Roller Burnishing for Stronger, Longer-Lasting Parts
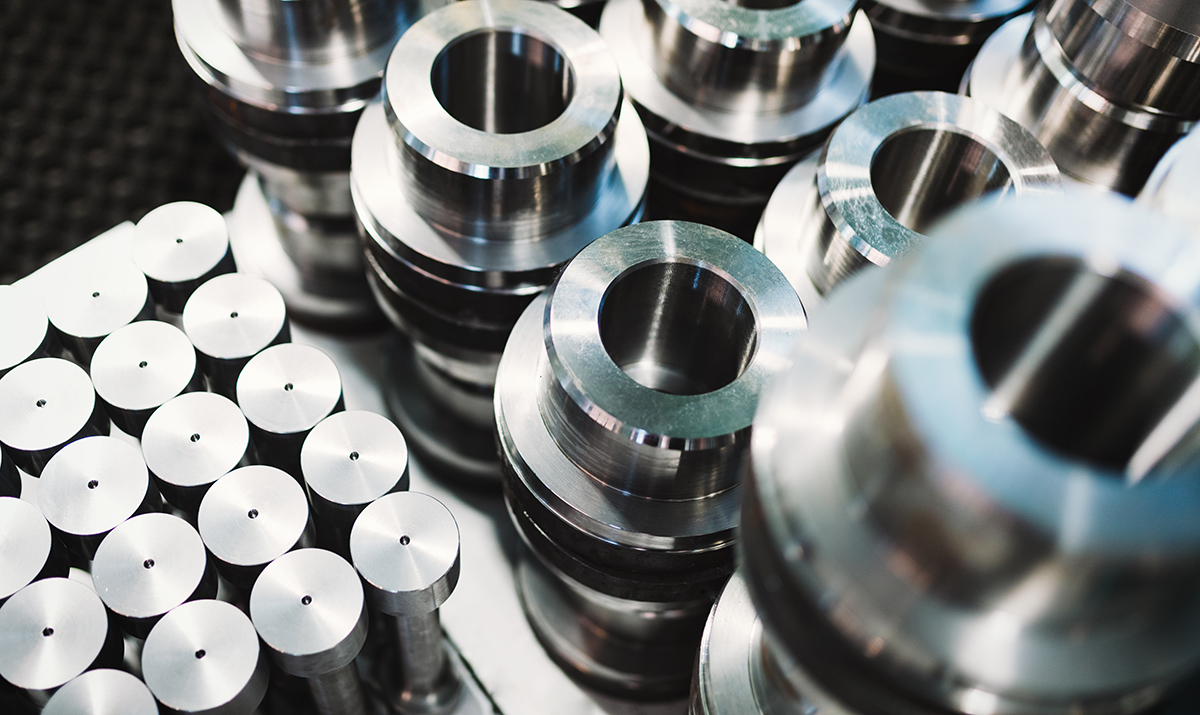
Roller Burnishing Roller burnishing is a cold working process that improves the surface finish and mechanical properties of part without removing material. This process involves applying pressure to a surface, resulting in a cold worked layer that offers several advantages including wear resistance, performance, and part life.
Improve Wear Resistance
Higher Surface Hardness
Burnishing is a machining process that cold works the metal without removing material. Rather it compresses or “irons-out” the peaks of a metal surface into the valleys, resulting in a uniform surface. One benefit of cold working material is that it causes the metal’s crystal structure to be distorted and rearranged, ultimately increasing the surface hardness of the material. As a result, the higher hardness provides an increased resistance to abrasion and wear.
Reduces Friction
A smoother surface finish will make a part less susceptible to wear, as it reduces friction. Friction is a force that resists relative motion between two surfaces that come in contact. Lower friction means less force is required to move one surface over another, reducing the amount of material that is worn away in operation. Additionally, less friction lowers operating temperatures, preventing premature failure of the part.
Enhance Performance
Similar to wear resistance, the cold-worked layer produced during burnishing can also provide fatigue and corrosion resistance.
Reduce Stress Concentrations
Stress concentrations are localized areas where stress is particularly high. These areas of stress can result in fatigue cracks, leading to premature failure of the part. Burnishing can help to reduce stress concentrations by smoothing out surface irregularities and refining the grain structure of the material. This provides fatigue resistance for the part. Burnishing can also be used to prestress the material. Prestressing machined parts involves applying controlled pre-compression to critical areas of a part to enhance its strength, fatigue resistance, and dimensional stability under operational loads. This technique is especially relevant in high-stress applications, such as aerospace, automotive, and heavy machinery, where parts are subjected to intense, repetitive loads.
Corrosion Resistance
Burnishing produces a smoother surface finish, reducing the likelihood of corrosion in some materials. A rougher surface provides a larger surface area for corrosive substances to come into contact with. Additionally, rough surfaces are more likely to have crevices and trap fluids which can create localized corrosive environments. A smoother surface, on the other hand, minimizes the area exposed to the environment and is less likely to retain fluid, reducing the potential for corrosion.
Increase Part Life
Increased part life is largely due to a combination of the elements listed above. Burnishing’s ability to improve wear resistance, reduce fatigue, and minimize the likelihood of corrosion all contribute to reduced part maintenance. Parts with enhanced wear resistance and performance can operate for longer periods of time without failure, increasing the overall life of the part.
Roller burnishing stands as a versatile and effective cold working process that significantly enhances the performance and lifespan of various components. By creating a hardened, wear-resistant surface layer, reducing friction, and improving fatigue and corrosion resistance, roller burnishing offers a multitude of benefits for manufacturers across industries. From automotive and aerospace to machinery and consumer goods, the application of roller burnishing can lead to improved product reliability, reduced maintenance costs, and increased customer satisfaction.
Overall, roller burnishing is a versatile finishing process that offers significant benefits to a wide range of automotive components. By increasing surface hardness, improving surface finish, and reducing stress concentrations, roller burnishing enhances durability, reliability, and performance. From crankshafts to bearing surfaces, this process plays a vital role in ensuring the longevity and efficiency of automotive systems. As the automotive industry continues to evolve, roller burnishing will remain a valuable tool for improving component part quality and vehicle performance.
For more information on enhancing part performance with burnishing tools, contact our Metal Finishing Application Specialist Team.