Tube Sheet Grooves & How They Impact Expansion
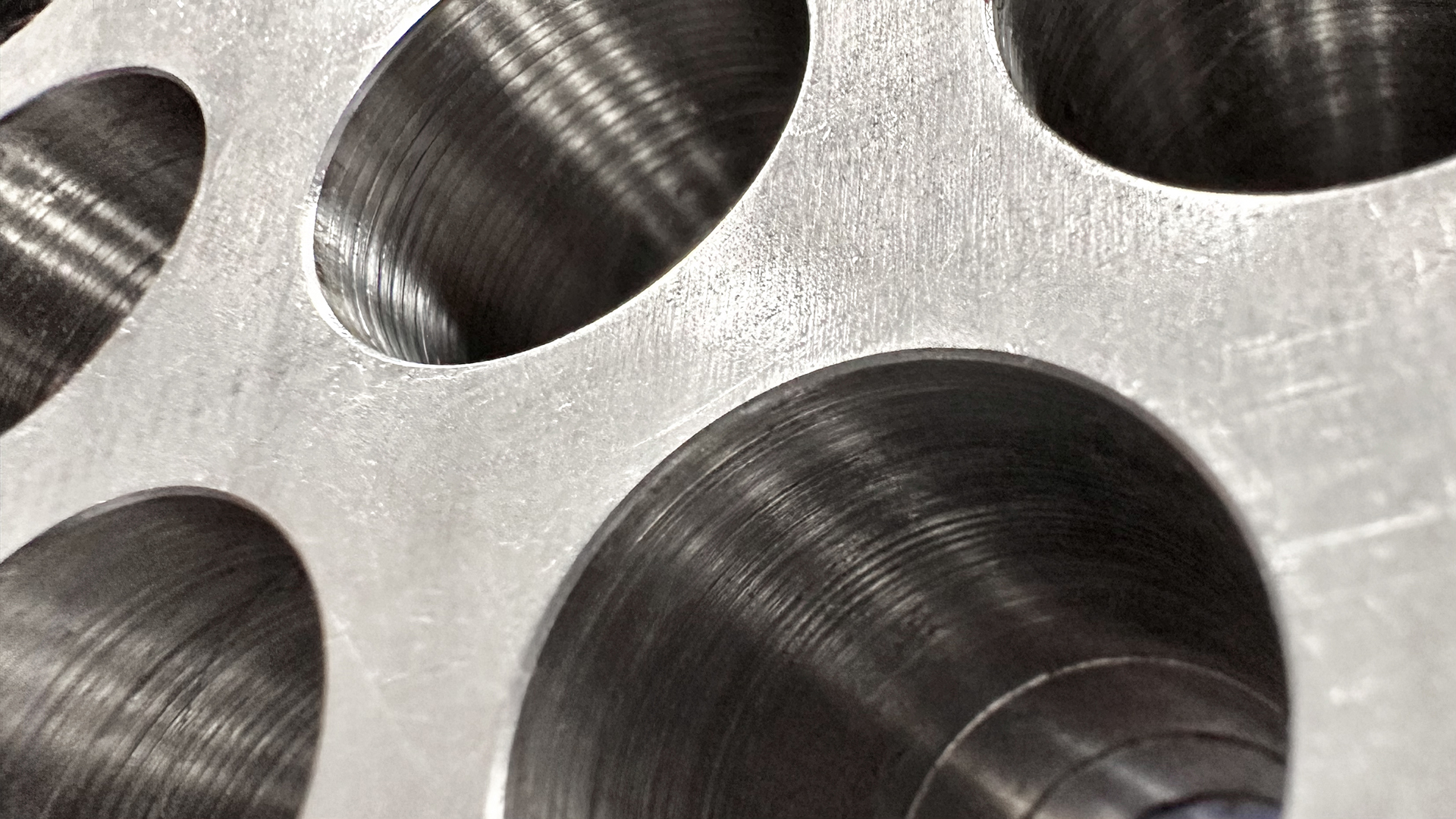
Grooved tube sheets are the standard in most shell and tube heat exchanger applications. Providing both leak protection and improving the tube-to-tube sheet joints, grooves play an important role in prolonging the life of a tube and the efficiency of a vessel. However, in few applications where grooves are not required, there can be challenges during the tube expansion process. This article will discuss the purpose of tube sheet grooves, industry specifications, and challenges that can occur in applications where grooves are not use.
Leak Protection & Joint Strength
Tube Sheet grooves are serrations that are made in the tube sheet hole during manufacturing. Created using a CNC machine or a radial arm drill, these serrations are used to add additional leak path protection and improve tube to tube sheet joint strength. This is because the groove creates a path for the tube material to expand into, creating a tight mechanical joint. The use of grooves also allow operators to expand to a higher wall reduction percent, improving the effectiveness of the expansion in preventing leak paths from forming.
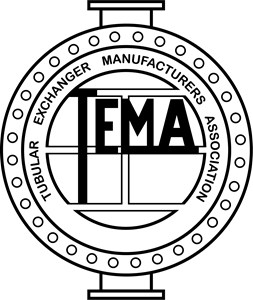
TEMA Specifications
Tubular Exchanger Manufacturers Association (TEMA) is a trade association made up of shell and tube heat exchanger manufacturers. The organization provides specifications for the fabrication of new shell and tube heat exchangers to ensure quality and consistency. When it comes to grooves, TEMA specifies that expanded joints for tubes 5/8” OD and larger shall be machined with 1 – 2 grooves depending on the tube sheet thickness. For tube sheets 1” and below, 1 groove is sufficient, while thicker tube sheets require 2 grooves.
In terms of groove placement, TEMA suggests that tube sheet grooves be 1/8” wide with a ¼” gap in-between. However, they leave the specific groove size and arrangement to the manufacturer’s discretion, based on the vessel type and prior experience.
Exceptions To the Rule
While most shell and tube applications will have grooved tube sheets, there are some exceptions. First, any application with strength welded tube to tube sheet joints does not require the use of grooves. This is because the strength weld is acting in a similar manner to prevent leaks and provide additional joint strength. Additionally, evaporators may not require tube sheet grooves depending on the type and the maximum allowable working pressure (MAWP). Since many evaporators have a very low working pressure, ~30-40 PSI, the benefits of grooves are not necessary. Instead, the vessel design may prioritize ease of maintenance and cost effectiveness instead.
Potential Challenges Expanding Un-Grooved Tube Sheets
One of the biggest challenges when expanding tubes without a grooved tube sheet is the potential for tube elongation. While this can occur in many different applications, it happens a lot quicker without grooves because the tube material has nowhere to go. Without a path for the material to expand into, the wall reduction that can be achieved in these applications is significantly lower than those with grooves. In general, customers can expect to see 3 – 4% of wall reduction depending on the type of tube and tube sheet material. Once that amount has been exceeded, any additional wall reduction will be a direct result of tube elongation. If the tubes grow too much, it can compromise the quality of the mechanical joint and cause damage to the tube or tube sheet hole.
In order to avoid excess elongation, operators are encouraged to start at a lower wall reduction and work their way up. This allows for additional room to re-roll the tube joints if they’re under expanded at the time of hydro. Additionally, when expanding tubes without grooved tube sheet holes, it’s important to remember that measuring can be misleading. In most cases, it’s highly encouraged to measure the tubes pre and post expansion. While this is still the case in these applications, it’s important to keep in mind that the number may not indicate more wall reduction. At a certain point, as the percent wall reduction increases, any larger measurement in the tubes is likely a result of elongating rather than additional wall reduction.
A common method of identifying tube elongation is to visually look for growth. This can be done by monitoring the projection on the opposite side of the vessel, or by tracking the starting point of the tube. For example, some manufacturers will mark the OD of the tube where it meets the back side of the tube sheet. This allows operators to visually see if the tube starts to elongate, because the marked portion will move further and further away.
Overall, a majority of heat exchanger applications will have grooved tube sheet holes. This is because grooves improve leak protection and the tube-to-tube sheet joint. However, in some applications where grooves are not used, it’s important to pay close attention to the wall reduction achieved. Overrolling can occur if wall reduction targets are not adjusted to the application, as tube elongation is more likely. To avoid complications, it’s important to be mindful of tube sheet grooves and the impact that they can have on the quality of the expansion.