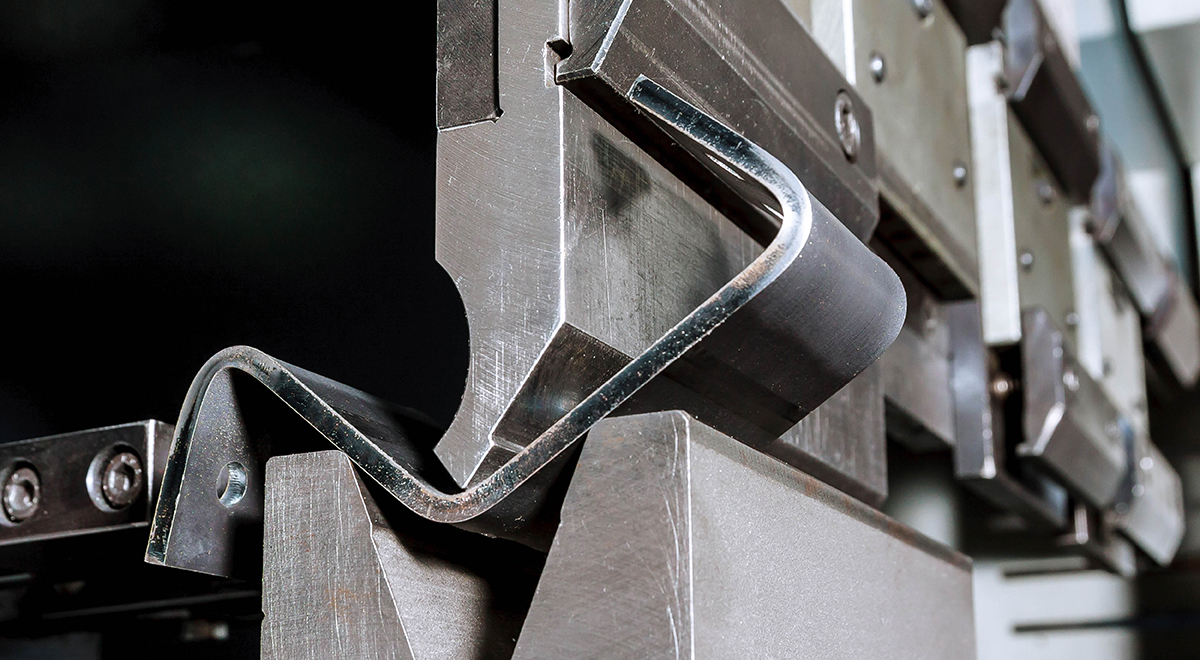
Understanding Ductility
Ductility is a material property that describes its ability to deform under tensile stress without fracturing. it’s the material’s ability to be stretched or bent without breaking. Materials with high ductility, such as gold, silver, and copper, are more easily deformed than those with low ductility, such as cast iron and tungsten.
High Ductility Materials |
Low Ductility Materials |
---|---|
Gold | Cast Iron |
Silver | Tungsten |
Copper | Molybdenum |
Aluminum | Zinc |
Nickel | Rigid Plastics |
Titanium | Ceramics (ie. porcelain) |
Note: The ductility of a material can depend on factors such as temperature, strain rate, and grain size
On the opposite end of the spectrum, if the feedrate is too high, the tool may not spend enough time on the surface to achieve plastic deformation. This can result in a rougher surface finish and leave visible tool marks on the surface. To get the best performance out of the tool, it’s important to find the optimal feedrate that allows the tool to deform the surface enough that it creates a smoother and more polished finish. The best feedrate ensures the tool maintains consistent contact with the surface, providing uniform compression and material flow. Depending on the tool itself, a minimum feedrate may be required to produce consistent results.
Ductility and the Burnishing Process
Ductility plays a significant role in burnishing operations. Highly ductile materials flow more easily under pressure, allowing for a smoother and more consistent finish.
Burnishing High-Ductility Materials
Ideal Starting Finish: For highly ductile materials, a course peak and valley pattern (60-120 Ra) is recommended. This provides a good starting point for compression and helps achieve a smoother final finish.
Burnishing Low-Ductility Materials
Smoother Starting Finish: A smoother starting finish (less than 40 Ra) is generally recommended to ensure efficient material flow and to reduce burnishing time. As a general rule, the turned finish can be cut in half with a burnishing tool.
Overall, ductility is a critical factor in determining the success of a burnishing operation. By understanding the ductility of the material being processed, manufacturers can select the appropriate burnishing parameters and surface preparation techniques to achieve the desired surface finish.
For more information on ductility and finishes, contact our application support team.