What Is Mechanical Joining?
In manufacturing there are numerous applications where tubes need to be joined to flanges or fittings to create a leak proof seal. One common example is joining flexible couplings and hose assemblies for use in aerospace and hydraulic assemblies in heavy industry. While there are a few different ways to achieve the required seal, mechanical joining is one of the most consistent and low-cost methods available. In this article, we will discuss what mechanical joining is, how it compares to other methods, and some common industry applications.
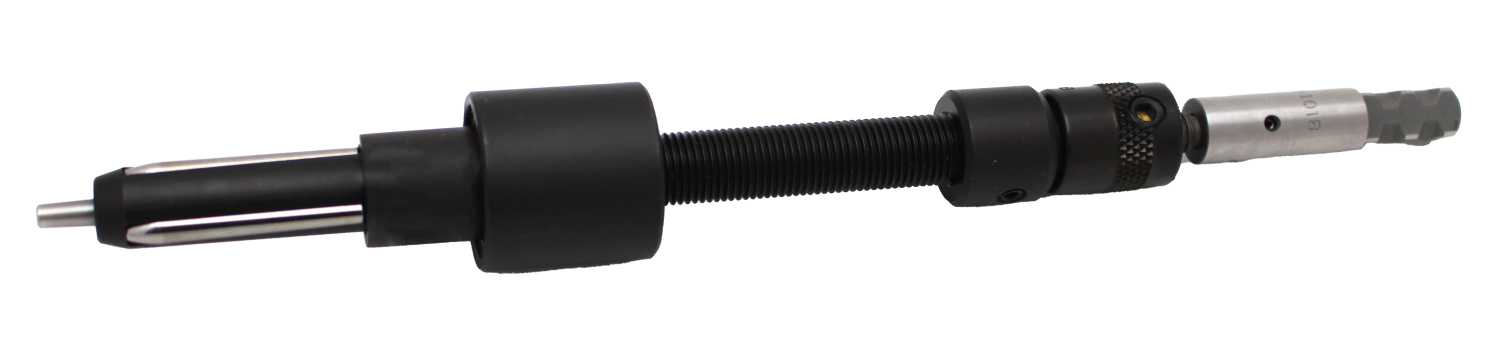
The Process
Mechanical joining is a process of joining a tubular element to another component by compressing the outer diameter of the tube against a fixed container, generally a flange or fitting. Virtually any metal can be mechanically joined, including steel, stainless, aluminum, titanium, copper, Inconel, etc. Consisting of a mandrel, roll set, and cage, the mechanical joining tool works by advancing the mandrel forward until the rolls expand and make contact with the inner wall of the tube. This process forces the material out, compressing it into the serrations on the flange ID, creating a tight seal and locking the tube in place.
There are two methods for mechanically joining two components: rolling to torque and rolling to diameter. Depending on the part specifications, the amount of expansion is going to vary. Rolling to a torque is going to be the most accurate in terms of guaranteeing consistent joints, as it accounts for any variations in tube size, thickness, and component ID. On the other hand, rolling to a diameter will ensure that a consistent finished ID size is achieved.
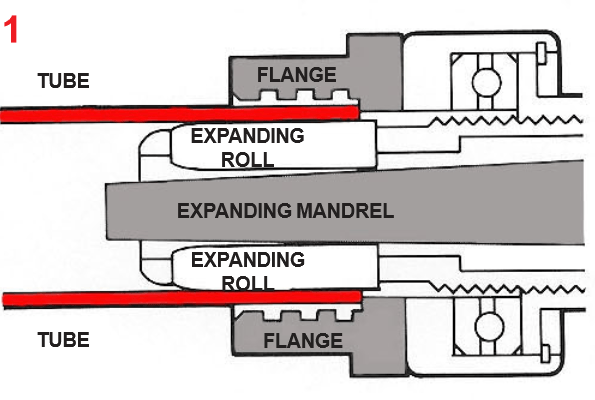
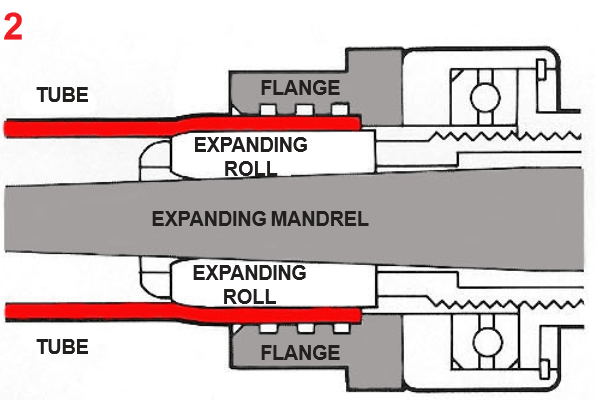
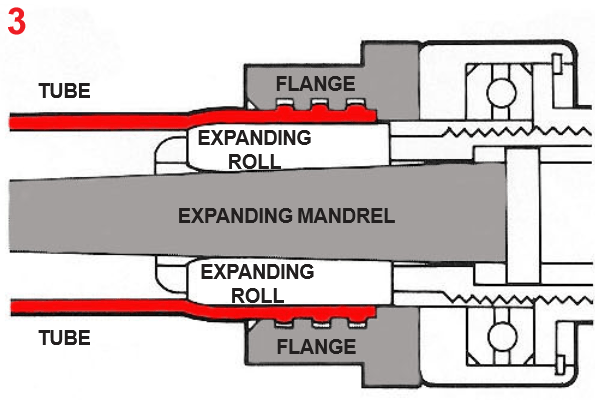
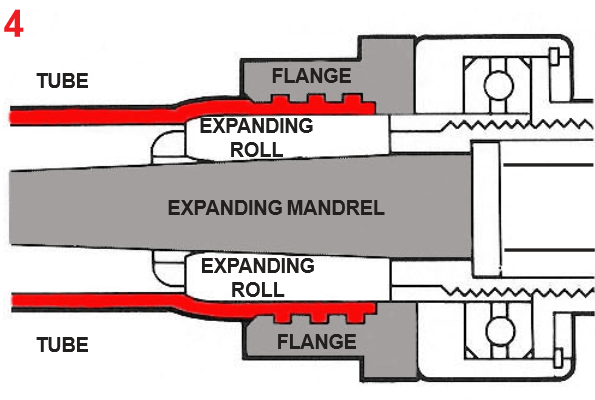
Benefits Of Mechanical Joining
Mechanical joining is best suited for applications that are subject to high vibration, changes in temperature or altitude, and high-pressure applications. This is because mechanical joints can withstand up to 20,000 pounds of hydro-static pressure without leaking or pulling apart. Additionally, the process of mechanical joining is generally lower cost and easier to perform when compared to welding, brazing, or crimping.
In addition to creating a leak-free joint, mechanical joining is also easy to operate and can be used with a variety of installation sources. From handheld motors to assisted rolling systems to CNC machines, there are many power options available.
Common Applications
Mechanical joining is used in a wide variety of industries such as fluid power, heavy equipment, aerospace, and automotive. Some common applications are hydraulic fittings, transmission blocks, and fluid lines in aircraft.
Overall, mechanical joining is a quick and easy process for creating leak free joints between tubular products and fittings, when compared to welding or brazing operations. This makes it well suited for high vibration and high-pressure applications like aerospace and heavy equipment.
Contact us to learn how mechanical joining may benefit your application.