The Best Bond: Choosing the Right Joining Method
Welding, brazing, and mechanical joining are all methods used to connect two or more pieces of metal. Each method has its own unique advantages and disadvantages, making it suitable for different applications. The choice of method depends on factors such as the materials being joined, the desired strength and durability of the joint, the environmental factors the joint will experience, and the cost and complexity of the process.
Welding
Welding creates a strong, permanent bond, making it ideal for critical structural applications subject to high stress. Additionally, welding can provide a seamless, leak-free joint, making it ideal for airtight or watertight applications like pressure vessels.
While welding is generally the most secure option of the three, it does require more skilled labor to execute and can be very expensive. Additionally, depending on the work environment and end use, special permitting may also be required. These restrictions can be cost prohibitive for smaller job shops or less critical manufacturing where the strength or permanence requirements may be lower.
Brazing
Brazing is a process used to join two or more metals together by melting and flowing a filler metal into the joint. This differs from welding as brazing requires a filler to join pieces together, rather than melting the joined material itself.
Brazing is advantageous when joining dissimilar materials together, as it prevents the occurrence of corrosion, or when the appearance of the pieces being joined needs to be maintained. Lower temperatures can also be used when brazing, which can be advantageous depending on the operational requirements. However, brazing can be just as expensive as welding, and may not be suited for all applications.
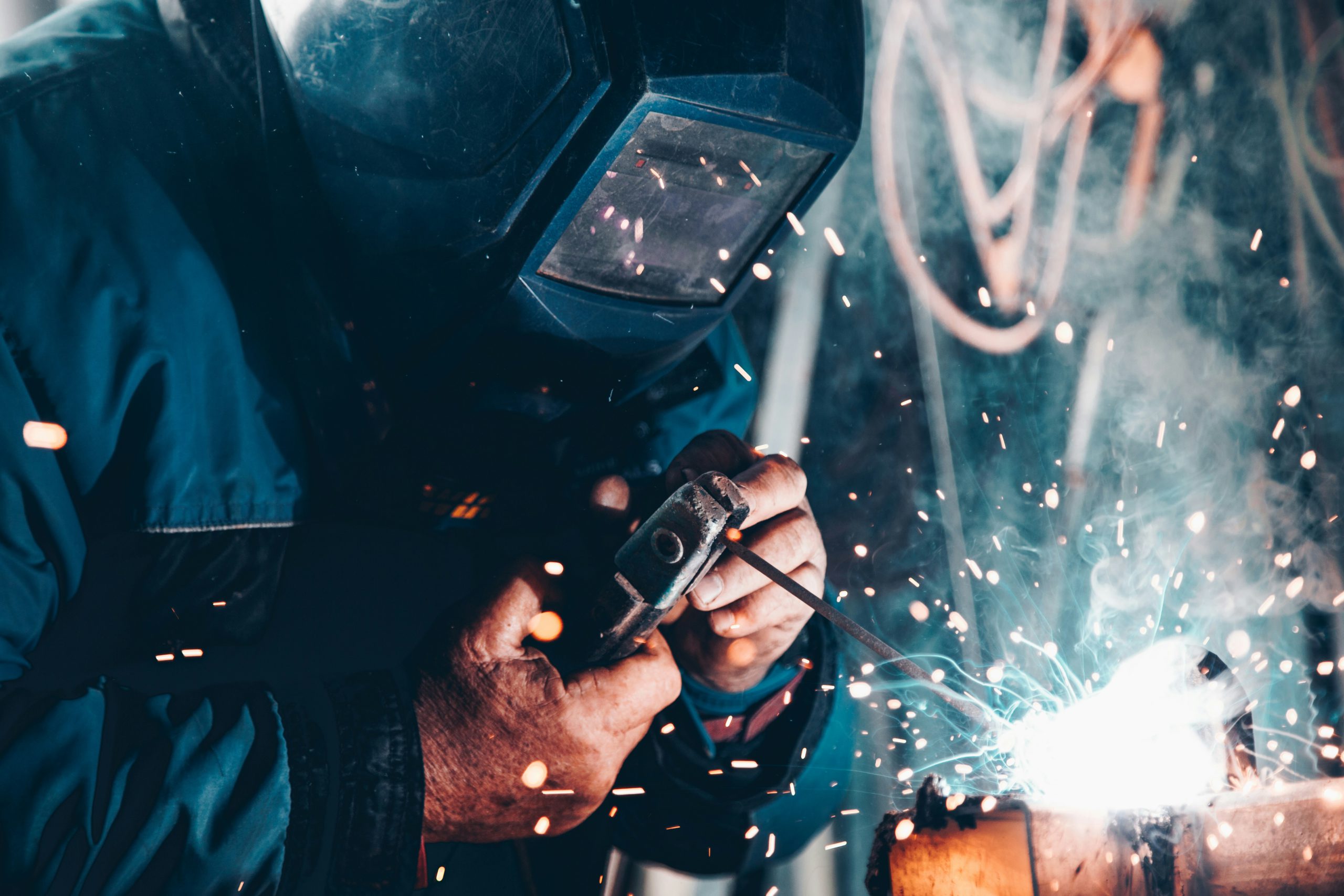
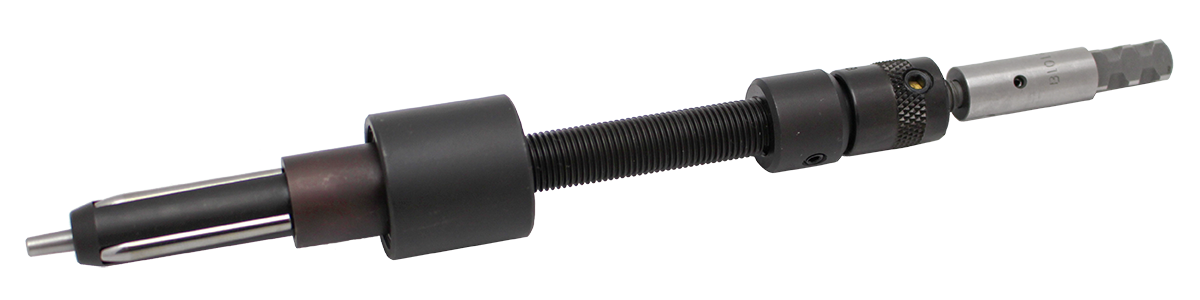
Mechanical Joining
Mechanical joining is a process of joining a tubular element to another component by compressing the outer diameter of the tube against a fixed container, generally a flange or fitting. A mechanical joining tool works by advancing a mandrel forward until the rolls expand and contact the inner wall of the tube. This process forces the material out, compressing it into the serrations/grooves on the flange ID, creating a tight seal and locking the tube in place.
This method doesn’t require any heating or specialized equipment, making it a relatively fast and simple process. Mechanical joining is best suited for applications that are subject to high vibration, changes in temperature or altitude, and high-pressure applications. This is because mechanical joints can withstand up to 20,000 pounds of hydro-static pressure without leaking or pulling apart, while welded and brazed joints can experience wear in these variable environments.
In conclusion, each joining method has its own strengths and weaknesses. Welding provides the strongest and most permanent bond but requires skilled labor and can be expensive. Brazing is a versatile method suitable for joining dissimilar materials but may not be as strong as welding. Mechanical joining is a fast and simple method that can withstand high pressure and vibration but may not be as durable as welding or brazing. The best method for a particular application depends on the specific requirements of the project.