Increase Efficiency of Electric Motors
How roller burnishing can improve manufacturing tolerances in laminated stacks
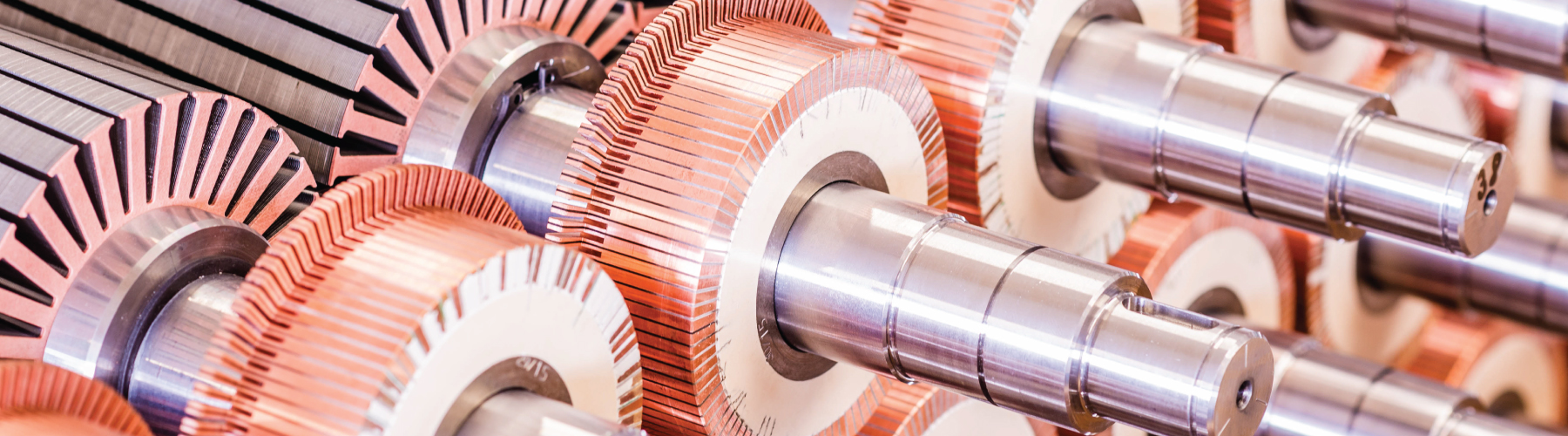
Electric motors are used in a wide variety of applications, from lawn tools to automobiles. While there are many different styles of electric motors, the general operating principle is the same; they work to convert electrical energy into mechanical energy. The efficiency of the motor will depend on how much power is required to convert electrical current into energy. Efficiency is greatly impacted by materials, design, and manufacturing processes. When looking at laminated motors, tight manufacturing tolerances are ideal for producing higher efficiency products. In this article, we will review the basic construction of an electric motor, the benefits of laminated stacks, and how burnishing can improve manufacturing tolerances.
What Are Laminated Stacks?
Typically, all electric motors are run by a rotor and a stator. In operation, the stator remains stationary and provides the electromagnetic force that causes the rotor to spin. The spinning of the rotary is what ultimately converts electrical current into energy. In many cases, both the stator and the rotor are made up of laminations, as opposed to solid pieces. Laminations are thin layers of metal stamped into a specific design and assembled to create a lamination stack, as shown in Figure 1.
Lamination stacks are beneficial because they reduce the amount of energy lost in operation, thus improving the efficiency of the motor itself. A more efficient motor will generally last longer and have lower operating costs.
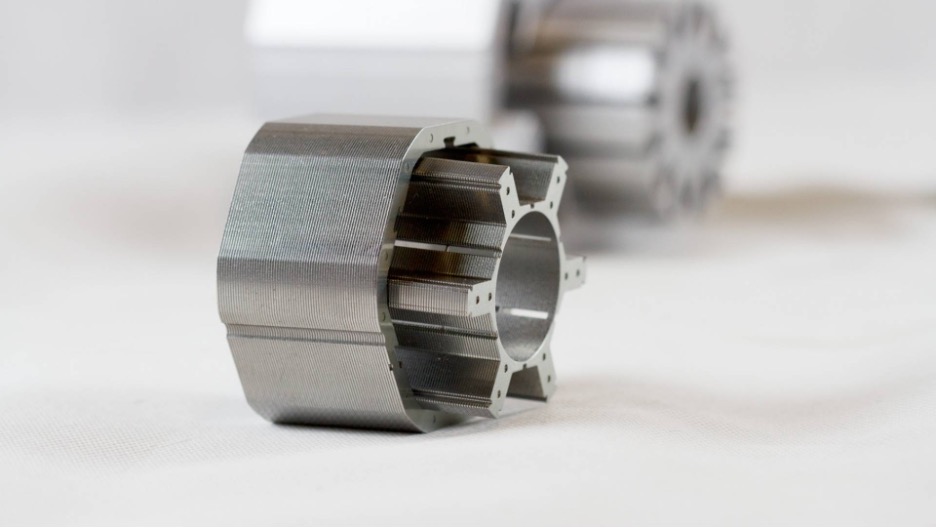
From R. Bourgeois Group, https://www.rbourgeois.com/products-services/rotor-and-stator-lamination-assemblies/
Lamination Stack Assembly & Finishing
While laminations provide many benefits for operation, the manufacturing, assembling, and finishing of the stack can make a huge difference in the motor’s efficiency. In general, the smaller the gap between the inner diameter of the stator and the outer diameter of the rotor, the less power that is required for the motor to operate. However, a tight gap between these two pieces means there is very little room for manufacturing or assembling errors, as an overset lamination or incorrectly sized part can interfere with the rotor and cause premature wear or failure of the part.
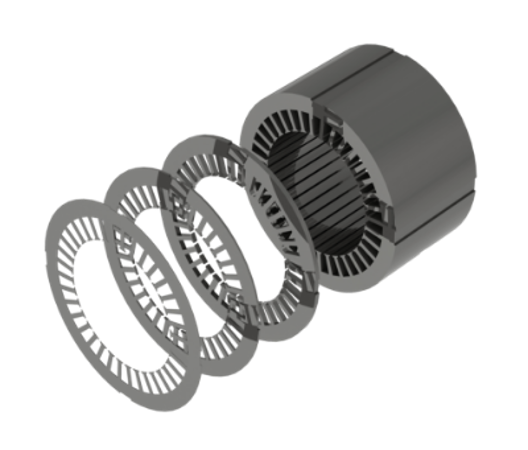
From Carpenter Electrification, https://www.carpenterelectrification.com/stator-rotor-stacks
One challenge that can occur is offset laminations. This can happen due to machining tolerances on dowel holes or assembly error. Since the individual laminations are stacked to form the stator, if any of the laminations are offset, it can result in interference with the rotor. This is especially true in designs where the rotor is operating with very little air gap. To ensure that laminations form a consistent ID, a finishing or sizing operation can be performed after assembly.
Grinding & Honing
Traditionally, many manufacturers will send the lamination stack through a grinding and honing process to create a consistent size through the inner diameter of the stator. One of the biggest issues with grinding and honing is that it adds a significant amount of time to a job, not only due to set-up but also cleaning in between each step to remove residue. Additionally, honing is a more specialized process that requires dedicated equipment, so many customers end up outsourcing parts adding cost and lead time.
Roller Burnishing
One of the easiest ways to set the gap on the lamination stack is to use a roller burnishing tool. While the surface may not need to be burnished in the traditional sense, in this application the roller burnishing tool will act as a sizing tool. Since burnishing tools are sized to a specific inner diameter, they will allow the manufacturer to hold to a very precise finished ID. Additionally, since burnishing does not remove material, adjustability increments of .001” allows the user to hold incredibly tight tolerances. If manufacturing tolerances are greater than what can be burnished, grinding and honing may be required.
Aside from its precision, roller burnishing is also an all-in-one operation that can be run on a CNC, reducing set-up time and cost when compared to other finishing operations.
Conclusion
Overall, electric motors are an important part of everyday appliances, heavy machinery, automobiles, and much more. The more efficient the electric motor, ie. the easier it can convert electrical current into mechanical energy, the better performance you’ll see out of end products. One method for improving the efficiency of an electric motor is by using lamination stacks for the rotor and stator, as they reduce overheating and energy loss while in operation. While they may be more efficient, laminations can be challenging to align precisely when creating the stack. Any offsets in the stack can lead to interference while the motor is in operation, reducing the life and performance of the motor. Roller burnishing tools are an easy and cost-effective way to get a precise air gap between the stator and rotor.
For more information on burnishing applications, contact our application support team.