Strategies for Successful Heat Exchanger Tube Plugging
Plugging leaking tubes in heat exchangers is a critical maintenance task to ensure safe and efficient operations. However, this seemingly straightforward procedure can present a multitude of challenges that can impact both the success of the plug and the overall maintenance process. These challenges include creating a secure seal due to suboptimal tube conditions, limited reach and accessibility, and the availability of suitable plugging materials in emergency situations.
Sealing Ability & Suboptimal Tube Conditions
Achieving a secure, leak-proof seal when plugging a tube, especially in high-pressure exchangers, is critical. However, the condition of the tube itself can significantly impact the success of the plug. Fouling, scaling, ovality, pitting, and wall loss are common occurrences in highly corrosive environments or vessels experiencing significant wear. These conditions can hinder the proper seating of the plug and compromise the integrity of the seal.
One-piece plugs generally do not face significant sealing challenges in extreme conditions. This is primarily due to their application in either low-pressure settings or high-pressure environments where they are welded in place, effectively overcoming any issues related to wall loss or other tube irregularities.
Similarly, two-piece plugs, typically used in chillers, are generally not severely impacted by suboptimal tube conditions. The design of the two-piece plug, when installed correctly, inherently mitigates the effects of tube defects.
Mechanical plugs, however, can face sealing challenges in suboptimal conditions, since their design relies on the plug expanding and creating a tight seal against the tube’s inner diameter. To get the most success, there are a few practices that should be followed:
- Thorough Tube Preparation: Utilize a prep brush to remove debris and create a clean, primed surface for the plug. In cases of significant irregularity or damage, reaming the tube may be necessary.
- Tube Ovality: If tube is out of round, re-rolling can restore its circularity, providing a more consistent and reliable surface for the plug to engage with.
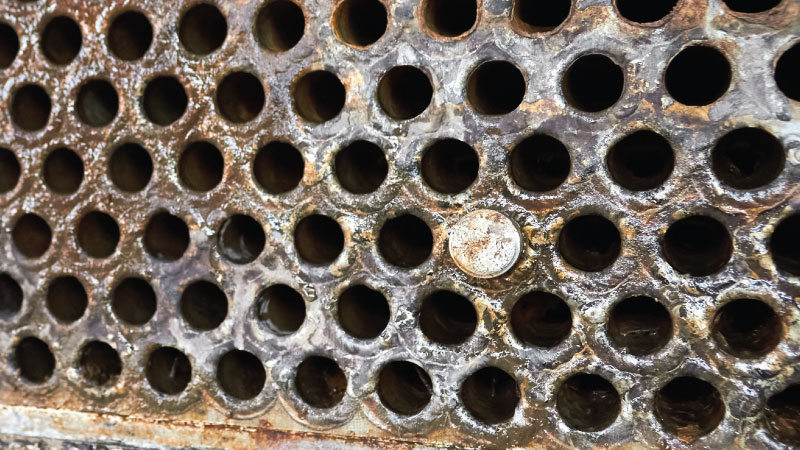
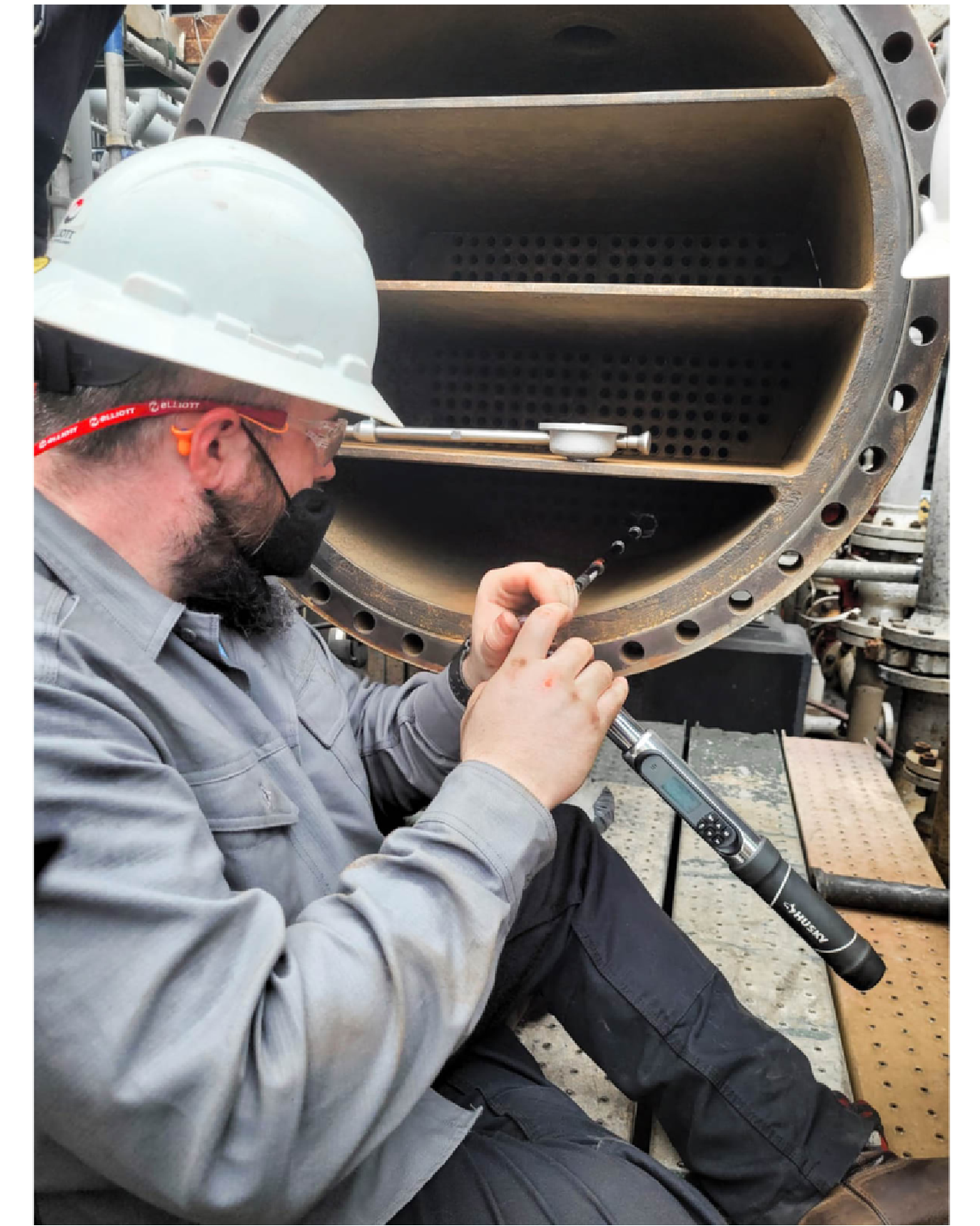
Reach & Accessibility
Limited reach and accessibility are frequent challenges encountered during plugging operations. Before starting a job, it’s crucial to carefully assess the distance to the tube sheet and its thickness.
When working through channels or headers, establishing and maintaining consistent reach is essential. Marking off a specific extension for each tool used ensures that cleaning, measuring, and plugging operations are performed consistently within the same area of the tube.
The location and configuration of the vessel will significantly influence the required tools and equipment. For example, offline-installed vessels may present different accessibility challenges compared to offline-removed vessels, potentially requiring special equipment.
Availability of Exotic Materials
Refineries and plants often utilize a wide range of vessels, many requiring specialized plug materials. Due to the potential for extended lead times and increased costs associated with procuring exotic materials, it is highly beneficial to maintain comprehensive records of all vessels on site, including their tube materials and sizes.
Establishing an on-site inventory of spare tubing, plugs, and expanders for commonly used materials can significantly reduce downtime and costs in emergency situations, enabling prompt repairs and minimizing operational disruptions.
Successful tube plugging requires a proactive approach to overcome suboptimal tube conditions, limited reach and accessibility, and the availability of exotic materials. By implementing thorough tube preparation techniques, carefully planning access routes, and maintaining a well-stocked inventory of essential materials, operators can significantly improve the efficiency and success rate of tube plugging operations, ensuring the continued safe and reliable operation of critical heat exchanger equipment.