Increase Tool Life On Tough Materials
Extending The Life Of Condenser Expanders
As end users strive for increased heat transfer efficiency, customers are often tasked with building vessels that will withstand heavy use and the test of time. This often results in the use of more wear resistant tube sheet and tube materials, such as Inconel, Hastelloy, and Duplex Stainless Steel. While exotic materials often mean longer tube life, they can take a big toll on expander tool life. In this article, we will cover some simple tips & tricks that can be used to get the most life out of your tube expanders when working with tough materials.
One of the biggest challenges when working with tough materials is that they have a higher yield strength and are more prone to work hardening. Yield strength describes the force required to permanently deform a material so that it’s unable to return to its original shape. Achieving this “plastic state” is crucial during expansion because it’s required to create a leak free mechanical joint. When working with materials like Inconel or 2205, it takes more force to deform the material and create a mechanical joint before the material hits its plastic state. This means the tool must work even harder, which can result in overheating and premature failure. For example, rolling a 14 BWG Inconel tube vs Carbon Steel can use up to 3Xs as many tools depending on the job specifications.
Short Roll vs Long Roll Expanders
In thicker tube sheets applications over 2-1/2”, step rolling with a long roll expander is common practice. This allows the entire length of the tube sheet to be expanded in fewer steps compared to using a short roll expander. However, when working with tougher materials, long roll tools may not be the best solution. In applications with heavy wall tubing or tough tube materials, long roll expanders may not be able to generate enough force to create a good mechanical seal. This is because the more contact the tool has, the more wear it will experience. Additionally, even if the tool can expand the material, the length of the roll can lead to quicker tool failures. As a result, it can be more beneficial to use a short roll tool and complete an additional step to reduce the number of expanders and set-ups required for the job.
Clean & Cool
Debris and overheating are two of the biggest culprits when it comes to expander wear. Expanding tougher tube materials will require more lubrication be applied at more frequent intervals in order to keep the tool cool. This increase in lubrication will help keep the expander from overheating, however, frequent cleaning will also be necessary. Best practice is to have at least 2 expanders set up, so they can be swapped out for cleaning.
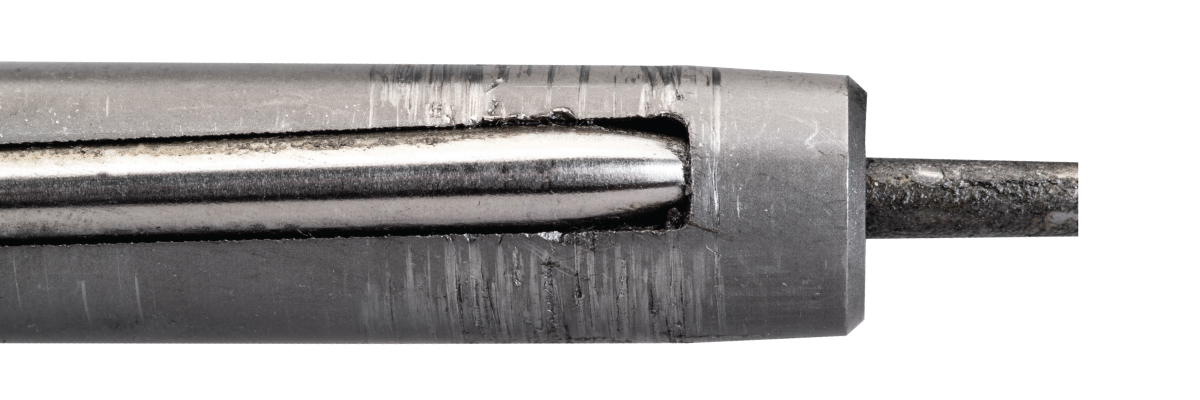
Figure 1. Wear on Expander Cage
Expanding Welded or Heat-Treated Areas
Another common issue when expanding tougher materials is expanding over a seal weld or a heat treated area of the tube. When tube ends are welded, the amount of heat needed to create the weld causes the material to harden. If the expanding rolls come in contact with the welded bead during expansion, they will break. This is especially the case on tougher tube materials. A common method to prevent the expander from working over the weld is to use relief rolls or adjust the depth of the expander 1-1/4” – 3/8” past the welded area.
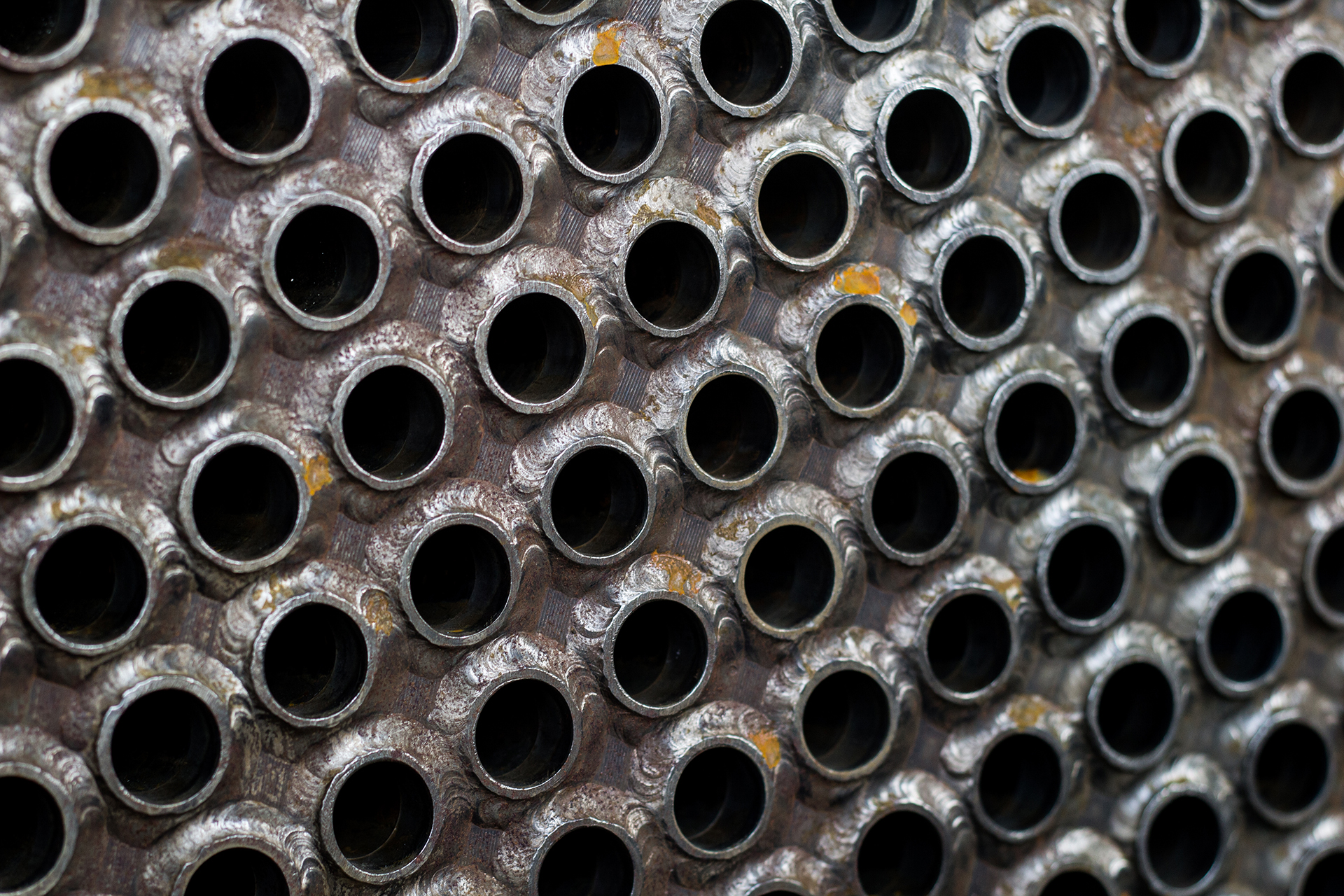
Figure 2. Seal Welded Tubes
Overall, expanding tough materials like Inconel, Hastelloy, and 2205 Stainless Steel can reduce tool life by up to 50% depending on the severity of the application. As a result, it’s important that preventative steps are taken to decrease the amount of premature wear put on the expander. This can be done by selecting short roll expanders, increasing the amount and frequency of tool lubrication, regularly cleaning and inspecting tooling, and utilizing relief roll expanders on welded joints.
Contact our Application Team for more information about working with tough materials and check out other articles in this series.