The Science Of Tube Cutting
Geometry, materials, coatings, and application all influence the performance and life of a cutting blade. In order for it to perform well, it needs to be designed to work in a certain application. Using the incorrect cutting blade will reduce tool life and negatively impact cutting performance.
Blade Geometry
When designing a cutting blade it is important to first consider the application. Depending upon the material being cut and the use of the blade, the geometry will vary considerably. Rake angle, relief angle, and surface finish will all influence how a blade performs. Rake Angle is the angle of the cutting edge in relation to the material being cut. During the cutting process, the work piece material will shear along the cutting edge of the blade producing a thin ribbon of material known as a chip. Alterations to the rake angle will directly affect cutting loads as well as the chip produced. Longer chips can get wrapped around tools, wedged in between the cutting blade and tools/work piece, or even re-cut causing reductions in tool life and potential tool breakage. Surface Finish is the smoothness or roughness of the blade. A smooth surface finish will reduce friction during cutting and improve blade life. Overall, the geometry of the tool can greatly affect the cutting performance of a blade. If you try to cut material with a blade that’s not designed to be used in that application, you may experience a lot more wear and premature breakage of the tool.
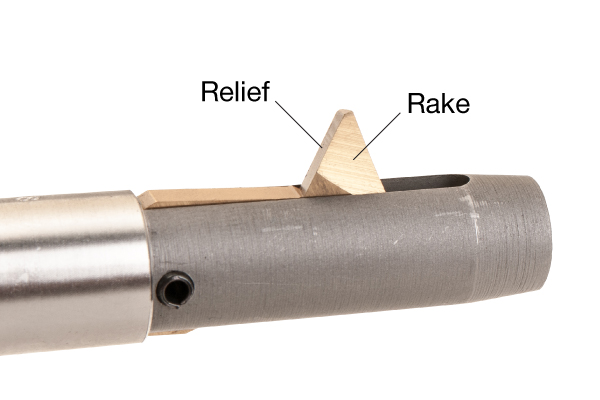

Blade Material
When selecting a blade material for an application, it is important to consider its mechanical properties. These are properties that describe how a material performs under some type of force or when exposed to different temperatures, such as hardness, red hardness and toughness.
Hardness is a material’s ability to resist scratches and abrasions. This is important when determining what materials will be wear resistant. Diamonds and ceramics would be considered hard substances because they are very difficult to scratch.
Red Hardness describes the hardness of a material when exposed to high temperatures. This is important when cutting certain materials because more heat is generated.
Toughness is a material’s ability to resist a sudden force or impact without snapping, breaking, or shattering. Softer steels or stainless steels are considered tough, because of its ability to stretch and bend, rather than break.
Ideally, you want to use a harder material when designing a cutter blade because it increases tool life and wear resistance. However, using too hard of a blade material will cause the blade to be brittle and more likely to chip or break when heavy load, vibration, or shock is applied.
Blade Coatings
There are several different coating options you can use on a cutting blade to prolong tool life. Generally, coatings are used when cutting tougher materials where excess heat may be generated.
PVD Coatings are the most common since they are extremely durable and resistant to corrosion. These are often used when you get into higher cutting rates (RPM & feeds) because more heat is generated. PVD coatings help increase tool life by preventing the material from sticking to the cutting edge.

Signs Of Wear
There are several different types of wear that you should look out for to ensure the best performance of the tool.
Chipping occurs along the cutting edge of the blade. A worn cutting edge will increase the load and increase the probability of breakage.
Flank Wear occurs on the back edge of the blade from rubbing the section of material that has already been cut.
Crater Wear occurs when the chip hits the rake face and wears down blade material.
Checking for wear regularly will ensure that you get the best performance out of the blade. As a blade wears it will increase the load and the probability of breakage. If a blade breaks it can damage the tool and the material being cut. As a result, it is important to replace blades at the first signs of wear.
Overall, there are many different factors that can influence a cutting blade’s performance. Depending upon the material being cut and the method in which it will be cut, the design of the blade may vary considerably. Therefore, it is important to gather this information prior to starting a project to make sure you have the correct tools on hand.