Stress Corrosion Cracking In Heat Exchangers
Exploring The Impact and Mitigation Strategies
Premature tube failure is a leading cause of downtime in heat exchangers operating in corrosive environments. Stress corrosion cracking is a common tube failure mode in corrosive environments, impacting any number of tubes in a vessel. While stress corrosion can be difficult to identify in the field, there may be ways to reduce the likelihood of occurrence.
Stress Corrosion Cracking
Stress corrosion cracking (SCC) is a type of fracturing that occurs in metals due to a combination of tensile and residual stress in a corrosive environment. This can occur in a stainless steel, titanium, and Inconel materials, impacting any number of tubes in a vessel. Tube failure related to stress corrosion cracking will often result in retuning, as the tube is often too brittle to be plugged or repaired by other means.
Two types of stress corrosion cracking are intergranular, when cracks develop along grain boundaries, and transgranular, where the crack forms through the grains of the material. Figures 1 and 2 below illustrate each type of stress corrosion cracking in stainless steel.
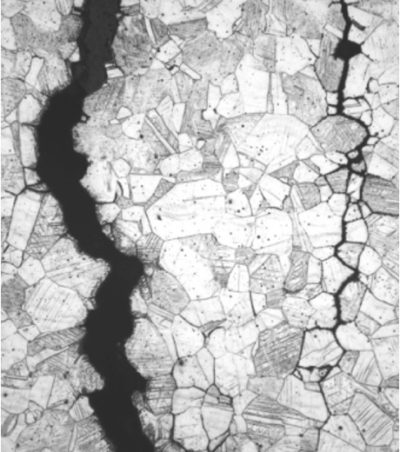
Figure 1. Intergranular Stress Corrosion Cracking.
SS Vent Valve Screw.
Credit: Lavoisier Editions
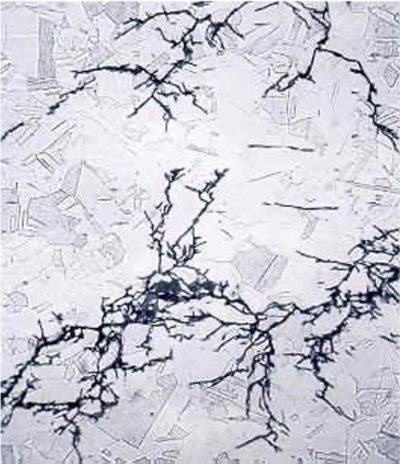
Figure 2. Transgranular Stress Corrosion Cracking.
316SS Pipe.
Credit: AMPP and Rimkus
Indicators Of Stress In Metals
There are many different sources of residual stress in heat exchanger manufacturing including welding, tube trimming, and tube expansion. Additionally, the exchanger will also experience additional stress under the operation from thermal cycling, pressure fluctuations, and vibrations.
There are two indicators of stress in metals: hardness and shear banding. Tube expansion alters the grain structure through plastic deformation, resulting in some degree of hardness change in all metals. Hardness change is more pronounced in work hardening materials like steel, with higher nickel and chrome content, and titanium.
Shear banding is another method to determine how much stress was imparted on a metal. Shear bands are a microstructure feature that develops in the grains as a result of deformation and increase with the degree of deformation. A 2013 study by Bai et. al. demonstrated a correlation between increased shear banding and stress corrosion cracking, particularly in 300 series stainless steel. Shear banding presents as lines appearing inside the grain boundaries, as illustrated in Figure 4.
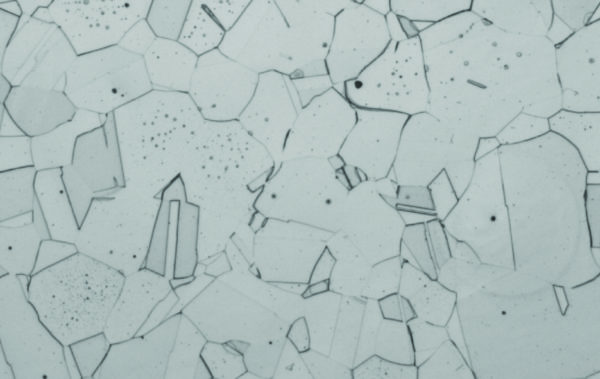
Figure 3. Undeformed area of 304 Stainless Steel.
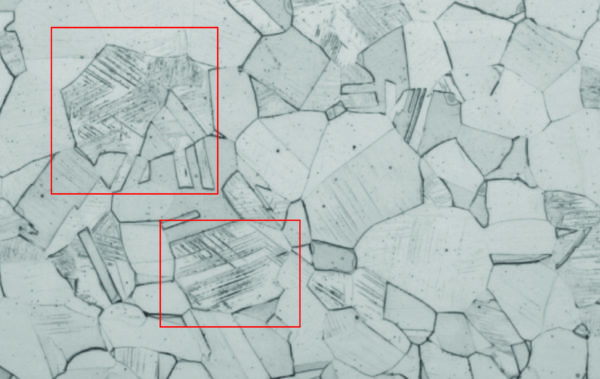
Figure 4. Deformed area of 304 Stainless Steel.
Impacts Of Stress Corrosion Cracking
Stress corrosion cracking begins in areas where the combination of stress and a corrosive environment is most severe. This localized cracking can lead to:
- Tube Leaks: Cracks can penetrate the tube wall, creating a leak path.
- Reduced Heat Transfer: Cracks can disrupt the flow of fluids, diminishing the exchanger’s efficiency.
- Catastrophic Failure: In severe cases, SCC can lead to the complete rupture of the heat exchanger, causing significant damage and potential safety hazards.
Mitigating Stress Corrosion Cracking
While there’s no guarantee of preventing stress corrosion cracking, there are steps that can be taken to reduce the likelihood of occurrence.
Material Selection
Materials with enhanced stress corrosion cracking resistance, such as low-carbon stainless steels, duplex stainless steels, and nickel alloys, should be considered based on the specific corrosive environment of the heat exchanger.
Stress Relief
Optimizing the manufacturing process to minimize the introduction of residual stress can help reduce the likelihood of SCC from occurring.
Corrosion Monitoring
Regular inspections and non-destructive testing (NDT) methods, such as eddy current or ultrasonic testing, can be employed to detect early signs of cracking.
Conclusion
Premature tube failure is one of the leading causes of downtime in the field. Reducing any avenue for tube failure can help reduce downtime and costs. As stress corrosion cracking can affect multiple tubes simultaneously, mitigating its occurrence significantly reduces the costs associated with emergency repairs or retubing efforts.
Stay tuned for the second part of this series investigating the impact of tube expansion methods on stress corrosion cracking.
References:
Bai, T., Chen, P., & Guan, K.S. (2019). How do nickel and Inconel alloys perform in caustic media. Heanjia Super Metals Co. Ltd. https://super-metals.com/news/how-do-nickel-and-inconel-alloys-perform-in-caustic-media/