Reducing Scrap and Energy Use with Mechanical Joining
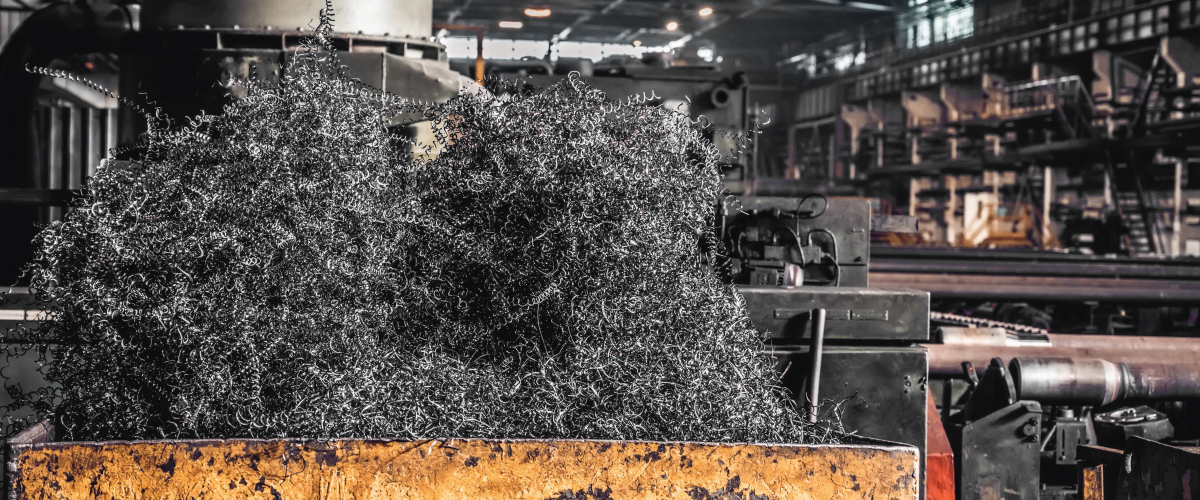
Mechanical joining is a crucial process in various industries, including aerospace, automotive, and heavy machinery. It’s used to create a leak-free seal between a tube and a fixed container by expanding the outer diameter of the tube into a series of grooves. This cold working process offers significant sustainability advantages over traditional methods like welding and brazing.
Energy Efficiency
Reduced Energy Consumption
Welding and brazing require high temperatures, often achieved through the combustion of fuels like propane or acetylene. This significantly increases energy consumption compared to mechanical joining, which is a cold working process.
Diverse Power Sources
Mechanical joining can be performed using various energy sources, including electric or pneumatic motors, drills, or even manual torque wrenches. This flexibility can amount to greater energy savings when used at scale.
Material Conservation
Elimination of Filler Metals
Welding and brazing require the use of filler metals, which can contribute to increased material consumption and waste. Mechanical joining, on the other hand, utilizes the existing metal of the tube, minimizing waste.
Reduced Scrap Rates
Welding and brazing can often lead to material distortion, warping, or even the need for rework due to heat-affected zones. Mechanical joining minimizes these risks, reducing the amount of scrap material generated.
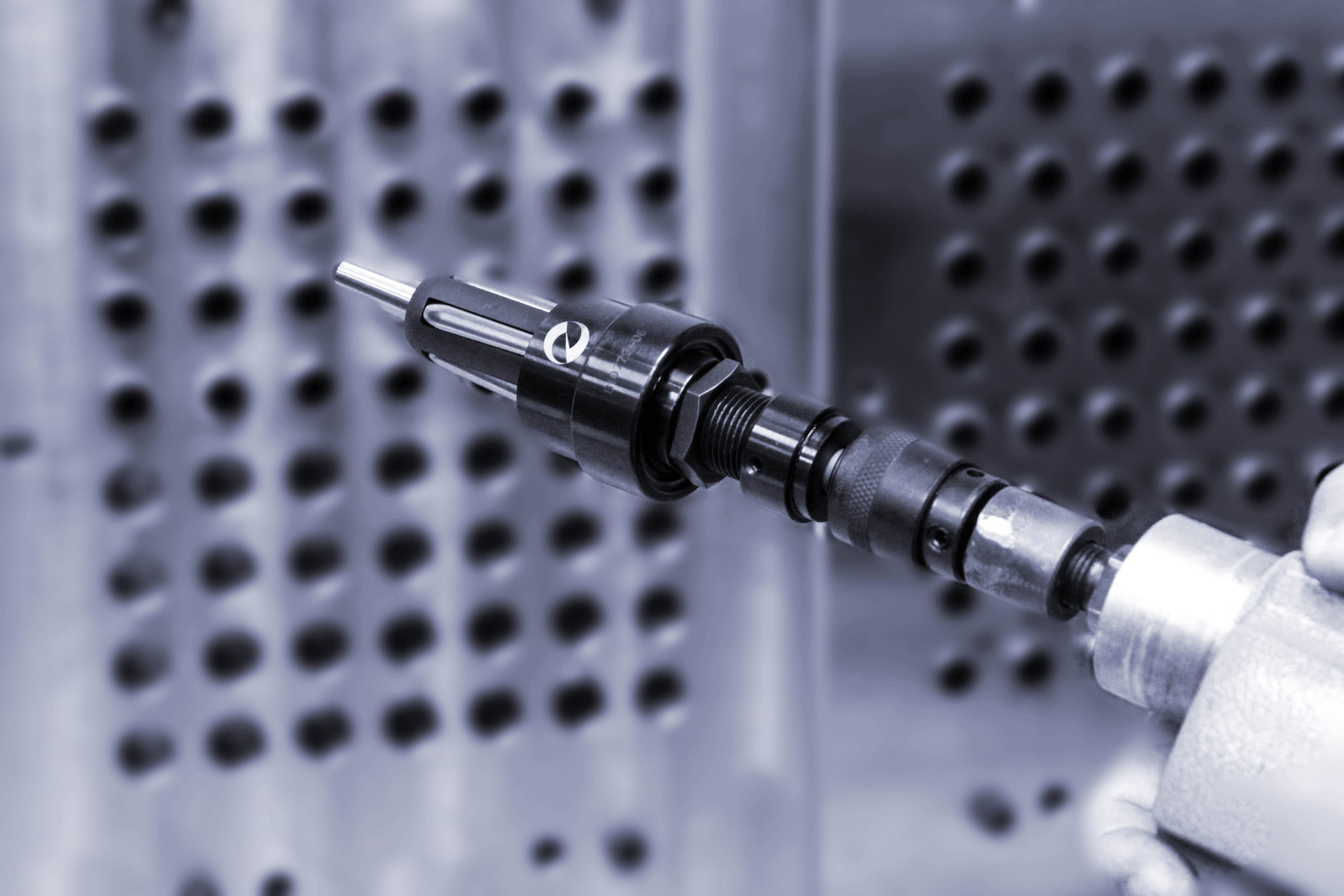
Human & Environmental Impact
Reduced Emissions
Welding and brazing processes often generate harmful emissions, such as fumes and particulate matter. Mechanical joining, being a cold working process, produces no such emissions, contributing to a cleaner and healthier working environment.
Lower Carbon Footprint
By reducing energy consumption and minimizing material waste, mechanical joining significantly lowers the carbon footprint of manufacturing processes.
Benefits Beyond Sustainability
Improved Quality
Mechanical joining often results in higher quality joints with improved leak tightness and fatigue resistance compared to welding or brazing.
Increased Productivity
The speed and efficiency of mechanical joining can lead to increased productivity and reduced manufacturing times.
Versatility
Mechanical joining can be applied to a wide range of tube sizes and materials, making it a versatile solution for various applications.
Conclusion
In an era of increasing environmental awareness, sustainable manufacturing practices are crucial. Mechanical joining presents a compelling alternative to traditional joining methods, offering significant advantages in terms of energy efficiency, material conservation, and environmental impact. By embracing this technology, manufacturers can not only reduce their environmental footprint but also improve product quality, enhance productivity, and gain a competitive edge in the market.