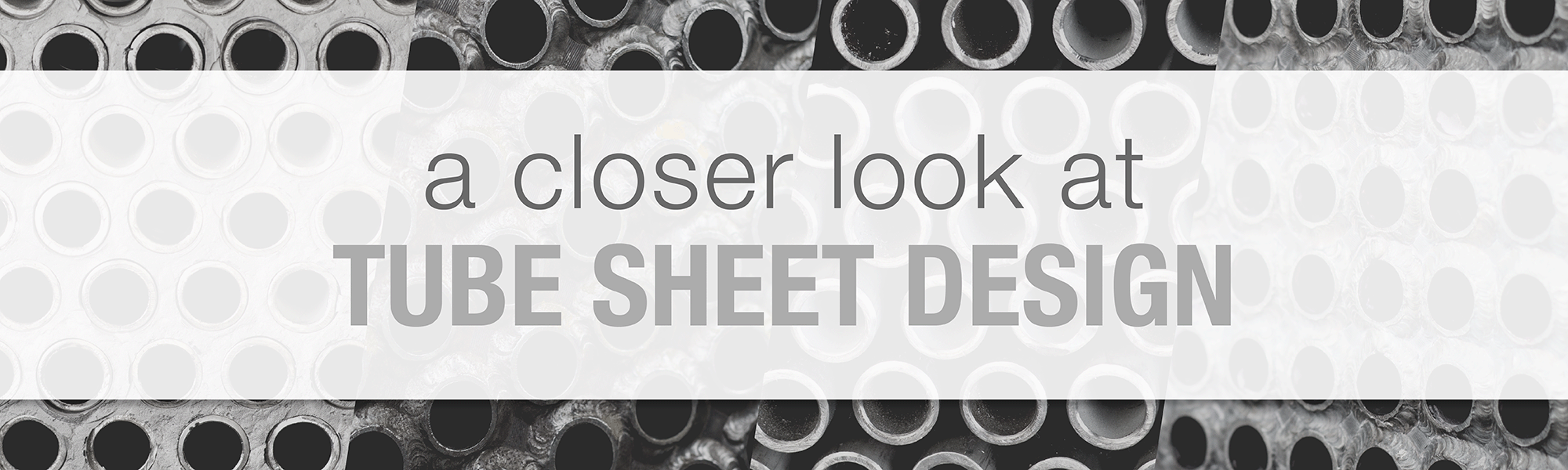
A Closer Look At Tube Sheet Design
How material and pitch impact the quality of expansion
As customers look towards increasing the heat transfer efficiency of a vessel, it’s forcing many customers to reevaluate their fabrication process. The use of materials like Nickel, Hastelloy, Inconel and other exotic materials in both tubes and tube sheets have become a lot more common, as they are more resistant to corrosion. Additionally, manipulating tube patterns and tube pitch to increase the number of tubes in a vessel helps to increase surface area and flow. While these modifications are beneficial to creating a long-lasting heat exchanger, it does create some challenges for tube expansion.
Tube Patterns & Ligament Distance
Tube patterns describe how the tube holes are distributed through the tube sheet. The most common patterns are triangle, square, and rotated square.
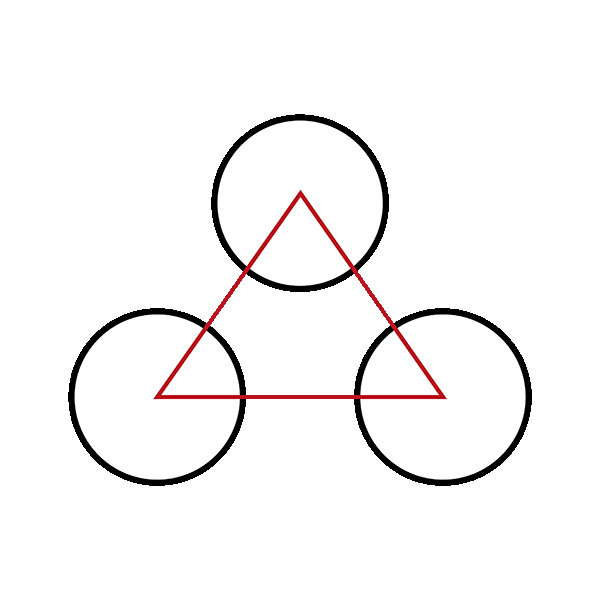
Triangle Tube Pitch
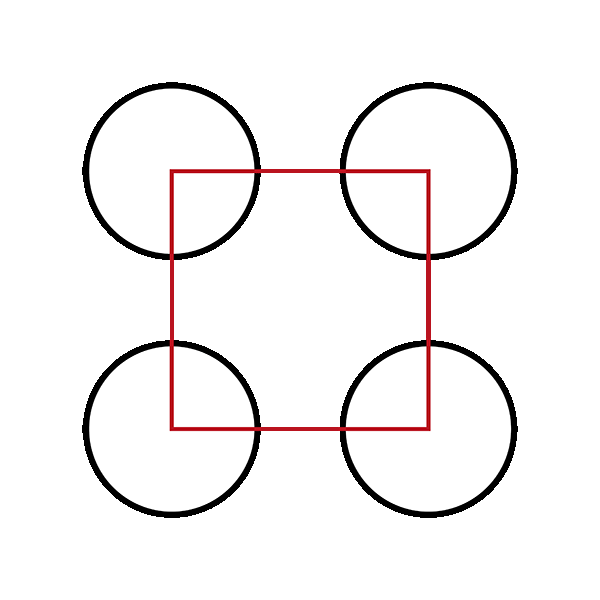
Square Tube Pitch
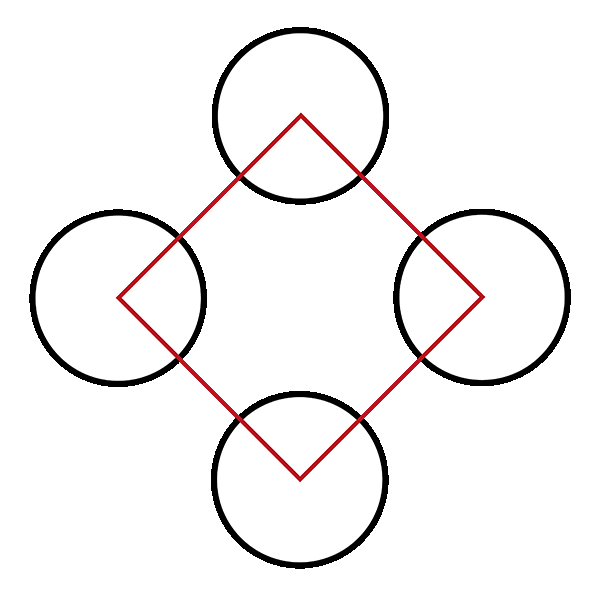
Rotated Square Tube Pitch
While the pattern is up to the manufacturer, the chosen pattern can be important depending on the ligament distance specified. The ligament distance is the distance from the outside of one tube sheet hole to the outside of the next tube sheet hole. Similarly, the tube pitch is the distance from the center of one tube sheet hole to the center of the next tube sheet hole.
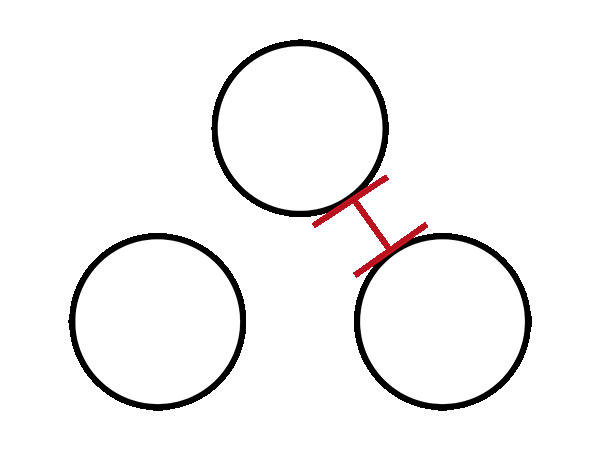
Ligament Distance
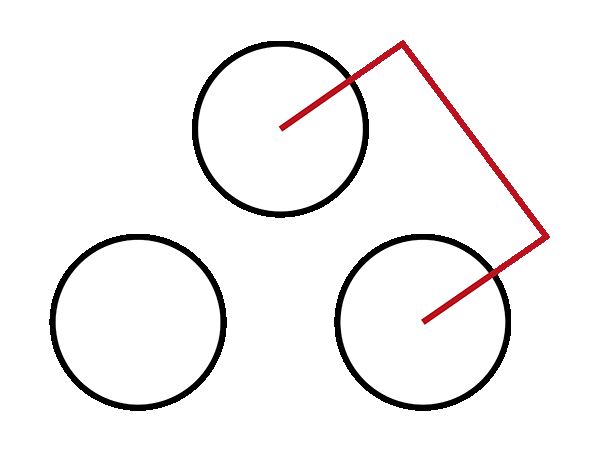
Tube Pitch
To increase the number of tubes in a tube sheet, many manufacturers will specify the minimum ligament distance. Generally, this distance is calculated by multiplying the tube OD by a fixed multiplier, such as 1.25. The multiplier value is set by TEMA (Tubular Exchangers Manufacturers Association) and will vary based on the tube size. When it comes to tube expansion, tube joint leak issues are most likely going to occur in tube sheets that have a triangular pitch and a minimum ligament distance.
Tube & Tube Sheet Material Yields
The other factor that can impact tube expansion is the tube and tube sheet material. Historically, a lot of vessels were constructed so the tube material and tube sheet material were complimentary, but not equal. This is ideal for tube expansion because the yield strength of the tube sheet is higher than that of the tube, allowing the tube to expand properly.
Yield strength describes the force required to move a material out of its elastic state when it’s able to stretch and hit plastic deformation, ie. when the material is permanently deformed and unable to return to its original shape. Achieving the plastic state is crucial during expansion because it’s required to create a leak free mechanical joint. If the tube material has a lower yield than the tube sheet, the tube sheet can help hold the tube in place once it hits plastic deformation. If the tube sheet is unable to work against the force placed on the tube, it can result in an uneven expansion.
In recent years, many customers are specifying like materials for the tube sheet and tubes, such as Inconel 625 or SA240. This is problematic because the yield strength between the two materials will be identical, meaning the tube expander will be unable to provide concentric expansion since the tube and tube sheet are expanding at the same rate. As a result, the tube and tube sheet hole can start to triangulate, resulting in leaks at hydro.
In situations where the materials are the same or the tube yield strength is higher than the tube sheet, it’s important to review the application with your tooling supplier. Depending on the tube pitch, materials, and tube size, multi roll 4 or 5 roll tube expanders may be required to overcome these challenges.
Overcoming Challenges with A Close Pitch
If similar materials are used in a close tube pitch, there are some methods that can be used to get a better mechanical joint.
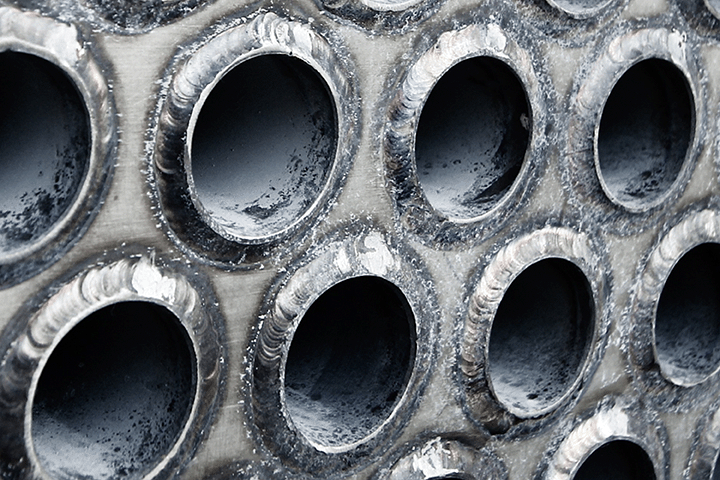
Seal Weld
In these cases seal welding is almost always required. This will ensure that the tubes will not leak should there be any inconsistencies in the expansion process. Additionally, the weld will protect the mechanical joint created by the expansion process and assist with heat dissipation across the tube sheet.
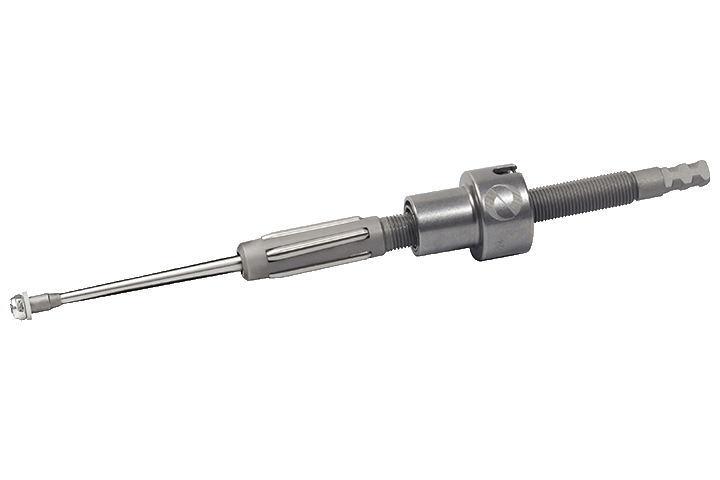
Use a 4 or 5 Roll Expander
Since the similar yields can result in an out of round roll, using a 4 or 5 roll tool can help to prevent that by increasing the amount of surface area being worked at a time. The additional rolls will help prevent the metal from triangulating. The added rolls help interrupt the geometry to promote even expansion of the tube being expanded and not interrupting the joint integrity of adjacent tubes.
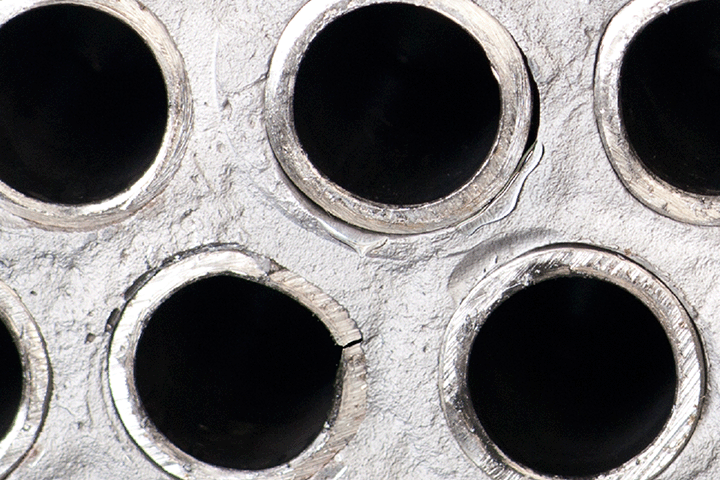
Low Wall Reduction and Low Torque
In this situation it’s important not to overwork the material, as it can impact the ligament distance between tubes and potentially result in leaks across the vessel. To avoid this, it’s recommended to roll to the lowest wall reduction that provides a leak free joint at a lower torque value.
Overall, as the market shifts towards increasing efficiency and vessel life, there will be impacts to the fabrication process. As exotic materials are more commonplace, it’s important to understand how the tube expansion process may be impacted, so that leak free joints can be achieved. Utilizing 4 or 5 roll expanders, lower wall reduction, coupled with seal welding will ensure a better tube expansion process.